DIN 30671 Fused Epoxy Coated Spiral Weld Pipe: The Complete Guide for 2025
February 19, 2025
Share This Article
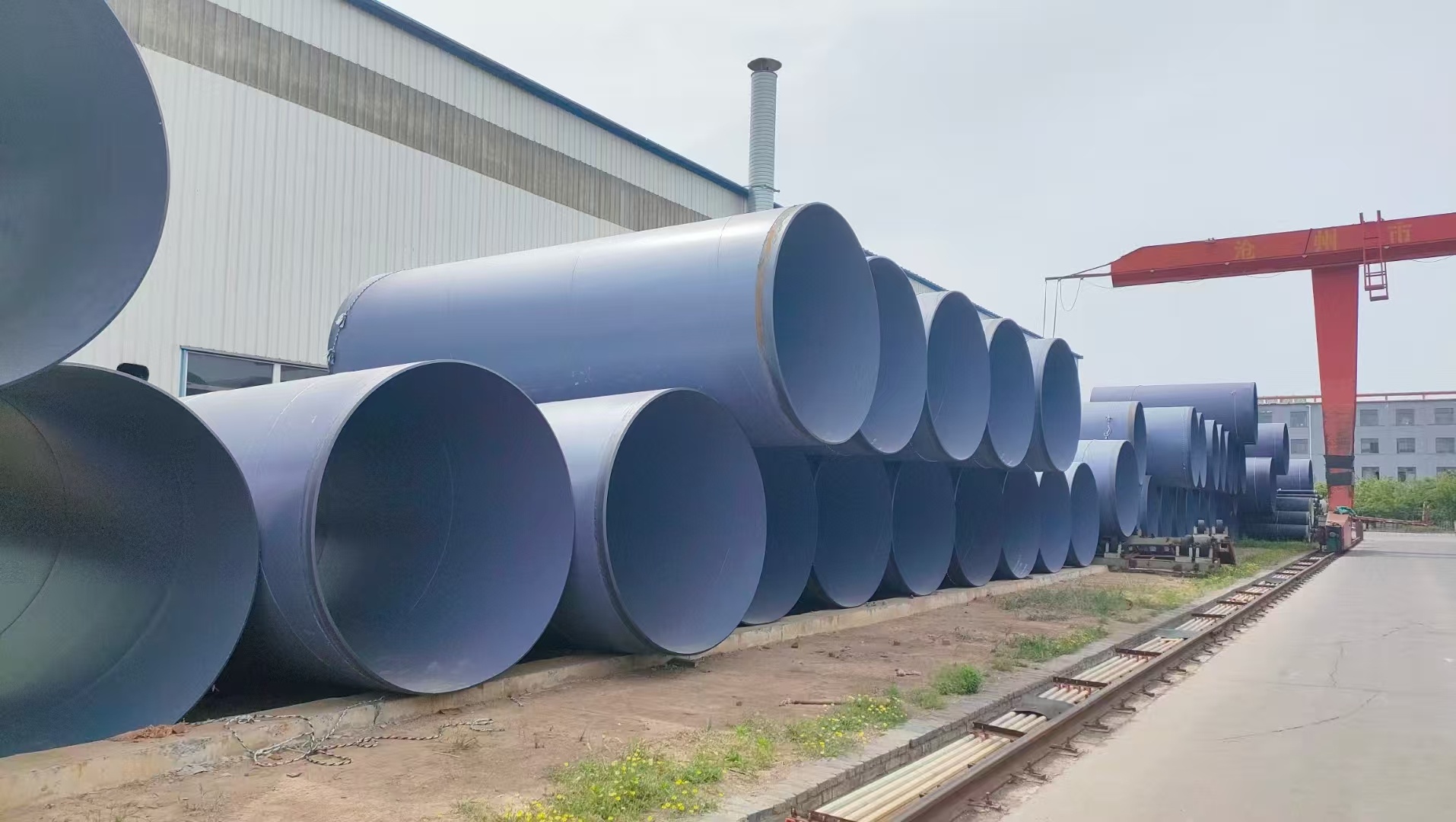
Overview of DIN 30671 Fused Epoxy Coated Spiral Weld Pipe
The DIN 30671 Fused Epoxy Coated Spiral Weld Pipe is a premium-quality steel pipe used in oil & gas pipelines, water transmission, industrial piping, and buried pipeline applications. The fusion bonded epoxy (FBE) coating ensures exceptional corrosion resistance, high adhesion, and durability, making it ideal for underground and marine environments.
