Common Mistakes to Avoid When Purchasing Spiral Welded Pipes
April 1, 2025
Share This Article
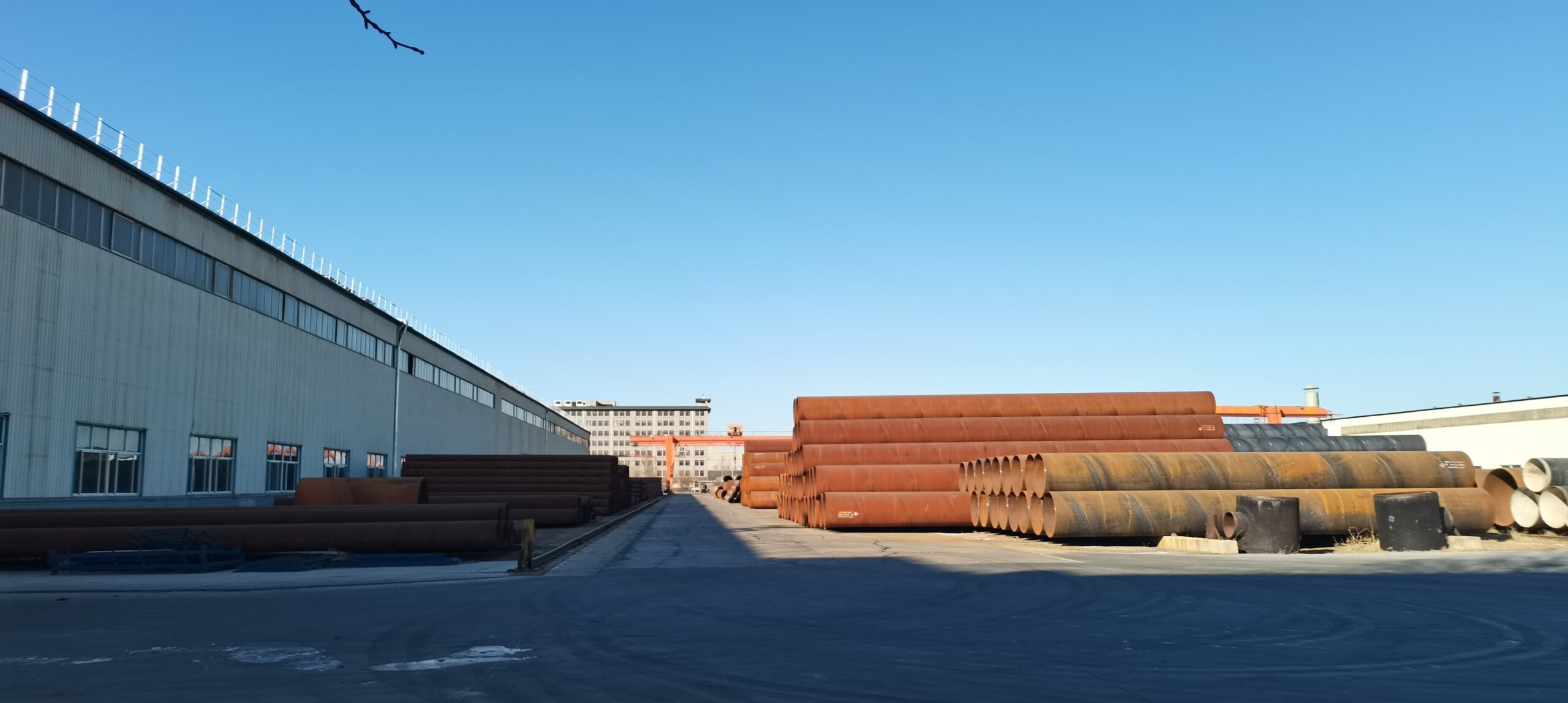
1. Introduction: The Critical Role of Spiral Welded Pipes in Industrial Applications
In today’s industrial landscape, spiral welded steel pipes form the backbone of critical infrastructure systems worldwide. From transporting oil and natural gas across vast distances to conveying water for municipal supply networks and supporting power generation facilities, these pipes literally keep our modern world functioning. However, the procurement process for these essential components is fraught with potential pitfalls that can lead to costly errors, project delays, and even catastrophic failures.
