Offshore Pipeline Solutions: Why SSAW Pipes Are the Best Choice
March 18, 2025
Share This Article
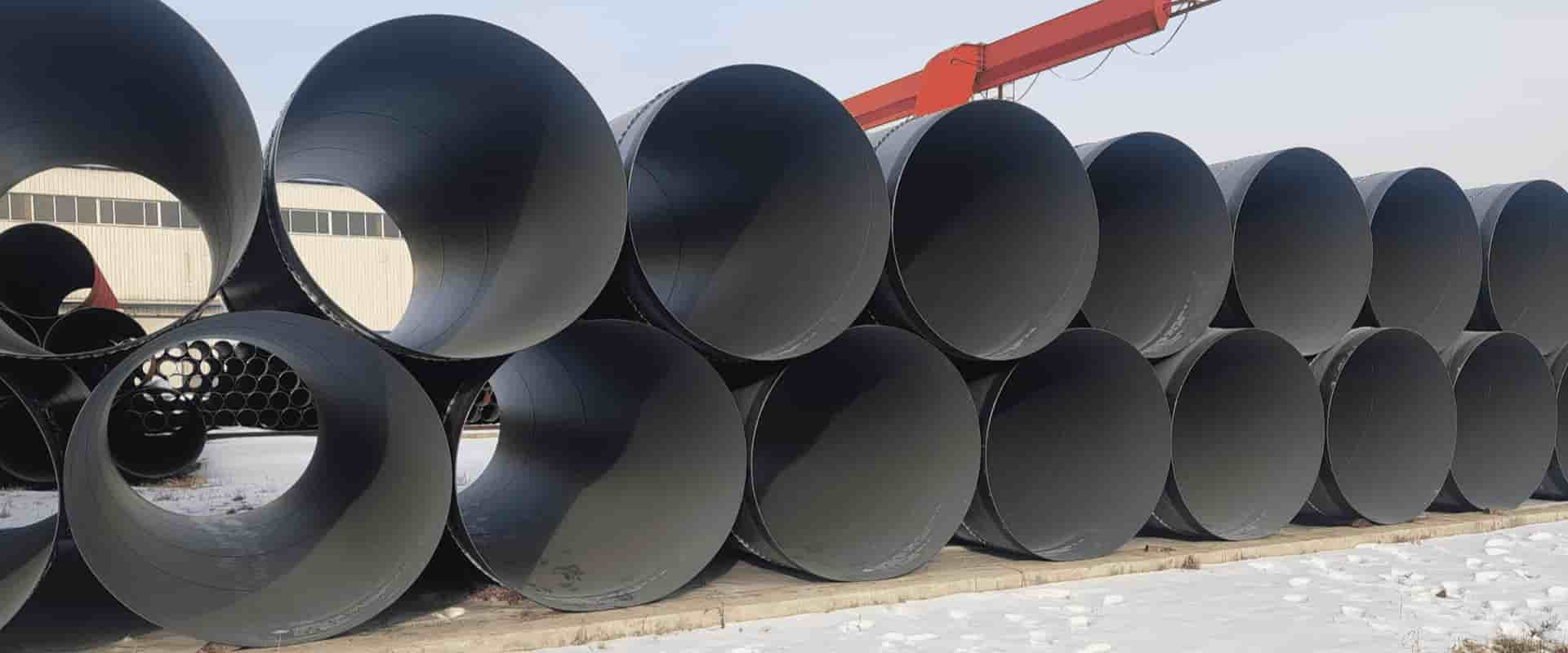
1. Introduction: The Critical Role of SSAW Pipes in Offshore Pipeline Infrastructure
In the demanding world of offshore energy infrastructure, the selection of pipeline materials represents one of the most consequential decisions facing project engineers, procurement specialists, and operation managers. As global energy demands continue to rise, offshore oil and gas extraction, underwater power transmission, and marine resource development have intensified, creating unprecedented challenges for pipeline systems that must withstand extreme conditions while maintaining operational integrity.
Spiral Submerged Arc Welded (SSAW) pipes have emerged as the premier solution for offshore pipeline applications, offering a compelling combination of structural integrity, cost-effectiveness, and versatility that makes them increasingly the preferred choice for wholesale buyers, major contractors, and engineering firms specializing in offshore infrastructure.
The Offshore Pipeline Market Landscape
The global offshore pipeline market is projected to reach $18.9 billion by 2026, growing at a CAGR of 6.7% from 2021 to 2026. This growth is driven by several factors:
Market Driver | Impact on Pipeline Requirements |
---|---|
Deepwater exploration expansion | Need for high-pressure resistant materials |
Renewable energy development | Increased demand for water intake/outflow systems |
Aging infrastructure replacement | Focus on corrosion-resistant, long-lifecycle solutions |
Environmental regulations | Requirement for leak-proof, environmentally secure systems |
Cost optimization pressures | Demand for economical yet high-performance materials |
For wholesale buyers and procurement specialists in this sector, understanding the technical advantages of SSAW pipes is essential for making informed purchasing decisions that balance performance requirements with budget constraints.
Why Material Selection Matters in Offshore Environments
Offshore pipeline systems face unique challenges that make material selection particularly critical:
- Environmental Exposure: Constant contact with seawater creates aggressive corrosion conditions
- Pressure Variations: Deep-water installations must withstand enormous hydrostatic pressures
- Temperature Fluctuations: Thermal expansion and contraction stress pipeline integrity
- Seabed Movement: Underwater currents and seismic activity create mechanical stress
- Installation Challenges: Deployment in marine environments requires robust, reliable materials
SSAW pipes address these challenges through their unique manufacturing process, material composition, and structural design. For companies seeking wholesale pipeline solutions for offshore projects, SSAW technology offers compelling advantages that we’ll explore throughout this article.
The Evolution of Offshore Pipeline Materials
The development of offshore pipeline materials has evolved significantly over the decades:
- 1950s-1960s: Early offshore pipelines primarily used seamless pipes with limited diameter options
- 1970s-1980s: Introduction of longitudinal welded pipes expanded diameter capabilities
- 1990s-2000s: Development of advanced SSAW manufacturing improved weld quality and reliability
- 2010s-Present: Modern SSAW pipes with enhanced steel grades and coating technologies dominate the market
Today, industry leaders like WUZHOU are pushing the boundaries of what’s possible with SSAW pipe technology, producing pipes that meet the most stringent international standards while offering cost advantages that appeal to wholesale buyers and project developers worldwide.
2. Understanding SSAW Pipe Technology: Manufacturing Process and Advantages
To appreciate why SSAW pipes excel in offshore applications, it’s essential to understand the sophisticated manufacturing process that creates these high-performance pipeline components.
The SSAW Manufacturing Process: Precision Engineering at Scale
The production of Spiral Submerged Arc Welded pipes involves a series of carefully controlled steps that transform high-quality steel coil into finished pipes with exceptional structural properties:
- Raw Material Selection: The process begins with premium steel coil selection, typically using grades like X42, X52, X56, X60, X65, X70, or X80 depending on the application requirements.
- Edge Preparation: The steel coil edges are precisely milled to create optimal welding surfaces.
- Forming Process: The steel strip is fed into a forming machine at a specific angle, creating a spiral shape as it moves through the production line.
- Inside Welding: The first submerged arc welding pass occurs on the inside of the spiral seam, ensuring complete penetration.
- Outside Welding: A second submerged arc welding pass on the outside creates a complete weld that fully integrates the steel edges.
- Heat Treatment: Controlled heat application removes residual stress from the welding process.
- Hydrostatic Testing: Each pipe undergoes pressure testing at levels exceeding operational requirements.
- Non-Destructive Testing: Ultrasonic or X-ray inspection ensures weld integrity throughout the pipe length.
- Coating Application: Specialized coatings provide additional corrosion protection for offshore environments.
WUZHOU, as a leading manufacturer in this field, has perfected this process across its 11 dedicated spiral pipe production lines, enabling production of pipes with diameters ranging from 219mm to 3500mm and wall thicknesses from 5mm to 25.4mm—ideal specifications for diverse offshore applications.