Key Features of DIN 30671 Fused Epoxy Coated Spiral Weld Pipe
✔ Spiral Submerged Arc Welded (SSAW) steel pipe
✔ DIN 30671-compliant fusion bonded epoxy (FBE) coating
✔ Excellent resistance to corrosion, impact, and chemical exposure
✔ Available in diameters ranging from 6 inches to 144 inches (150mm to 3658mm)
✔ Complies with DIN 30671, API 5L, ASTM A252, and GB/T9711 standards
✔ Ideal for underground pipelines, offshore oil & gas, and industrial applications
This guide will cover manufacturing processes, applications, price trends, suppliers, and quality standards for DIN 30671 FBE Coated Spiral Weld Pipes.
Top DIN 30671 Fused Epoxy Coated Spiral Weld Pipe Manufacturers in 2025
Choosing a reliable manufacturer ensures high-quality materials, precise coating applications, and compliance with DIN standards. Here are some of the leading manufacturers of DIN 30671 FBE Coated Spiral Weld Pipes:
1. Cangzhou Spiral Steel Pipes Group Co., Ltd
✔ 27 years of experience in steel pipe manufacturing
✔ 13 production lines for Φ219–Φ3500mm spiral welded pipes
✔ Annual production capacity: 400,000 tons
✔ ISO 9001, API 5L, ASTM-certified DIN 30671 FBE Coated Spiral Weld Pipes
✔ Custom epoxy coatings for water, oil & gas, and industrial pipelines
2. EUROPIPE (Germany)
A leading European manufacturer of large-diameter spiral welded pipes, specializing in DIN 30671 coatings for oil & gas transmission.
3. Jindal SAW Ltd (India)
Provides high-performance spiral pipes with DIN 30671 FBE coatings for water transmission, oil & gas, and industrial applications.
4. Nippon Steel (Japan)
A global leader in high-strength, corrosion-resistant spiral welded pipes for marine, offshore, and industrial applications.
5. Tenaris (Italy)
Manufactures premium-quality spiral welded pipes with DIN 30671 FBE coatings for onshore and offshore pipeline projects.