For wholesale buyers, distributors, and procurement professionals in industries such as oil and gas, water transmission, and power generation, understanding the complexities of spiral welded pipe purchasing is not just advantageous—it’s essential. The consequences of making procurement mistakes can be severe, including:
- Premature pipe failure resulting in operational downtime
- Environmental hazards due to leaks or ruptures
- Significant financial losses from replacement and remediation
- Project delays affecting multiple stakeholders
- Regulatory non-compliance and potential legal liabilities
- Damage to corporate reputation and loss of client trust
According to recent industry reports, approximately 30% of pipeline project delays stem from issues related to pipe quality and specification mismatches. Even more concerning, an estimated 15-20% of pipeline failures can be traced back to poor material selection or quality control issues during procurement.
Table 1: Impact of Procurement Mistakes in Spiral Welded Pipe Projects
Consequence | Financial Impact | Project Timeline Impact | Long-term Business Impact |
---|---|---|---|
Pipe Failure | $500,000-$5 million per incident | 2-6 months delay | Loss of contracts, reputation damage |
Specification Mismatch | $100,000-$1 million in rework | 1-3 months delay | Strained client relationships |
Quality Control Issues | $250,000-$2 million in testing and replacement | 2-4 months delay | Increased insurance premiums |
Supply Chain Disruption | $50,000-$500,000 in expediting fees | 1-2 months delay | Supplier relationship damage |
Industry leaders recognize that successful pipeline projects begin with informed procurement practices. As the CEO of a major pipeline construction firm recently noted, “The difference between a successful project and a problematic one often comes down to the quality of materials and the reliability of suppliers selected during the procurement phase.”
This comprehensive guide aims to illuminate the most common pitfalls in spiral welded pipe procurement and provide actionable strategies to avoid them. By understanding these challenges and implementing best practices, procurement specialists can ensure they select high-quality pipes that meet project specifications while maintaining budget constraints and timeline requirements.
2. Understanding Spiral Welded Pipe Specifications and Standards
One of the most critical aspects of spiral welded pipe procurement is having a thorough understanding of relevant specifications and standards. Many purchasing errors stem from a lack of clarity around these technical requirements, leading to mismatches between what’s ordered and what a project actually needs.
2.1 Key Technical Specifications for Spiral Welded Pipes
Before initiating any procurement process, buyers must be intimately familiar with several essential technical parameters:
Pipe Diameter and Wall Thickness:
Spiral welded pipes are available in a wide range of diameters, typically from 16 inches (406mm) to 120 inches (3048mm), with various wall thicknesses. Selecting the incorrect dimensions can lead to flow rate issues, pressure handling problems, and potential system failures.
Steel Grade Requirements:
The steel grade determines the pipe’s mechanical properties and its suitability for specific applications. Common grades for spiral welded pipes include:
- API 5L Grades (B, X42, X46, X52, X56, X60, X65, X70, X80)
- ASTM A252 Grades (1, 2, 3)
- EN 10219 Grades (S235, S275, S355)
Table 2: Common Steel Grades and Their Applications
Steel Grade | Yield Strength (min) | Applications | Special Considerations |
---|---|---|---|
API 5L X42 | 42,000 psi (290 MPa) | General pipeline applications | Good balance of strength and weldability |
API 5L X52 | 52,000 psi (359 MPa) | Oil and gas transmission | Improved pressure rating |
API 5L X65 | 65,000 psi (448 MPa) | High-pressure transmission | Enhanced strength-to-weight ratio |
API 5L X70 | 70,000 psi (483 MPa) | Arctic and offshore applications | Low-temperature toughness |
ASTM A252 Grade 3 | 45,000 psi (310 MPa) | Piling and foundation applications | High structural integrity |
EN 10219 S355 | 50,800 psi (355 MPa) | Structural applications | European standard compliance |
Welding Process and Quality:
Spiral welded pipes are typically manufactured using one of two processes:
- Single-sided submerged arc welding (SSAW)
- Double-sided submerged arc welding (DSAW)
Understanding the differences between these processes and their implications for pipe performance is crucial for procurement specialists. Double-sided welding, as utilized by industry leaders like WUZHOU, generally provides superior weld strength and reliability for demanding applications.