Technical Advantages of SSAW Pipes in Offshore Applications
SSAW pipes offer several distinct technical advantages that make them particularly well-suited for offshore environments:
1. Superior Pressure Resistance
The spiral weld configuration creates an inherently stronger structure than traditional longitudinal welds:
Pressure Rating | SSAW Performance |
---|---|
Standard pressure applications | Excellent (up to 30% stronger than equivalent LSAW) |
High-pressure deepwater | Outstanding with appropriate steel grade selection |
Pressure cycling resistance | Superior due to spiral stress distribution |
2. Enhanced Structural Flexibility
The spiral welding pattern distributes stress more evenly across the pipe body:
- Tensile Strength: The helical weld provides better resistance to longitudinal stress
- Bending Resistance: Improved ability to handle installation stresses during marine deployment
- Impact Absorption: Better performance against external impacts and underwater debris
3. Optimized Material Utilization
The spiral manufacturing process offers significant material efficiency advantages:
- Reduced waste during production (typically 5-8% less than LSAW alternatives)
- Lower raw material requirements for equivalent strength specifications
- Ability to produce larger diameter pipes from standard-width steel coil
4. Cost-Effective Production at Scale
For wholesale buyers and project developers, the economic advantages are compelling:
- Lower per-meter costs for equivalent performance specifications
- Reduced production lead times for large-volume orders
- Efficient transportation and handling due to optimized weight-to-strength ratio
WUZHOU’s SSAW Manufacturing Excellence
WUZHOU has established itself as an industry leader in SSAW pipe manufacturing through:
- Advanced Production Technology: State-of-the-art manufacturing lines with digital process controls ensure consistent quality.
- Material Science Expertise: Collaboration with steel suppliers to develop optimal grade specifications for offshore applications.
- Quality Control Rigor: Every spiral steel pipe undergoes comprehensive testing:
- Hydrostatic pressure testing
- Ultrasonic examination
- X-ray inspection
- Mechanical property verification
- International Certification: WUZHOU’s manufacturing processes are certified to the highest international standards:
- API 5L certification from the American Petroleum Institute
- EU standard compliance
- ISO 9001 and ISO 14001 certifications
- Production Capacity: With an annual output of 400,000 tons across multiple production facilities, WUZHOU can meet the supply demands of major offshore projects worldwide.
3. Key Performance Metrics: How SSAW Pipes Outperform Alternatives in Offshore Environments
When evaluating pipeline solutions for offshore applications, procurement specialists and project engineers must consider multiple performance factors that directly impact project success. SSAW pipes demonstrate exceptional performance across the key metrics that matter most in challenging marine environments.
Critical Performance Parameters for Offshore Pipelines
Mechanical Performance Comparison
The table below compares SSAW pipes against common alternatives across critical mechanical parameters:
Performance Metric | SSAW Pipes | LSAW Pipes | Seamless Pipes | ERW Pipes |
---|---|---|---|---|
Burst Pressure Resistance | Excellent | Good | Excellent | Moderate |
Collapse Resistance | Very Good | Good | Excellent | Moderate |
Tensile Strength | Excellent | Good | Very Good | Good |
Bending Flexibility | Excellent | Moderate | Good | Moderate |
Impact Resistance | Very Good | Good | Excellent | Fair |
Fatigue Resistance | Very Good | Good | Excellent | Moderate |
Weight-to-Strength Ratio | Excellent | Good | Moderate | Good |
Corrosion Resistance and Longevity
Offshore environments present extreme corrosion challenges that directly impact pipeline lifecycle costs:
- External Corrosion Protection: SSAW pipes can be manufactured with specialized coatings:
- 3-layer polyethylene (3LPE)
- Fusion-bonded epoxy (FBE)
- Concrete weight coating (CWC)
- Polypropylene coatings
- Internal Corrosion Resistance: Available with:
- Internal epoxy linings
- Liquid epoxy coatings
- Cement mortar lining
- Lifespan Comparison:
Pipeline Type | Average Expected Service Life (Years) | Maintenance Frequency |
---|---|---|
SSAW with advanced coatings | 30-50+ | Low |
LSAW with standard protection | 25-40 | Moderate |
Seamless with coating | 30-45 | Low-Moderate |
ERW with coating | 20-35 | High |
WUZHOU’s SSAW pipes are engineered for exceptional durability, with advanced coating options applied on their 2 specialized coating and lining production lines. This comprehensive approach to corrosion protection ensures optimal performance throughout the operational lifetime of offshore installations.
Installation Performance in Marine Environments
Offshore pipeline installation presents unique challenges that SSAW pipes are particularly well-equipped to address:
1. Installation Method Compatibility
SSAW pipes demonstrate excellent performance across all major offshore installation methods:
- S-Lay Installation: The spiral weld configuration provides superior resistance to the bending stresses encountered during S-lay operations.
- J-Lay Installation: SSAW pipes maintain structural integrity under the high tension loads experienced during deep-water J-lay installations.
- Reel-Lay Installation: For smaller diameter requirements, SSAW pipes can be manufactured with specifications suitable for reel-lay operations.
- Towing Installation: The robust construction of SSAW pipes makes them ideal for towing installation methods that subject the pipeline to variable tension and pressure.
2. Handling and Deployment Efficiency
For project managers and installation contractors, SSAW pipes offer practical advantages that directly impact project timelines and costs:
- Joining Efficiency: Field welding of SSAW pipes is streamlined due to consistent end preparation and dimensional stability.
- Weight Optimization: The efficient material usage of spiral welding creates pipes with an optimal strength-to-weight ratio, reducing handling challenges.
- Length Flexibility: SSAW manufacturing allows for production of longer individual pipe sections, reducing the number of field welds required.
- Dimensional Consistency: WUZHOU’s manufacturing precision ensures uniformity across large production runs, minimizing field adjustments.
Performance Under Extreme Conditions
Offshore pipelines must withstand environmental extremes that test the limits of material performance:
1. Deep Water Performance
As exploration and production move to ever-greater depths, pipeline materials face increasing challenges:
Water Depth | Pressure Conditions | SSAW Performance |
---|---|---|
Shallow (<300m) | Moderate external pressure | Excellent with standard specifications |
Mid-depth (300-1000m) | High external pressure | Very good with enhanced wall thickness |
Deep (1000-2000m) | Very high external pressure | Good with specialized grades and design |
Ultra-deep (>2000m) | Extreme external pressure | Viable with custom engineering and materials |
WUZHOU’s manufacturing capabilities include production of heavy-wall SSAW pipes specifically engineered for deepwater applications, with wall thicknesses up to 25.4mm and premium steel grades providing the necessary pressure resistance.
2. Temperature Extremes
Offshore pipelines often transport products at temperature extremes that stress material properties:
- High-Temperature Applications: SSAW pipes maintain structural integrity in applications up to 120°C with appropriate material selection.
- Low-Temperature Performance: Using specialized steel grades, SSAW pipes deliver excellent toughness at temperatures as low as -40°C.
- Thermal Cycling Resistance: The spiral weld pattern distributes thermal expansion stress more effectively than longitudinal welds.
3. Environmental and Regulatory Compliance
Modern offshore projects face increasingly stringent environmental requirements:
- Leak Prevention: WUZHOU’s rigorous testing protocols, including 100% hydrostatic testing and ultrasonic inspection, ensure pipeline integrity and minimize environmental risks.
- Material Traceability: Complete documentation of raw materials and manufacturing processes meets or exceeds international regulatory standards.
- Environmental Certification: ISO 14001 certification demonstrates WUZHOU’s commitment to environmentally responsible manufacturing practices.
- End-of-Life Considerations: SSAW pipes are fully recyclable, supporting sustainable project lifecycle management.
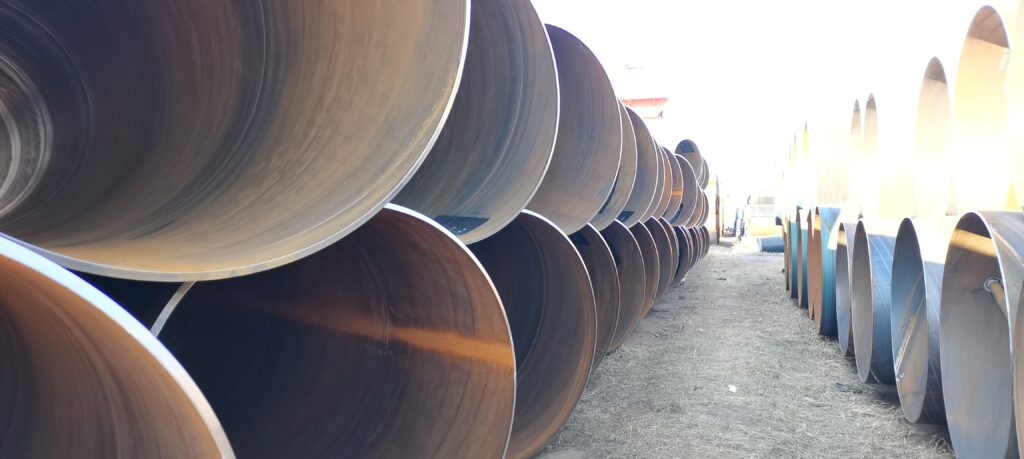
The WUZHOU Advantage in Performance Metrics
WUZHOU’s SSAW pipes consistently outperform industry standards across critical performance metrics, offering wholesale buyers and project developers a compelling value proposition:
- Manufacturing Excellence: State-of-the-art production facilities with 11 spiral pipe production lines ensure consistent quality and performance.