Each of these manufacturers ensures strict compliance with DIN 30671 standards, guaranteeing high durability and corrosion resistance.
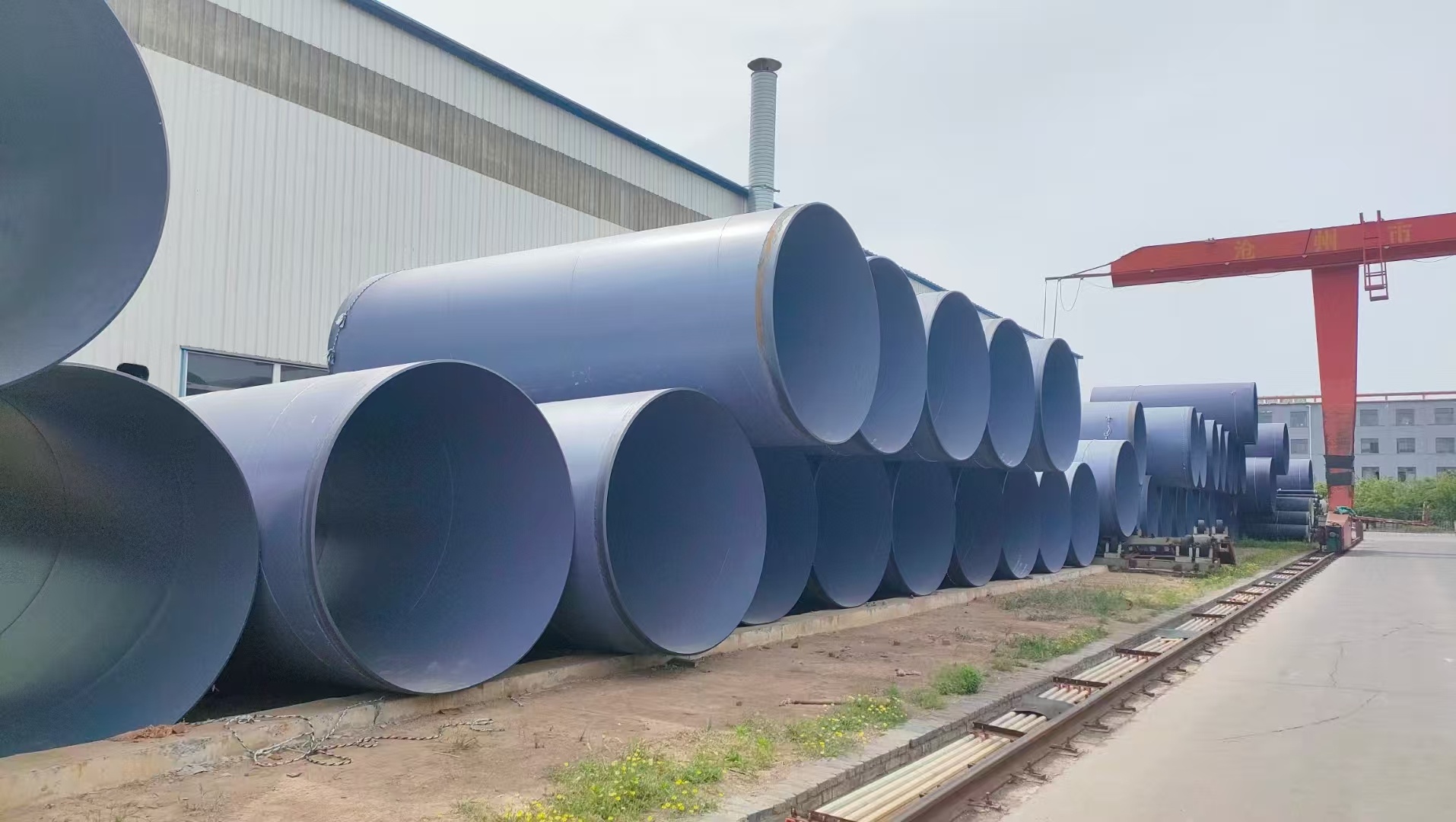
DIN 30671 Fused Epoxy Coated Spiral Weld Pipe vs Other Coated Pipes
Selecting the right coating type depends on application, cost, and durability. Below is a comparison between DIN 30671 FBE Coated Spiral Weld Pipe and other coated pipes:
Feature | DIN 30671 FBE Coated Pipe | DIN 30670 PE Coated Pipe | AWWA C214 3LPE Coated Pipe |
---|---|---|---|
Coating Type | Fusion Bonded Epoxy (FBE) | Polyethylene (PE) | Three-layer Polyethylene (3LPE) |
Corrosion Resistance | Very High | High | Very High |
Mechanical Protection | Moderate | High | Very High |
Best Use Case | Underground pipelines, water transmission | Underground pipelines, oil & gas transmission | High-pressure and offshore applications |
Lifespan | 30-50 years | 50+ years | 50+ years |
Temperature Resistance | Up to 110°C | Up to 85°C | Up to 85°C |
Cost | Moderate | Slightly higher | Higher |
Why Choose DIN 30671 FBE Coated Spiral Weld Pipe?
✔ Superior adhesion and corrosion resistance
✔ Ideal for underground and offshore applications
✔ Cost-effective compared to multi-layer coatings
DIN 30671 Spiral Weld Pipe Price Per Ton in 2025
The price of DIN 30671 FBE Coated Spiral Weld Pipes varies based on factors such as pipe diameter, wall thickness, steel grade, and coating thickness. Below is an estimated pricing chart for 2025:
Wall Thickness (mm) | Steel Grade | Price Per Ton (USD) |
---|---|---|
6 – 10 mm | API 5L X42 – X65 | 4,800−4,800 – 4,800−6,800 |
12 – 18 mm | API 5L X65 – X70 | 5,900−5,900 – 5,900−7,900 |
20 – 40 mm | API 5L X70 – X80 | 7,200−7,200 – 7,200−10,200 |
Factors Affecting Price:
✔ Pipe Diameter & Wall Thickness – Larger and thicker pipes require more material.