Coating and Lining Requirements:
Depending on the application environment, pipes may require specific protective coatings:
- External coatings: FBE (Fusion Bonded Epoxy), 3PE/3PP (Three-layer polyethylene/polypropylene), coal tar epoxy
- Internal linings: Epoxy, cement mortar, polyurethane
Failure to correctly specify coating requirements can lead to accelerated corrosion and significantly reduced service life.
2.2 Critical Industry Standards and Certifications
Procurement professionals must be familiar with relevant international standards governing spiral welded pipe manufacturing and testing:
- API 5L: American Petroleum Institute standard for line pipe
- ASTM A252: Standard specification for welded steel pipe piles
- AWWA C200: American Water Works Association standard for steel water pipe
- EN 10219: European standard for cold-formed welded structural hollow sections
- ISO 3183: International standard for petroleum and natural gas industries
- CSA Z245.1: Canadian standard for steel pipe
Each standard contains specific requirements for chemical composition, mechanical properties, dimensions, tolerances, and testing procedures. Procurement specifications should clearly reference the applicable standards and any additional project-specific requirements.
“Compliance with international standards isn’t just a checkbox exercise—it’s fundamental to ensuring pipe performance and longevity,” explains the Quality Control Director at WUZHOU, a leading manufacturer recognized as a “Top 10 Chinese Brand of Steel Pipe.” “At WUZHOU, our double-sided submerged arc welded spiral steel pipes have passed the API 5L standard of the American Petroleum Institute and EU standards, ensuring our products meet the highest quality benchmarks globally.”
2.3 Common Specification Mistakes and How to Avoid Them
Underspecifying Technical Requirements:
Many procurement issues arise from vague or incomplete technical specifications. Ensure all critical parameters are explicitly stated, including:
- Dimensional requirements (diameter, wall thickness, length)
- Material grade and chemical composition
- Mechanical property requirements (yield strength, tensile strength, elongation)
- Welding requirements and acceptance criteria
- Inspection and testing requirements
- Surface condition and end preparation
- Coating specifications
Overlooking End-Use Conditions:
Pipes intended for different environmental conditions require specific properties:
- Sour Service: Pipelines transporting H₂S-containing fluids require special material properties and testing
- Low-Temperature Service: Arctic or offshore applications may need enhanced low-temperature toughness
- High-Pressure Applications: Require specific weld quality and mechanical property verification
- Seismic Zones: May need enhanced flexibility and joint design
Ignoring Logistics Constraints:
Consider transportation limitations when specifying pipe dimensions and packaging requirements. Standard pipe lengths typically range from 6 to 12 meters, but transportation might limit practical lengths in some regions.
Best Practice Recommendation:
Create a comprehensive technical data sheet (TDS) that clearly defines all pipe requirements. Have this reviewed by both engineering and procurement teams before issuing purchase requisitions. Include explicit acceptance criteria for all properties and tests to avoid ambiguity.
3. Top 10 Common Mistakes in Spiral Welded Pipe Procurement
Throughout years of industry experience, certain procurement errors appear consistently across different sectors. By recognizing these patterns, buyers can implement preventative measures to avoid costly mistakes.
Mistake #1: Prioritizing Price Above All Other Factors
Perhaps the most common procurement error is making decisions primarily based on price without adequately considering quality, service, and long-term value. While initial cost savings may seem attractive, they often lead to greater expenses down the line.