- Comprehensive Testing: Every pipe undergoes rigorous quality inspection, including hydrostatic testing, ultrasonic examination, and X-ray inspection.
- Material Expertise: Strategic partnerships with premium steel suppliers ensure optimal raw material properties for offshore applications.
- International Standards Compliance: Certifications including API 5L and ISO 9001 validate WUZHOU’s commitment to producing pipes that meet or exceed international performance standards.
- Proven Track Record: Successful deployment in challenging offshore environments demonstrates real-world performance capabilities.
For offshore pipeline projects where reliability, longevity, and performance are non-negotiable requirements, WUZHOU’s SSAW pipes represent the optimal balance of technical excellence and cost-effectiveness.
4. Material Selection and Quality Standards for Offshore SSAW Pipe Applications
When engineering offshore pipeline systems, material selection becomes one of the most critical factors determining project success, operational lifespan, and total cost of ownership. For SSAW pipes used in marine environments, the relationship between material specifications and performance outcomes is particularly significant.
Steel Grade Selection for Offshore Applications
The foundation of any high-performance SSAW pipe begins with the appropriate steel grade selection. For offshore applications, this decision must balance multiple factors:
API 5L Steel Grades Commonly Used in Offshore SSAW Pipes
Steel Grade | Yield Strength (MPa) | Tensile Strength (MPa) | Typical Applications |
---|---|---|---|
X42 | 290 | 414 | Standard offshore gathering lines |
X52 | 359 | 455 | Medium-pressure transport lines |
X60 | 414 | 517 | Main transmission lines |
X65 | 448 | 531 | High-pressure transmission |
X70 | 483 | 565 | Deepwater trunk lines |
X80 | 552 | 621 | Ultra-high pressure applications |
WUZHOU specializes in manufacturing SSAW pipes across this full spectrum of steel grades, with particular expertise in X65 and X70 grades that are increasingly specified for challenging offshore projects. Their metallurgical expertise ensures consistent mechanical properties throughout large production runs, giving wholesale buyers confidence in material performance.
Chemical Composition Considerations
Beyond the basic strength classifications, the specific chemical composition of the steel used in SSAW pipes significantly impacts their suitability for offshore environments:
- Carbon Content: Lower carbon content improves weldability and low-temperature toughness
- Manganese Ratio: Impacts strength and resistance to hydrogen-induced cracking
- Micro-alloying Elements: Small additions of niobium, vanadium, and titanium enhance grain structure
- Sulfur and Phosphorus Control: Minimizing these elements improves toughness and corrosion resistance
- Carbon Equivalent: Influences weldability and susceptibility to hydrogen cracking
WUZHOU maintains strict control over the chemical composition of all raw materials, requiring comprehensive material certifications and conducting independent verification testing to ensure optimal performance in demanding offshore environments.
Critical Quality Standards for Offshore SSAW Pipes
Offshore pipeline applications require adherence to stringent international standards and specifications. WUZHOU’s manufacturing processes are aligned with the most demanding industry requirements:
Key International Standards for Offshore SSAW Pipes
Standard/Specification | Focus Area | WUZHOU Compliance |
---|---|---|
API 5L | General pipeline steel specifications | Full certification across all grades |
ISO 3183 | Petroleum and natural gas industries specifications | Complete compliance with all categories |
DNV-OS-F101 | Submarine pipeline systems | Meets all applicable requirements |
NACE MR0175/ISO 15156 | Materials for H₂S-containing environments | Compliant for sour service applications |
ASTM A1018 | Standard for steel sheet and strip | Fully compliant for raw materials |
AWS D1.1 | Structural welding code | Welding procedures and qualification |
Qualification and Testing Requirements
Ensuring SSAW pipe quality for offshore applications requires extensive testing throughout the manufacturing process:
- Pre-Production Material Testing:
- Chemical composition analysis
- Mechanical property verification
- Grain structure examination
- Inclusion assessment
- In-Process Quality Control:
- Automated weld parameter monitoring
- Real-time dimensional verification
- Continuous visual inspection
- Weld quality monitoring
- Post-Production Testing:
- Hydrostatic pressure testing (100% of production)
- Ultrasonic testing of weld seams
- X-ray inspection of critical sections
- Mechanical property confirmation
- Specialized Offshore Qualification Testing:
- Fracture toughness assessment
- Collapse resistance verification
- Fatigue performance evaluation
- Corrosion resistance testing
WUZHOU’s comprehensive quality assurance program includes all these testing protocols, with detailed documentation provided to wholesale buyers and project engineers to verify compliance with project specifications.
Enhancing Performance Through Material Innovation
Beyond standard material specifications, WUZHOU continues to innovate in material technology to enhance the performance of SSAW pipes in offshore environments:
Advanced Material Technologies for Offshore Applications
- High-Strength Low-Alloy (HSLA) Steel Optimization:
- Custom alloying formulations for specific offshore environments
- Balanced composition for strength, toughness, and weldability
- Controlled rolling processes to optimize grain structure
- Hydrogen-Induced Cracking (HIC) Resistant Grades:
- Modified chemistry to prevent sulfide stress cracking
- Controlled inclusion morphology to inhibit crack initiation
- Specialized heat treatment for resistance to hydrogen embrittlement
- Low-Temperature Toughness Enhancement:
- Refined grain structure for improved Charpy impact values
- Controlled cooling rates during production
- Nickel-enhanced grades for arctic and deep-sea applications
- Corrosion-Resistant Alloy Cladding:
- Internal cladding with corrosion-resistant alloys for aggressive media
- Metallurgically bonded layers providing superior performance
- Long-term protection against internal corrosion mechanisms
As offshore projects push into more challenging environments, these material innovations provide project developers with expanded options to meet specific operational requirements while maintaining the cost advantages of SSAW pipe technology.
5. Cost-Efficiency Analysis: SSAW Pipes vs. Alternative Pipeline Solutions
For procurement specialists and project managers, the total economic picture of pipeline selection extends far beyond initial purchase price. A comprehensive analysis reveals why SSAW pipes frequently emerge as the most cost-effective solution for offshore applications when all factors are considered.
Comparative Capital Expenditure Analysis
When evaluating initial procurement costs, SSAW pipes offer significant advantages:
Manufacturing Cost Comparison by Pipe Type
Pipe Type | Relative Manufacturing Cost | Production Efficiency | Material Utilization |
---|---|---|---|
SSAW | Baseline (100%) | High – continuous process | Excellent – minimal waste |
LSAW | 120-135% | Medium – plate forming required | Good – some edge waste |
Seamless | 150-200% | Low – intensive process | Poor – substantial material loss |
Mechanically lined | 200-250% | Very low – complex process | Poor – requires dual materials |
These manufacturing cost advantages translate directly to procurement savings, particularly for large-diameter pipes where SSAW technology demonstrates the greatest efficiency advantage. For wholesale buyers purchasing substantial volumes for major offshore projects, these savings can represent millions of dollars in reduced capital expenditure.
Cost Drivers in Offshore Pipeline Selection
Several factors influence the total acquisition cost of offshore pipeline systems:
- Raw Material Requirements:
- SSAW pipes typically require 5-8% less steel than LSAW alternatives
- Material savings increase proportionally with pipe diameter
- Strategic material purchasing at WUZHOU optimizes raw material costs
- Production Efficiency:
- SSAW manufacturing is a continuous, highly automated process
- Higher production rates reduce labor costs per meter
- WUZHOU’s 11 production lines enable optimized production scheduling
- Quality Control Economics:
- Integrated testing in SSAW production reduces rework
- Lower defect rates minimize costly material rejections
- WUZHOU’s comprehensive quality management system ensures first-time quality
- Logistics and Transportation:
- Optimized wall thickness reduces shipping weight
- Consistent quality reduces need for excess inventory
- WUZHOU’s strategic location facilitates efficient global shipping
Total Cost of Ownership Assessment
Beyond initial acquisition costs, SSAW pipes demonstrate compelling advantages in total lifecycle economics:
Installation Cost Factors
Installation represents a significant portion of total project costs for offshore pipelines:
Installation Factor | SSAW Advantage | Economic Impact |
---|---|---|
Welding requirements | Consistent weld preparation | 5-10% faster field welding |
Weight handling | Optimized strength-to-weight ratio | Reduced heavy lifting requirements |
Field cut adjustments | Dimensional stability | Minimized rework in the field |
Coating compatibility | Factory-applied coatings | Reduced field coating requirements |
WUZHOU’s precisely manufactured SSAW pipes, with their consistent dimensions and high-quality factory coatings, significantly reduce field installation challenges. This translates directly to faster installation schedules and lower project costs.