✔ Coating Type – FBE coating thickness impacts cost.
✔ Bulk Orders – Large quantity orders receive better pricing.
Cangzhou Spiral Steel Pipes Group offers high-quality DIN 30671 FBE Coated Spiral Weld Pipes at competitive prices.
DIN 30671 Fused Epoxy Coated Spiral Weld Pipe Manufacturing Process & Quality Control
How Are DIN 30671 Fused Epoxy Coated Spiral Weld Pipes Manufactured?
The manufacturing process of DIN 30671 FBE Coated Spiral Weld Pipes follows strict DIN, API 5L, ASTM A252, and GB/T9711 standards to ensure high durability, corrosion resistance, and mechanical protection. Below is a step-by-step breakdown of the production process:
1. Raw Material Selection
- High-quality steel coils (API 5L, ASTM A252, GB/T9711) are carefully selected to meet chemical and mechanical composition requirements.
- The steel undergoes chemical and mechanical testing to verify yield strength, tensile strength, and impact resistance.
2. Pipe Forming & Spiral Welding
- The steel plates are rolled into a spiral shape using advanced forming machines.
- The edges are submerged arc welded (SAW) using double-sided automatic welding to ensure defect-free, high-strength weld seams.
- This welding process ensures full penetration and structural stability, making it ideal for water transmission, oil & gas, and industrial applications.
3. Hydrostatic Pressure Testing
- Each pipe undergoes high-pressure hydrostatic testing to verify leak-proof and structural reliability.
4. Ultrasonic & Radiographic Testing
- Non-destructive testing (NDT) is performed to detect internal or external defects in the weld seam.
- Ultrasonic, X-ray, and magnetic particle testing are conducted based on pipe grade and project requirements.
5. Surface Preparation
- The pipe surface is thoroughly cleaned by sandblasting or shot blasting to remove rust, scale, and contaminants.
- Proper surface preparation ensures better adhesion of the FBE coating.
6. Fusion Bonded Epoxy (FBE) Coating Application (DIN 30671)
- Preheating: The pipe is preheated to the required temperature to ensure proper adhesion of the epoxy powder.
- Electrostatic Spray Application: A uniform layer of fusion bonded epoxy (FBE) powder is applied using an electrostatic spray process.
- Fusion & Curing: The epoxy powder melts and fuses onto the pipe surface, creating a seamless, corrosion-resistant barrier.
- Thickness Control: The coating thickness is measured to meet DIN 30671 specifications.
7. Beveling & Cutting
- Pipes are cut into required lengths using automated machinery.
- The pipe ends are beveled for easy welding and connection.
8. Final Inspection & Packaging
- Pipes are marked, inspected, and bundled according to customer requirements.
- Each pipe is labeled with batch numbers, specifications, and manufacturer details for full traceability.
Why DIN 30671 FBE Coated Spiral Weld Pipes Are Preferred?
✔ Designed for high-pressure water and oil & gas pipeline systems
✔ Manufactured with advanced welding and coating processes
✔ High resistance to corrosion, abrasion, and environmental stress
✔ Long-lasting performance in buried and marine environments
Cangzhou Spiral Steel Pipes Group Co., Ltd follows strict quality control procedures to ensure high-performance DIN 30671 FBE Coated Spiral Weld Pipes.