Real-World Impact:
A municipal water authority selected the lowest bidder for a major transmission line project, saving approximately 12% on initial pipeline costs. However, within three years, premature corrosion issues required partial pipeline replacement, resulting in costs exceeding 300% of the initial “savings.”
Solution Approach:
- Implement Total Cost of Ownership (TCO) analysis for major pipe procurements
- Consider life-cycle costs including installation, maintenance, and replacement
- Evaluate warranty terms and historical performance data
- Assess supplier reliability and post-purchase support capabilities
As one WUZHOU customer, a project manager for a major oil pipeline, noted: “The initial price differential was quickly offset by the superior quality and reduced installation issues. WUZHOU pipes required significantly less field rework and have performed flawlessly since installation five years ago.”
Mistake #2: Inadequate Supplier Qualification and Evaluation
Many procurement specialists fail to thoroughly investigate potential suppliers’ capabilities, quality management systems, and track records before placing orders.
Best Practice Approach:
- Request and verify relevant certifications (ISO 9001, API 5L, etc.)
- Conduct supplier facility audits when possible
- Review supplier manufacturing capacity and capabilities
- Check references from previous customers on similar projects
- Evaluate supplier financial stability
WUZHOU exemplifies the importance of supplier capabilities with its comprehensive manufacturing infrastructure: “With 13 advanced production lines—11 for spiral steel pipes and 2 for coating and lining—we ensure high-capacity output, strict quality control, and compliance with international standards,” explains the company’s Operations Director.
Mistake #3: Insufficient Quality Control Requirements
Many procurement documents lack detailed quality assurance and quality control requirements, leading to inconsistent product quality and acceptance disputes.
Key Quality Control Elements to Specify:
- Required non-destructive testing methods and acceptance criteria
- Material traceability requirements
- Witness and hold points during manufacturing
- Documentation requirements (MTRs, test reports, etc.)
- Third-party inspection requirements and inspector qualifications
WUZHOU’s approach to quality control demonstrates industry best practices: “Every spiral steel pipe produced by our factory undergoes rigorous quality inspection including water pressure testing, ultrasonic testing, and X-ray testing. From raw material selection to production completion, we ensure the quality of each spiral welded pipe, providing comprehensive material reports and quality inspection documentation.”
Mistake #4: Ignoring Industry-Specific Requirements
Different industries have unique requirements for spiral welded pipes, and failure to account for these can lead to significant problems:
Oil and Gas Sector Requirements:
- Sour service testing for H₂S environments
- Specific fracture toughness properties
- Special end treatments for welding
- Enhanced corrosion protection
Water Transmission Requirements:
- NSF/ANSI 61 compliance for potable water
- Specific lining requirements for water quality protection
- Cathodic protection compatibility
- Joint design for seismic conditions
Power Generation Requirements:
- High-temperature performance specifications
- Specific dimensional tolerances
- Enhanced weld quality requirements
- Special inspection criteria
Mistake #5: Poor Timing and Supply Chain Planning
Late procurement initiation and inadequate lead time allowances frequently cause project delays and rush charges.
Strategic Approaches:
- Begin procurement activities early in the project planning process
- Develop realistic lead time expectations based on current market conditions
- Consider split orders with staggered delivery schedules
- Implement supplier capacity reservation agreements for critical projects
Table 3: Typical Lead Times for Spiral Welded Pipe Procurement
Phase | Typical Duration | Factors Affecting Timeline | Risk Mitigation Strategies |
---|---|---|---|
Supplier Selection | 1-2 months | Market conditions, specification complexity | Early engagement with pre-qualified suppliers |
Manufacturing | 2-4 months | Order size, pipe complexity, factory capacity | Capacity reservation agreements |
Testing & Inspection | 2-3 weeks | Test requirements, third-party availability | Pre-arrange inspection services |
Transportation | 1-3 months | Destination, shipping method, customs | Logistics planning with contingencies |
Total Timeline | 4-10 months | Project scale, market conditions | Phased delivery scheduling |
Mistake #6: Incomplete Documentation Requirements
Failing to specify all required documentation leads to difficulties in material traceability, quality verification, and project handover.