Operational Economics Over Time
The long-term economic benefits of SSAW pipes become increasingly apparent throughout the operational life of offshore pipeline systems:
- Maintenance Requirements:
- Lower incidence of weld failures reduces inspection frequency
- Superior coating adhesion minimizes corrosion-related maintenance
- Structural integrity reduces need for pressure derating over time
- Operational Efficiency:
- Smooth internal surfaces reduce pumping power requirements
- Consistent internal diameter optimizes flow characteristics
- Dimensional stability maintains design performance long-term
- Lifetime Extension Potential:
- Higher initial safety factors allow for potential service life extension
- Better corrosion allowance utilization extends useful life
- Resistance to fatigue mechanisms preserves structural integrity
An economic analysis over a typical 30-year service life shows that SSAW pipes from quality manufacturers like WUZHOU typically result in 15-20% lower total lifecycle costs compared to alternative solutions, when all factors are considered.
Risk Mitigation Value
In offshore applications, the economic consequences of pipeline failures are exceptionally high. The reliability of SSAW pipes provides significant risk mitigation value:
Comparative Risk Assessment
Risk Factor | SSAW Performance | Economic Value |
---|---|---|
Catastrophic failure | Very low probability with quality SSAW | Avoidance of massive remediation costs |
Leak detection | High-integrity welds enable earlier detection | Minimized product loss and environmental impact |
Repair frequency | Lower requirement for in-service repairs | Reduced expensive underwater repair operations |
Service interruption | Higher reliability reduces downtime | Maintained production value |
The exceptional quality control systems employed by WUZHOU, including 100% hydrostatic testing and comprehensive non-destructive examination, provide wholesale buyers and project developers with confidence that their offshore pipelines will perform reliably throughout their design life.
Project Case Study: Economic Analysis
A comparative economic analysis from a recent major offshore pipeline project demonstrates the comprehensive cost advantages of SSAW pipes:
Cost Category | SSAW Solution | LSAW Alternative | Seamless Alternative |
---|---|---|---|
Material acquisition | $22.5M | $28.7M | $38.2M |
Transportation | $3.2M | $3.9M | $4.1M |
Installation | $18.7M | $20.3M | $19.5M |
Lifecycle maintenance | $7.3M | $9.1M | $6.8M |
Risk-adjusted costs | $4.2M | $5.8M | $3.9M |
Total lifecycle cost | $55.9M | $67.8M | $72.5M |
Relative cost | 100% | 121% | 130% |
This analysis demonstrates why procurement specialists and project developers increasingly specify WUZHOU SSAW pipes for offshore applications, recognizing their overall economic advantages while maintaining the performance requirements essential for challenging marine environments.
6. WUZHOU’s Advanced SSAW Pipe Production Capabilities for Offshore Projects
As the offshore industry demands increasingly sophisticated pipeline solutions, manufacturing capabilities become a critical differentiator in supplier selection. WUZHOU has established itself as an industry leader through continuous investment in production technology, quality systems, and specialized capabilities for offshore applications.
Manufacturing Infrastructure Overview
WUZHOU’s impressive production infrastructure provides the foundation for exceptional quality and capacity in SSAW pipe manufacturing:
Production Facilities and Capacity
Facility Assets | Specifications | Offshore Production Capability |
---|---|---|
3 subsidiaries | Specialized in different aspects of production | Comprehensive supply chain integration |
2 factories | Strategic locations with shipping access | Efficient global distribution |
4 production bases | Specialized manufacturing facilities | Dedicated offshore pipe production |
6 production workshops | Controlled manufacturing environments | Specialized coating and testing capabilities |
11 spiral pipe production lines | Advanced automation and control | Multiple diameter capability (219mm-3500mm) |
2 coating/lining production lines | Specialized offshore coatings | Complete external/internal protection systems |
With an annual production capacity of 400,000 tons of spiral welded pipes, WUZHOU maintains the scale necessary to support major offshore projects while ensuring consistent quality through specialized production facilities.
Technical Production Capabilities for Offshore Requirements
WUZHOU’s manufacturing processes are specifically optimized for the demanding requirements of offshore applications:
1. Advanced Forming Technology
The foundation of WUZHOU’s SSAW manufacturing excellence begins with sophisticated forming systems:
- CNC-Controlled Forming: Computer-controlled forming operations ensure precise spiral geometry
- Multi-Roll Forming Technology: Progressive forming reduces residual stress in the pipe body
- Dimensional Control Systems: Laser measurement ensures exact diameter and roundness
- Edge Preparation Technology: Precision milling creates optimal weld joint configuration
These forming capabilities ensure that WUZHOU’s SSAW pipes maintain the dimensional precision and roundness critical for offshore applications where external pressure resistance is essential.
2. Welding Excellence
WUZHOU’s welding technology represents the state of the art in SSAW pipe manufacturing:
- Submerged Arc Welding Parameters: Computerized control of all welding parameters:
- Current and voltage optimization
- Travel speed precision
- Flux composition and application
- Heat input control
- Multi-Wire Technology: Simultaneous multiple wire welding for:
- Increased deposition rates
- Improved productivity
- Enhanced metallurgical properties
- Reduced heat-affected zone
- Weld Monitoring Systems: Real-time monitoring ensures weld quality:
- Continuous parameter verification
- Automated defect detection
- Digital quality documentation
- Complete traceability
- Post-Weld Heat Treatment: Specialized stress relief processes:
- Controlled heating and cooling cycles
- Residual stress reduction
- Hydrogen removal
- Mechanical property optimization
3. Specialized Offshore Coating Systems
WUZHOU’s dedicated coating facilities provide comprehensive protection systems specifically designed for marine environments:
- External Coating Options:
- 3-Layer Polyethylene (3LPE): Superior mechanical protection and moisture barrier
- Fusion-Bonded Epoxy (FBE): Excellent chemical resistance for aggressive environments
- Polypropylene Coatings: Enhanced temperature resistance for heated product lines
- Concrete Weight Coating: Provides negative buoyancy and mechanical protection
- Internal Lining Systems:
- Liquid Epoxy Linings: Chemical resistance for corrosive products
- Cement Mortar Lining: Abrasion resistance and flow efficiency
- Dual-Layer Systems: Combined chemical and mechanical protection
- Field Joint Coating Preparation: Factory preparation of pipe ends for field joint completion:
- Cutback specifications optimized for field conditions
- Surface preparation for maximum coating adhesion
- Compatible systems for continuous protection
4. Comprehensive Testing Infrastructure
WUZHOU’s commitment to quality is demonstrated through extensive testing capabilities specifically calibrated for offshore applications:
- Hydrostatic Testing: Every pipe undergoes pressure testing exceeding operational requirements
- Ultrasonic Testing: Automated UT systems detect and characterize weld imperfections
- X-Ray Inspection: Radiographic examination verifies weld integrity
- Mechanical Testing Laboratory: Comprehensive verification of material properties:
- Tensile testing
- Charpy impact testing
- Hardness testing
- Bend testing
- Flattening tests
Quality Management Systems for Offshore Applications
WUZHOU’s quality management systems are specifically designed to meet the stringent requirements of offshore projects:
1. International Certification and Compliance
WUZHOU maintains the highest level of international certification relevant to offshore pipeline applications:
- API 5L Certification: Meeting American Petroleum Institute standards for petroleum pipeline systems
- ISO 9001 Certification: Comprehensive quality management system implementation
- ISO 14001 Certification: Environmental management systems for sustainable manufacturing
- EU Standard Compliance: Meeting European requirements for pressure equipment
These certifications provide wholesale buyers and project developers with confidence that WUZHOU’s SSAW pipes meet all international standards applicable to offshore applications.