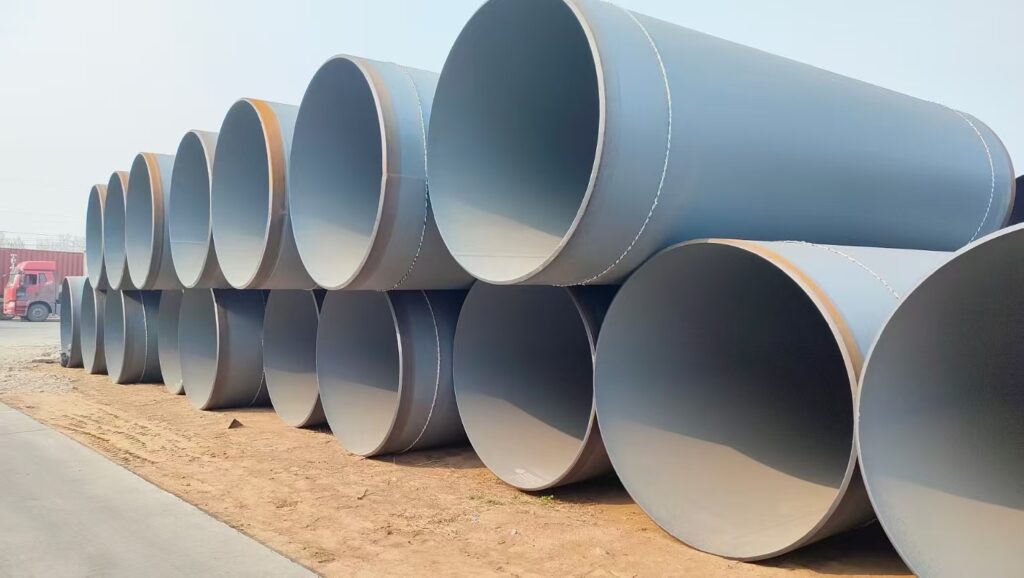
DIN 30671 FBE Coated Spiral Weld Pipe Applications & Industry Uses
Where Are DIN 30671 FBE Coated Spiral Weld Pipes Used?
DIN 30671 FBE Coated Spiral Weld Pipes are widely used in municipal water infrastructure, oil & gas pipelines, industrial projects, and marine environments.
Industry | Application | Why DIN 30671 Spiral Weld Pipe? |
---|---|---|
Water Transmission | Municipal water supply, potable water pipelines | Leak-proof, corrosion-resistant, and long service life |
Wastewater Systems | Sewage treatment plants, drainage pipelines | High-strength, durable, and resistant to chemical exposure |
Industrial Pipelines | Power plants, chemical processing, and desalination plants | Handles high pressures and corrosive environments |
Oil & Gas | Crude oil, natural gas transmission pipelines | Superior chemical resistance and long lifespan |
Marine & Offshore | Coastal water transmission systems, offshore desalination plants | Resistant to seawater and extreme marine conditions |
Why DIN 30671 Spiral Weld Pipes Are Ideal for Underground & Marine Applications?
✔ High resistance to chemical corrosion and environmental exposure
✔ Available in large diameters for municipal and industrial projects
✔ Cost-effective solution for long-distance transmission pipelines
Cangzhou Spiral Steel Pipes Group supplies customized DIN 30671 FBE Coated Spiral Weld Pipes for municipal water supply, oil & gas pipelines, industrial applications, and marine projects.
DIN 30671 Spiral Weld Pipe Coating & Anti-Corrosion Treatment
To ensure long-lasting performance, DIN 30671 Spiral Weld Pipes can be coated with various anti-corrosion treatments.
Coating Type | Corrosion Resistance | Best Applications |
---|---|---|
Fusion Bonded Epoxy (FBE) Coating (DIN 30671) | Very High | Underground pipelines, water transmission |
3LPE Coating (AWWA C214) | Very High | Underground pipelines, oil & gas transmission |
3LPP Coating (AWWA C214) | Very High | High-temperature applications, offshore pipelines |
Polyethylene (PE) Coating (DIN 30670) | High | Municipal water supply, structural applications |
Why FBE Coating is Essential for DIN 30671 Spiral Weld Pipes?
✔ Prevents corrosion in buried and marine environments
✔ Reduces maintenance costs and extends service life
✔ Enhances resistance against chemicals, soil, and extreme temperatures
Cangzhou Spiral Steel Pipes Group provides custom coating services to meet industry-specific requirements.
Final Thoughts
For high-quality DIN 30671 FBE Coated Spiral Weld Pipes, Cangzhou Spiral Steel Pipes Group Co., Ltd is your best choice in 2025!
Need a quote or more technical details? Contact Cangzhou Spiral Steel Pipes Group today!