Essential Documentation Package:
- Material Test Reports (MTRs) for raw materials
- Production process records
- Dimensional inspection reports
- Non-destructive testing reports (UT, RT, etc.)
- Hydrostatic test records
- Coating inspection reports
- Certificate of Compliance
- Packing lists and shipping documentation
As WUZHOU highlights in their quality assurance process: “We provide raw material reports and quality inspection reports for every spiral welded steel pipe. Documentation ensures traceability throughout the pipe lifecycle and facilitates project certification.”
Mistake #7: Inadequate Communication of Project-Specific Requirements
Many procurement issues stem from failure to communicate unique project requirements to manufacturers.
Critical Communication Points:
- Special testing requirements beyond standard specifications
- Unique identification marking requirements
- Project-specific quality control procedures
- Special packaging or handling needs
- Site-specific delivery constraints
- End-use environmental conditions
Mistake #8: Overlooking Coating and Corrosion Protection
Pipe coating specifications are frequently given insufficient attention, despite coating failures being a primary cause of premature pipe deterioration.
Coating Consideration Checklist:
- External environmental factors (soil conditions, moisture, temperature)
- Internal product characteristics (corrosivity, abrasiveness)
- Expected service life requirements
- Installation method impacts on coating
- Cathodic protection compatibility
- Field joint coating requirements
WUZHOU’s specialized coating production lines highlight the importance of this aspect: “Our dedicated coating and lining production facilities ensure pipes receive appropriate protection tailored to their intended service environment, significantly extending service life and reducing maintenance requirements.”
Mistake #9: Failure to Consider Installation Methods
The installation method for spiral welded pipes can significantly impact required specifications, yet is often overlooked during procurement.
Installation-Related Specifications:
- Field welding requirements for joint design
- Handling restrictions during installation
- Minimum bend radius for directional drilling
- End protection during transportation and storage
- Special lifting point requirements
- Field testing protocols
Mistake #10: Not Establishing Clear Acceptance Criteria
Ambiguous acceptance criteria lead to disputes during inspection and potential delays in project completion.
Effective Acceptance Strategy:
- Define quantitative acceptance criteria whenever possible
- Specify allowable defect types, sizes, and frequencies
- Clarify repair limitations and procedures
- Establish variance request procedures
- Define resolution process for inspection disputes
- Document inspection verification methods
“Establishing clear acceptance criteria upfront is crucial to avoiding disputes and ensuring on-time project execution,” notes WUZHOU’s Quality Assurance Manager. “Our transparent quality control process and comprehensive testing regime eliminate ambiguity and provide customers with confidence in our products.”
4. How to Evaluate Supplier Qualifications and Manufacturing Capabilities
The difference between a successful pipeline project and one plagued with problems often comes down to supplier selection. This critical decision requires a systematic evaluation process that looks beyond marketing materials and price quotes to assess true manufacturing capabilities.
4.1 Essential Supplier Qualification Criteria
When evaluating potential spiral welded pipe suppliers, procurement professionals should assess several key areas:
Manufacturing Infrastructure Assessment
The supplier’s production facilities directly impact their ability to deliver quality products consistently and on schedule. Important factors to evaluate include:
- Production Line Configuration: Number, type, and age of spiral pipe manufacturing lines
- Maximum/Minimum Capacity: Diameter range, wall thickness capabilities, and length limitations
- Coating and Lining Facilities: In-house capabilities versus outsourced processes
- Materials Handling Equipment: Capacity for heavy coils, finished pipe movement, and loading
- Testing Facilities: On-site capabilities for mechanical, chemical, and non-destructive testing
WUZHOU exemplifies strong manufacturing infrastructure with its comprehensive facilities: “With 3 subsidiaries, 2 factories, 4 production bases, 6 production workshops, 11 spiral pipe production lines, and 2 coating lining production lines, we maintain an annual output value of 400,000 tons of spiral welded pipes. This robust infrastructure ensures we can produce multiple specifications while maintaining consistent quality.”