2. Material Traceability and Documentation
Complete documentation and traceability are essential for offshore projects subject to rigorous regulatory oversight:
- Material Test Certificates: Comprehensive documentation of chemical composition and mechanical properties
- Production Records: Complete manufacturing history for each pipe:
- Heat numbers and material source
- Production date and line identification
- Process parameters and controls
- Operator qualifications
- Inspection Reports: Detailed results of all testing:
- Hydrostatic test results with pressure curves
- NDE reports with acceptance criteria
- Dimensional inspection records
- Coating inspection results
- Digital Quality Documentation: Electronic records for efficient project integration:
- Searchable database of all quality records
- Digital certification accessible to project teams
- Comprehensive material traceability
- Integration with project documentation systems
3. Continuous Improvement Programs
WUZHOU maintains a dedicated focus on continuous improvement in manufacturing processes:
- Production Data Analysis: Statistical process control to identify optimization opportunities
- Customer Feedback Integration: Project experience incorporated into manufacturing refinements
- Technology Investment: Ongoing capital investment in advanced manufacturing systems
- R&D Collaboration: Partnerships with research institutions to develop new capabilities
These improvement initiatives ensure that WUZHOU’s manufacturing capabilities continue to advance alongside the evolving requirements of offshore pipeline projects.
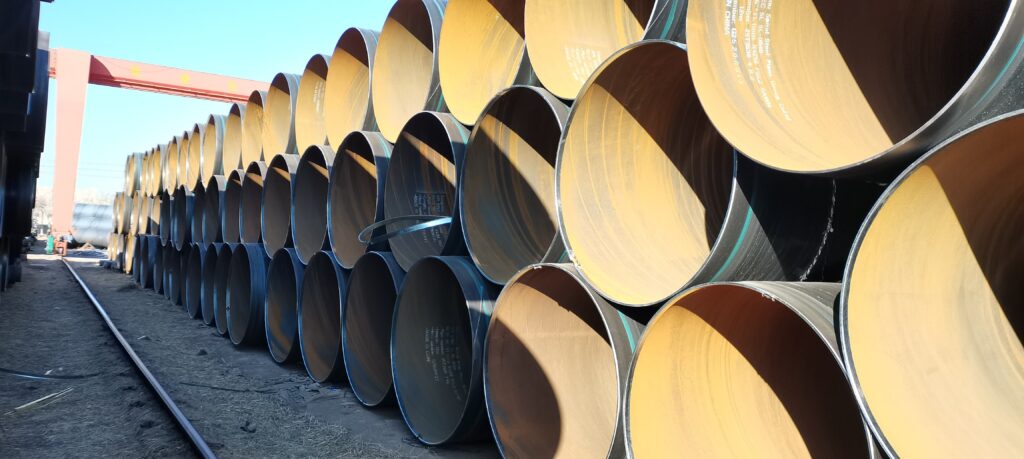
WUZHOU’s Production Advantages for Wholesale Buyers
For wholesale buyers and project developers, WUZHOU’s manufacturing capabilities translate into tangible business advantages:
- Production Scale and Flexibility:
- Capacity to fulfill large-volume orders for major projects
- Multiple production lines allow schedule optimization
- Ability to produce varying specifications within single orders
- Quality Consistency:
- Standardized manufacturing processes ensure consistent quality
- Comprehensive testing verifies compliance with specifications
- Documented quality systems minimize acceptance issues
- Delivery Reliability:
- Production capacity ensures on-time delivery
- Efficient scheduling minimizes lead times
- Logistics coordination optimizes project timelines
- Technical Support:
- Manufacturing expertise supports specification development
- Technical consultation throughout the procurement process
- Field support during installation and commissioning
For offshore projects where supply chain reliability is critical to overall project success, WUZHOU’s comprehensive manufacturing capabilities provide the confidence needed by procurement specialists and project managers to specify SSAW pipes as their preferred solution.
7. Case Studies: Successful Offshore Pipeline Projects Using SSAW Pipes
The ultimate validation of any pipeline solution comes through successful implementation in challenging real-world environments. The following case studies highlight how SSAW pipes from WUZHOU have delivered exceptional performance in diverse offshore applications, providing valuable insights for project developers and procurement specialists considering similar projects.
Case Study 1: North Sea Gas Transmission System
Project Overview
Project Parameter | Specification |
---|---|
Location | North Sea continental shelf |
Water Depth | 85-120 meters |
Pipeline Length | 142 kilometers |
Pipe Diameter | 36 inches (914mm) |
Wall Thickness | 20.6mm |
Steel Grade | X65 |
Design Pressure | 150 bar |
Product | Natural gas |
Installation Method | S-lay |
Project Challenges
This major gas transmission project faced several significant challenges:
- Harsh Environmental Conditions:
- Severe North Sea winter weather
- Strong currents and wave action
- Abrasive seabed conditions in certain sections
- Strict Regulatory Requirements:
- Rigorous European safety standards
- Environmental impact minimization mandates
- Regular inspection and integrity verification requirements
- Technical Specifications:
- High-pressure gas transmission
- Temperature fluctuations from ambient seawater
- Potential for internal condensation corrosion
WUZHOU SSAW Pipe Solution
WUZHOU provided a comprehensive pipeline solution featuring:
- Custom X65 SSAW Pipes: Manufactured to precise project specifications with enhanced toughness properties
- 3LPE External Coating: Three-layer polyethylene coating with additional mechanical protection
- Internal Epoxy Coating: Specialized coating to prevent internal corrosion
- Concrete Weight Coating: Applied to provide stability and mechanical protection
- Comprehensive Documentation: Full material traceability and testing certification
Results and Performance
The pipeline has been in successful operation for over five years with:
- Zero Reportable Incidents: No leaks, failures, or environmental incidents
- 100% Uptime Performance: No service interruptions due to pipeline issues
- Excellent Corrosion Control: Inspection reports show minimal corrosion activity
- On-Schedule Installation: Installation completed ahead of projected timeline
- Long-Term Integrity: Pressure testing confirms maintained structural integrity
Key Learnings
This project demonstrated several important advantages of WUZHOU’s SSAW pipes:
- The spiral weld configuration provided exceptional resistance to the bending stresses encountered during installation.
- The consistent dimensional accuracy facilitated efficient field welding, reducing installation time.
- The integrated quality assurance program ensured problem-free commissioning and operation.
- The cost savings compared to alternative pipe types enabled additional investment in advanced coating systems.
Case Study 2: Southeast Asian Offshore Oil Production System
Project Overview
Project Parameter | Specification |
---|---|
Location | South China Sea |
Water Depth | 45-75 meters |
Pipeline Length | 78 kilometers |
Pipe Diameter | 24 inches (610mm) |
Wall Thickness | 16.8mm |
Steel Grade | X60 |
Design Pressure | 120 bar |
Product | Crude oil |
Installation Method | S-lay with bottom tow sections |
Project Challenges
This offshore oil production system presented unique challenges:
- Environmental Factors:
- Typhoon-prone region with extreme weather events
- Varied seabed topography requiring route flexibility
- Warm water accelerating potential corrosion processes
- Operational Requirements:
- Intermittent flow patterns creating pressure cycling
- Crude oil with potentially corrosive properties
- High operating temperature differential
- Logistical Challenges:
- Remote location with limited infrastructure
- Tight project timeline requiring just-in-time delivery
- Multiple installation vessels requiring coordinated supply
WUZHOU SSAW Pipe Solution
WUZHOU engineered a comprehensive solution including:
- Modified X60 SSAW Pipes: Custom chemistry for enhanced corrosion resistance
- High-Performance FBE Coating: Specifically formulated for elevated temperature service
- Specialized Field Joint System: Designed for rapid installation in offshore conditions
- Enhanced End Preparation: Optimized for automated welding systems
- Expedited Production Schedule: Dedicated production line allocation to meet timeline
Results and Performance
After three years of operation, the pipeline system has demonstrated:
- Excellent Flow Efficiency: Better than predicted pressure drop characteristics
- Superior Corrosion Resistance: Inspection reveals minimal internal or external corrosion
- Structural Integrity: No evidence of fatigue or stress-related issues despite multiple typhoon events
- Schedule Adherence: Project completed on schedule with no material-related delays
- Cost Performance: Total installed cost approximately 12% below initial budget
Key Learnings
This project highlighted several specific advantages of WUZHOU’s SSAW pipes:
- The production flexibility allowed custom material properties tailored to the specific operating environment.
- The efficient manufacturing process enabled meeting an aggressive delivery schedule that would have been challenging with alternative pipe types.