Technical Expertise and Experience
The supplier’s technical knowledge and industry experience significantly impact product quality:
- Engineering Staff Qualifications: Education, certifications, and years of experience
- Manufacturing Process Expertise: Demonstrated knowledge of welding metallurgy and process controls
- Quality Control Personnel: Training, certification, and experience in pipe inspection
- Product Development Capabilities: History of innovation and problem-solving
- Similar Project Experience: Track record with applications similar to your requirements
Table 4: Supplier Technical Qualification Assessment Framework
Evaluation Area | Key Performance Indicators | Documentation to Request | Red Flags to Watch For |
---|---|---|---|
Engineering Team | Years of experience, professional certifications | Staff credentials, technical papers published | High turnover, limited spiral pipe-specific knowledge |
Production Expertise | Process controls, weld quality, dimensional accuracy | Manufacturing procedures, process validation records | Outsourcing of critical processes, limited automation |
Quality Systems | Inspection methods, defect rates, traceability | Quality manual, inspection procedures, test capabilities | Manual-only inspection, limited test equipment |
Problem Resolution | Response time, technical solutions provided | Case studies, reference feedback | Unresolved quality issues, pattern of disputes |
Industry Knowledge | Understanding of application requirements | Industry participation, compliance with latest standards | Unfamiliarity with industry-specific requirements |
Quality Management Systems
A robust quality management system is essential for consistent manufacturing quality:
- Certifications and Compliance: ISO 9001, API Q1, and industry-specific certifications
- Quality Control Procedures: Documented processes for all manufacturing stages
- In-Process Inspection: Methods and frequency of quality checks during production
- Final Testing Protocols: Standardized final inspection and testing procedures
- Documentation Systems: Material traceability and quality records management
- Nonconformance Handling: Procedures for identifying, addressing, and preventing defects
WUZHOU’s commitment to quality is evidenced by their comprehensive certification portfolio: “We uphold the highest industry standards with internationally recognized certifications. Our double-sided submerged arc welded spiral steel pipes have passed the API 5L standard of the American Petroleum Institute and the EU standard. We also maintain ISO 9001 and ISO 14001 quality management systems and Environmental Management System Certification.”
Production Capacity and Scheduling Flexibility
Evaluate the supplier’s ability to accommodate your order within your required timeline:
- Current Order Backlog: Existing commitments that might impact your project schedule
- Production Capacity Utilization: Current percentage of capacity in use
- Scheduling Flexibility: Ability to accommodate urgent orders or schedule changes
- Raw Material Supply Chain: Relationships with steel suppliers and inventory management
- Contingency Planning: Backup systems and recovery procedures for production interruptions
4.2 Conducting Effective Supplier Audits
For major pipeline projects, conducting on-site supplier audits is a valuable practice that provides insights not available through documentation review alone.