- The robust spiral weld design provided exceptional resistance to the pressure cycling inherent in the operation.
- The comprehensive quality documentation facilitated regulatory approval and commissioning.
Case Study 3: Offshore Wind Farm Intake/Outflow System
Project Overview
Project Parameter | Specification |
---|---|
Location | Baltic Sea |
Water Depth | 20-35 meters |
Pipeline Length | 28 kilometers (multiple lines) |
Pipe Diameter | 72 inches (1829mm) |
Wall Thickness | 17.5mm |
Steel Grade | X52 |
Design Pressure | 10 bar |
Function | Cooling water intake/outflow |
Installation Method | Bottom tow with concrete mattress protection |
Project Challenges
This renewable energy infrastructure project faced distinct challenges:
- Large Diameter Requirements:
- Exceptional diameter-to-thickness ratio
- Significant fabrication challenges
- Complex handling and installation logistics
- Environmental Regulations:
- Strict ecological impact limitations
- Thermal discharge monitoring requirements
- Marine life protection mandates
- Operational Specifications:
- Continuous seawater exposure
- Biological growth management
- Long-term maintenance minimization
WUZHOU SSAW Pipe Solution
WUZHOU developed a specialized solution featuring:
- Large-Diameter X52 SSAW Pipes: Among the largest diameter pipes manufactured
- Marine-Grade Coating System: Specifically formulated for continuous seawater immersion
- Internal Cement Lining: Providing flow efficiency and biological growth resistance
- Custom End Connections: Designed for specialized underwater joining system
- Streamlined Production Process: Modified to accommodate exceptional diameter
Results and Performance
With the wind farm now operational for over two years:
- Optimized Flow Performance: System provides the required cooling capacity with minimal pumping energy
- Excellent Structural Integrity: No deformation or buckling despite challenging diameter-to-thickness ratio
- Minimal Maintenance Requirements: Inspection reports indicate excellent coating performance
- Environmental Compliance: System meets all regulatory requirements for marine impact
- Cost Effectiveness: Total solution delivered approximately 22% cost savings compared to alternative materials
Key Learnings
This challenging application demonstrated important capabilities of WUZHOU’s SSAW pipe technology:
- The spiral manufacturing process enabled production of exceptionally large diameter pipes that would be impractical with other fabrication methods.
- The dimensional stability of the large-diameter pipes facilitated precise installation in environmentally sensitive conditions.
- The cost-effectiveness of the SSAW solution allowed allocation of budget to enhanced environmental protection measures.
- The technical support provided by WUZHOU throughout the design and installation process contributed significantly to project success.
Analysis: Common Success Factors
Across these diverse case studies, several common factors emerge that highlight why WUZHOU’s SSAW pipes consistently deliver exceptional performance in offshore applications:
- Manufacturing Quality:
- Consistent dimensional accuracy facilitates installation
- Comprehensive testing eliminates in-service failures
- Material traceability supports quality assurance
- Technical Adaptability:
- Customized solutions for specific project requirements
- Material properties tailored to operating environments
- Production flexibility accommodating project timelines
- Economic Advantages:
- Cost-efficiency enabling additional protective measures
- Schedule reliability reducing project timeline risks
- Long-term performance minimizing maintenance costs
- Comprehensive Support:
- Technical consultation during specification development
- Documentation support for regulatory compliance
- Field support during installation and commissioning
For wholesale buyers and project developers considering offshore pipeline solutions, these case studies provide compelling evidence of the advantages offered by WUZHOU’s SSAW pipes across diverse applications and operating environments.
8. Installation and Maintenance Best Practices for Offshore SSAW Pipelines
The exceptional performance of SSAW pipes in offshore applications depends not only on manufacturing quality but also on proper installation and maintenance practices. This section provides essential guidance for project engineers and operations managers to maximize the value of their SSAW pipeline investments.
Pre-Installation Planning and Preparation
Successful offshore pipeline installation begins with thorough planning and preparation:
Material Handling and Storage Guidelines
Handling Phase | Best Practices for SSAW Pipes | Rationale |
---|---|---|
Transport | Use proper pipe supports and securing | Prevents deformation and coating damage |
Offloading | Utilize appropriate lifting equipment with padding | Preserves coating integrity |
Storage | Store on level ground with proper supports | Prevents ovalization and coating damage |
Stacking | Limit stack height; use appropriate separators | Maintains pipe roundness and coating condition |
Inspection | Perform receiving inspection upon arrival | Identifies any transportation damage |
WUZHOU provides comprehensive handling guidelines with each shipment, ensuring that pipes maintain their manufactured quality throughout the logistics chain.
Pre-Installation Inspection and Testing
Before offshore deployment, a thorough inspection regime should include:
- Visual Inspection:
- Coating condition assessment
- End preparation verification
- Dimensional confirmation
- Identification and traceability verification
- Supplementary Testing:
- Holiday testing of coatings
- Coating adhesion verification
- End straightness measurement
- Ovality verification at pipe ends
- Documentation Review:
- Verification of material test certificates
- Confirmation of dimensional reports
- Review of coating inspection reports
- Validation of traceability documentation
WUZHOU’s comprehensive quality documentation package facilitates this pre-installation verification process, providing all necessary information in a structured format.
Offshore Installation Techniques for SSAW Pipes
Different installation methods require specific considerations to leverage the advantages of SSAW pipes:
1. S-Lay Installation Method
The S-lay method is commonly used for offshore pipeline installation, where the pipe forms an S-shape from the lay vessel to the seabed:
- Stinger Design Considerations:
- Minimum bend radius calculations based on SSAW pipe properties
- Stinger configuration optimization for specific pipe dimensions
- Tension control parameters based on pipe strength characteristics
- Field Joint Efficiency:
- Welding procedure qualification specific to SSAW pipe properties
- Field joint coating system compatibility with factory-applied coatings
- Quality control procedures tailored to field conditions
- Tension Control Parameters:
- Maximum allowable tension based on SSAW pipe structural properties
- Adjustment protocols for varying water depths and pipe characteristics
- Continuous monitoring systems to prevent over-tensioning
2. J-Lay Installation Considerations
For deeper water applications, the J-lay method offers advantages but requires specific attention to:
- Top Tension Management:
- Maximum allowable tension calculations for SSAW pipe specifications
- Monitoring systems to maintain tension within design parameters
- Emergency procedures for tension excursion events
- Verticality Control:
- Pipe string alignment monitoring to prevent excessive bending
- Adjustment procedures based on SSAW pipe flexibility characteristics
- Weather condition limitations specific to pipe properties
- Seabed Touchdown Monitoring:
- ROV surveillance of pipe touchdown conditions
- Pipe deformation monitoring during installation
- Seabed preparation requirements based on pipe flexibility
3. Reel-Lay Considerations for Smaller Diameter SSAW Pipes
For smaller diameter applications where reel-lay is feasible:
- Reeling Strain Limitations:
- Maximum allowable strain calculations specific to SSAW pipe properties
- Reel diameter optimization based on pipe characteristics
- Post-reeling inspection requirements
- Straightening Process:
- Straightener configuration for SSAW pipe dimensions
- Residual curvature monitoring and acceptance criteria
- Post-straightening inspection protocols
- Coating Integrity Verification:
- Post-reeling coating inspection techniques
- Repair procedures for any coating damage
- Additional coating protection measures if required
4. Towing Installation Methods
For certain applications, bottom or controlled depth towing offers advantages:
- Pipe String Assembly:
- Assembly site requirements for SSAW pipe handling
- Field welding considerations for long strings
- Buoyancy module attachment guidelines
- Tow Configuration:
- Tow string design based on SSAW pipe properties
- Tension monitoring and control systems
- Weather and sea state limitations
- Touchdown and Positioning:
- Seabed preparation requirements
- Positioning accuracy protocols
- Post-installation survey requirements
Long-Term Maintenance and Integrity Management
The operational phase of offshore SSAW pipelines requires a structured approach to maintenance and integrity management:
Inspection and Monitoring Programs
A comprehensive inspection regime should include:
Inspection Type | Frequency | Focus Areas for SSAW Pipes |
---|---|---|
External visual inspection | 1-3 years | Coating condition, free span, marine growth |
Cathodic protection survey | 1-2 years | System effectiveness, anode consumption |
Internal inspection (pigging) | 3-5 years | Internal corrosion, geometry, metal loss |
Pressure testing | As required | System integrity verification |
Geotechnical survey | 2-5 years | Seabed movement, pipeline support |
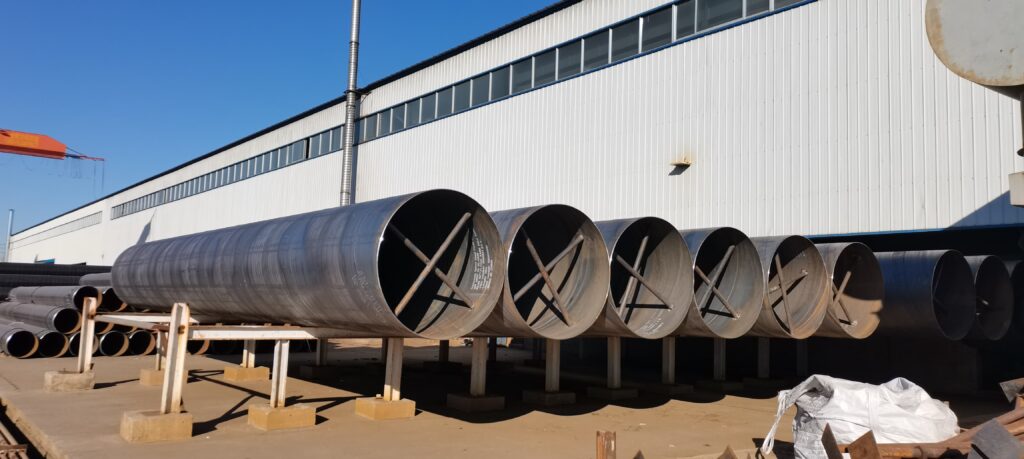
Corrosion Management Strategies
SSAW pipes in offshore environments benefit from multi-layered corrosion protection:
- External Corrosion Control:
- Coating system maintenance and repair protocols
- Cathodic protection system monitoring and maintenance
- Marine growth management to prevent under-deposit corrosion
- Internal Corrosion Management:
- Product chemistry monitoring and control
- Corrosion inhibitor injection programs
- Cleaning pig frequency optimization
- Corrosion monitoring systems deployment
- Specific Attention Areas for SSAW Pipes:
- Weld seam inspection focus during in-line inspection
- Field joint coating performance monitoring
- Bend locations where strain may be concentrated
Integrity Assessment and Remaining Life Evaluation
Regular integrity assessments help optimize pipeline operations and maintenance:
- Risk-Based Inspection Planning:
- Identification of high-consequence areas
- Probability and consequence assessment
- Inspection resource optimization
- Fitness-for-Service Assessment:
- Analysis of inspection data against critical limits
- Remaining life calculations based on degradation rates
- Operating pressure reassessment if required
- Rehabilitation and Repair Strategies:
- Coating repair methods and qualification
- Structural repair options for different damage mechanisms
- Assessment of repair effectiveness and durability
WUZHOU’s Technical Support for Lifecycle Management
WUZHOU provides ongoing technical support throughout the operational life of their SSAW pipe systems:
- Technical Consultation:
- Advice on inspection findings interpretation
- Guidance on repair method selection
- Input on life extension assessments
- Material Data Support:
- Original manufacturing data for comparison with inspection results
- Material property information for integrity assessments
- Weld seam characteristics for specialized inspections
- Continuous Improvement Feedback:
- Collection of in-service performance data
- Analysis of potential design or manufacturing enhancements
- Updates on latest maintenance technologies and practices
By following these installation and maintenance best practices, operators can maximize the performance and service life of offshore SSAW pipelines, realizing the full economic and technical benefits of this pipeline solution.
9. FAQs: Common Questions About SSAW Pipes for Offshore Applications
This comprehensive FAQ section addresses the most common questions procurement specialists, project engineers, and operations managers have about SSAW pipes for offshore applications.
Manufacturing and Production Questions
Q: What is the maximum diameter available for SSAW pipes suitable for offshore applications?
A: WUZHOU manufactures SSAW pipes with diameters ranging from 219mm to 3500mm (approximately 8.6 inches to 138 inches) that meet offshore application requirements. The specific maximum diameter for a particular project depends on water depth, pressure requirements, and installation method. For most deep-water offshore applications, SSAW pipes up to 60 inches (1500mm) are commonly used, while larger diameters are frequently specified for shallow water applications like water intake systems and outfalls.
Q: How does the spiral welding process affect the pipe’s pressure resistance compared to longitudinal welded pipes?
A: The spiral welding configuration actually provides enhanced pressure resistance compared to longitudinal welded pipes of equivalent wall thickness. This is due to several factors:
- The spiral weld distributes hoop stress along a greater length of weld, reducing stress concentration.
- The helical weld path creates a more uniform stress distribution throughout the pipe body.
- The manufacturing process allows for more precise control of dimensional properties.
WUZHOU’s SSAW pipes typically demonstrate 5-15% higher pressure resistance than longitudinal welded pipes of equivalent dimensions and material grade. This can allow for optimization of wall thickness in some applications, providing cost savings without compromising safety.
Q: What quality control measures ensure SSAW pipes will perform reliably in offshore environments?
A: WUZHOU implements a comprehensive quality control system specifically designed for offshore-grade SSAW pipes:
- Raw Material Verification: 100% of steel coil undergoes chemical and mechanical property verification
- In-Process Monitoring: Continuous automated monitoring of all welding parameters
- Hydrostatic Testing: Every pipe is pressure tested to 1.5 times design pressure minimum
- Non-Destructive Examination: 100% of weld seams undergo ultrasonic testing
- X-Ray Inspection: Random and targeted radiographic examination of welds
- Dimensional Verification: Comprehensive measurement of all critical dimensions
- Coating Inspection: Multiple test methods verify coating integrity
- Mechanical Testing: Regular sampling for destructive testing of production material
- Traceability: Complete documentation from raw material to finished product
This multi-layered quality system ensures that only pipes meeting all specification requirements are shipped to offshore projects.
Technical Performance Questions
Q: How do SSAW pipes perform under the cyclic loading conditions typical in offshore environments?
A: SSAW pipes demonstrate excellent fatigue resistance under cyclic loading conditions when properly manufactured. The spiral weld configuration actually provides advantages in fatigue performance because:
- The helical weld path distributes stress more uniformly than a longitudinal weld.
- The weld reinforcement profile can be carefully controlled to minimize stress concentration.
- Modern welding processes used by WUZHOU create extremely consistent weld profiles with minimal defects that could serve as fatigue initiation sites.
For applications with significant cyclic loading, WUZHOU can provide enhanced fatigue-resistant SSAW pipes by:
- Utilizing specific steel grades with superior toughness properties
- Implementing post-weld heat treatment to optimize residual stress patterns
- Applying additional NDT to verify absence of fatigue-sensitive defects
- Providing additional engineering support for fatigue-critical designs
Q: What coating systems are recommended for SSAW pipes in offshore applications?
A: The optimal coating system depends on specific project requirements, but WUZHOU recommends and applies several proven systems for offshore applications:
Coating System | Best Applications | Features |
---|---|---|
3-Layer Polyethylene (3LPE) | General purpose offshore | Excellent corrosion and mechanical protection |
Fusion-Bonded Epoxy (FBE) | High-temperature service | Superior chemical resistance and temperature stability |
Dual Layer FBE | Aggressive environments | Enhanced protection with redundant barrier |
Polypropylene | Deepwater applications | Excellent pressure and temperature resistance |
Concrete Weight Coating | Stability requirements | Provides negative buoyancy and mechanical protection |
For internal protection, options include:
- Liquid epoxy coatings for corrosive products
- Cement mortar lining for abrasion resistance
- Specialized chemical-resistant linings for aggressive media
WUZHOU’s two dedicated coating facilities can apply these systems to exact project specifications with comprehensive quality control and documentation.
Q: How do SSAW pipes compare to seamless pipes for deep-water applications?
A: Both SSAW and seamless pipes can be successfully used in deep-water applications when properly designed and manufactured. The comparison involves several factors:
Performance Factor | SSAW Pipes | Seamless Pipes |
---|---|---|
Collapse resistance | Very good with proper D/t ratio | Excellent |
Available diameters | Wide range (219-3500mm) | Limited (typically max 20-24″) |
Wall thickness consistency | Excellent | May vary within tolerance |
Material grade options | Extensive | May be limited for large diameters |
Production lead time | Typically shorter | Often longer for specialty grades |
Cost efficiency | More economical | Premium cost |
For deep-water applications requiring diameters larger than 24 inches, SSAW pipes are often the only practical option. WUZHOU provides specialized engineering support to ensure SSAW pipes meet all deep-water design requirements, including enhanced collapse resistance through optimized D/t ratios and material selection.
Procurement and Specification Questions
Q: What international standards should be specified when ordering SSAW pipes for offshore applications?
A: For offshore applications, WUZHOU recommends specifying the following standards:
- Primary Pipe Standard: API 5L / ISO 3183 with appropriate grade (typically X52 through X70)
- Supplementary Requirements:
- PSL2 quality level as minimum
- Additional NDT requirements (100% UT of weld seam)
- Enhanced dimensional tolerances
- Specific mechanical property requirements (Charpy impact testing)
- Offshore-Specific Standards:
- DNV-OS-F101 for submarine pipeline systems
- API RP 1111 for design of offshore pipelines
- Coating Standards:
- ISO 21809 series for external coatings
- API RP 5L2 or ISO 15741 for internal coatings when required
WUZHOU’s quality management system is fully aligned with these international standards, and all production is certified accordingly.
Q: What documentation should be requested with SSAW pipes for offshore projects?
A: WUZHOU provides comprehensive documentation for offshore SSAW pipe orders, including:
Standard Documentation Package:
- Material Test Certificates (EN 10204 3.1 or 3.2 as required)
- Dimensional inspection reports
- Hydrostatic test certificates
- NDT reports (UT, X-ray)
- Coating inspection reports
- Certificate of Compliance to ordered specification
- Traceability documentation
Optional Enhanced Documentation:
- Production process parameters summary
- Welding procedure qualification records
- Welder qualification documentation
- Raw material source certification
- Additional mechanical test reports (CTOD, HIC, etc.)
- Third-party inspection reports
Comprehensive documentation is essential for regulatory compliance and quality assurance in offshore projects, and WUZHOU’s documentation systems are designed to meet the most stringent requirements.
Q: What is the typical lead time for SSAW pipes for offshore projects?
A: Lead times vary based on project volume, specifications, and current production scheduling, but typical timeframes for WUZHOU’s SSAW pipes are:
Production Phase | Typical Duration |
---|---|
Engineering and specification review | 1-2 weeks |
Raw material procurement | 4-8 weeks |
Production scheduling | 1-2 weeks |
Manufacturing | 6-12 weeks depending on volume |
Coating application | 3-4 weeks |
Testing and inspection | 1-2 weeks |
Documentation and preparation for shipment | 1 week |
Total typical lead time | 16-28 weeks |
For urgent projects, WUZHOU can implement expedited schedules through priority production allocation and optimized process flow. Early engagement during the project planning phase allows for optimal integration with project timelines.
Installation and Operation Questions
Q: What are the key considerations for field welding of SSAW pipes in offshore installation?
A: Field welding of WUZHOU’s SSAW pipes requires attention to several important factors:
- Welding Procedure Qualification:
- Procedures should be qualified specifically for the SSAW pipe material
- Test welds should include the spiral seam intersection when applicable
- All offshore installation positions should be included in qualification
- Pipe End Preparation:
- WUZHOU provides precise end preparation to customer specifications
- Bevels are machined to tight tolerances to facilitate alignment
- Special attention to spiral weld location at pipe ends
- Field Quality Control:
- 100% NDT inspection of field welds is recommended
- Special attention to any intersection with the spiral seam
- Visual inspection criteria for alignment and profile
WUZHOU provides technical support for development of field welding procedures, including recommended parameters based on the specific pipe material properties.
Q: How should in-line inspection be adapted for SSAW pipes in offshore pipelines?
A: In-line inspection of SSAW pipes should consider the following:
- Tool Selection:
- Ultrasonic tools are generally preferred for detailed weld inspection
- MFL tools should have sufficient resolution to detect anomalies in the spiral weld
- Combination tools may provide optimal defect characterization
- Inspection Planning:
- Baseline inspection within first 1-3 years of operation is recommended
- Spiral weld location mapping improves analysis accuracy
- Consider lower reporting thresholds for initial inspections
- Data Analysis:
- Analysts should be familiar with SSAW pipe characteristics
- Differentiation between manufacturing features and in-service anomalies
- Correlation with manufacturing NDT results when available
- Reinspection Intervals:
- Risk-based approach considering initial findings
- Typical intervals of 3-7 years depending on service conditions
- Consider more frequent inspection of any identified areas of interest
WUZHOU can provide technical information to support development of effective in-line inspection programs for their SSAW pipes.
Q: What is the expected service life of SSAW pipes in offshore applications?
A: When properly specified, installed, and maintained, WUZHOU’s SSAW pipes for offshore applications typically have a design life of 25-30 years minimum. Actual service life can extend significantly beyond this timeframe with appropriate integrity management.
Factors affecting service life include:
- External Environment:
- Effectiveness of corrosion protection systems
- Seabed stability and movement
- Marine growth and microbiological activity
- Internal Environment:
- Product corrosivity and flow characteristics
- Effectiveness of internal corrosion management
- Operational temperature and pressure cycles
- Design Margins:
- Initial corrosion allowance specification
- Safety factors in pressure rating
- Fatigue life calculations
- Maintenance Practices:
- Effectiveness of inspection programs
- Timely intervention for identified issues
- Cathodic protection system maintenance
WUZHOU’s SSAW pipes have demonstrated excellent long-term performance in offshore applications, with many installations exceeding their initial design life while maintaining full operational capability.
Economic and Business Questions
Q: What total cost of ownership advantages do SSAW pipes offer for offshore projects?
A: SSAW pipes provide several significant total cost of ownership advantages:
- Initial Capital Cost Savings:
- 10-25% lower material cost compared to seamless alternatives
- 5-15% cost advantage over LSAW pipes for equivalent specifications
- Material optimization through consistent wall thickness
- Installation Cost Benefits:
- Consistent dimensions reduce field fit-up challenges
- Excellent roundness minimizes alignment issues
- Precise end preparation improves welding efficiency
- Operational Economics:
- Reliable performance reduces maintenance requirements
- Excellent coating compatibility enhances corrosion protection
- Consistent internal diameter optimizes flow efficiency
- Life-Cycle Cost Advantage:
- Reduced inspection frequency due to manufacturing quality
- Lower repair and intervention requirements
- Potential for life extension beyond initial design parameters
A comprehensive economic analysis typically demonstrates that WUZHOU’s SSAW pipes offer 15-20% lower total lifecycle costs compared to alternative pipe types for most offshore applications.
Q: What financing and payment terms are available for large offshore SSAW pipe orders?
A: WUZHOU offers flexible financial arrangements for major offshore projects:
- Standard Payment Terms:
- Typical structure: 30% deposit, 40% before shipment, 30% upon delivery
- Letter of Credit accepted for international transactions
- Payment terms can be aligned with project milestones
- Project Financing Support:
- Assistance with export credit agency involvement
- Cooperation with project finance structures
- Extended payment terms for qualified major projects
- Volume Discounting:
- Tiered pricing structure for large-volume orders
- Long-term supply agreement discounts
- Framework agreements for multi-phase projects
WUZHOU’s financial team works directly with project developers to create customized financial arrangements that align with project cash flow requirements while managing risk appropriately.
Q: How does WUZHOU ensure reliable supply for multi-year offshore development projects?
A: WUZHOU has implemented several strategies to ensure supply reliability for major projects:
- Production Capacity Management:
- 400,000-ton annual production capacity across 11 production lines
- Strategic scheduling of maintenance to maintain capacity
- Ability to dedicate production lines to critical projects
- Raw Material Security:
- Strategic relationships with multiple steel suppliers
- Material reservation programs for long-term projects
- Inventory management for critical steel grades
- Project-Specific Planning:
- Detailed production scheduling aligned with project timelines
- Regular progress reporting and schedule updates
- Contingency planning for potential disruptions
- Quality Resources Allocation:
- Dedicated quality personnel assigned to major projects
- Capacity for resident inspection when required
- Documentation systems scaled to project requirements
For multi-phase offshore projects, WUZHOU can establish framework agreements that guarantee capacity, pricing structure, and quality resources throughout the project lifecycle, providing development teams with supply chain certainty for these critical components.
WUZHOU is committed to providing the highest quality SSAW pipes for offshore applications, supported by comprehensive technical expertise and customer service. Our state-of-the-art production facilities, rigorous quality control systems, and proven track record in challenging offshore environments make us the preferred supplier for project developers worldwide.
For detailed information about how WUZHOU’s SSAW pipes can meet your specific offshore project requirements, contact our technical sales team today to arrange a consultation with our engineering specialists.