Pre-Audit Preparation:
- Develop a structured audit checklist based on project requirements
- Review supplier’s quality manual and key procedures before the visit
- Identify critical processes and inspection points to observe
- Prepare specific technical questions based on your application
Key Areas to Evaluate During Audits:
- Raw Material Receiving and Inspection:
- Material verification procedures
- Storage conditions and inventory management
- Traceability systems and marking
- Manufacturing Process Controls:
- Coil preparation and edge milling
- Forming process controls and monitoring
- Welding parameter monitoring and recording
- Heat treatment processes (if applicable)
- Dimensional control methods
- Inspection and Testing Capabilities:
- Calibration of measurement and test equipment
- Non-destructive testing methods and equipment
- Mechanical testing facilities and procedures
- Hydrostatic testing capabilities
- Staff qualification and certification
- Coating and Lining Processes:
- Surface preparation methods
- Application procedures and environmental controls
- Coating thickness measurement and quality checks
- Coating repair procedures
- Finished Product Handling and Storage:
- End protection methods
- Loading and securing practices
- Storage conditions and inventory management
Post-Audit Assessment:
- Document findings and observations systematically
- Identify strengths and weaknesses relative to project requirements
- Request corrective actions for any critical gaps identified
- Consider production trial orders before major commitments
4.3 Evaluating Supplier Track Record and Reputation
Historical performance is often the best predictor of future reliability. Investigate potential suppliers’:
- Project References: Contact previous customers with similar applications
- Delivery Performance: On-time delivery percentage and causes of delays
- Quality History: Rejection rates, warranty claims, and recurring issues
- Problem Resolution: Responsiveness to issues and effectiveness of solutions
- Financial Stability: Company longevity and financial health indicators
“WUZHOU stands for unmatched precision, superior quality, and unwavering trust,” notes a long-term client in the oil and gas sector. “Their state-of-the-art production, strict quality control, and dedication to customer satisfaction have made them our preferred supplier for critical pipeline projects.”
4.4 Red Flags in Supplier Evaluation
Be alert for warning signs that might indicate potential problems:
- Reluctance to provide detailed manufacturing information
- Resistance to quality requirements or testing standards
- Limited similar project experience or references
- Excessive focus on price negotiations rather than technical requirements
- Inability to provide proper certifications or test reports
- High staff turnover in key technical or quality positions
- Poorly maintained facilities or outdated equipment
- Inconsistent communication or responsiveness during evaluation
By thoroughly evaluating potential suppliers against these criteria, procurement professionals can significantly reduce the risk of supply chain disruptions, quality problems, and project delays.
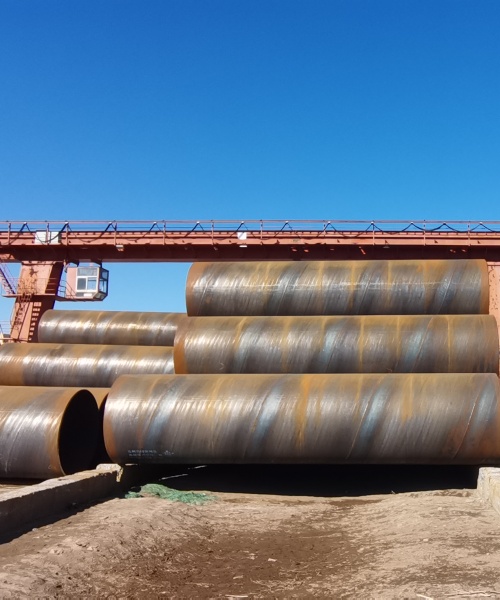
5. Quality Control: Essential Testing Methods for Spiral Welded Pipes
Quality assurance for spiral welded pipes involves multiple inspection and testing methods throughout the manufacturing process. Understanding these methods helps procurement professionals specify appropriate quality requirements and interpret test results.
5.1 Raw Material Verification and Testing
Quality control begins with the steel coil used to manufacture spiral welded pipes:
Chemical Composition Analysis:
- Spectrographic analysis to verify elements including carbon, manganese, phosphorus, sulfur, and alloying elements
- Results must comply with specified steel grade requirements
- Special attention to carbon equivalent for weldability assessment
Mechanical Property Testing:
- Tensile testing to verify yield strength, tensile strength, and elongation
- Impact testing to assess toughness at specified temperatures
- Hardness testing for consistency verification
Coil Surface Inspection:
- Visual and automated inspection for surface defects
- Thickness measurement for consistency
- Edge condition assessment for welding preparation
WUZHOU’s approach to raw material quality exemplifies industry best practices: “We provide raw material reports for every spiral welded steel pipe. From the selection of raw materials to the completion of production, we ensure the quality of each spiral welded pipe through rigorous verification and testing.”
Table 5: Critical Raw Material Testing Requirements
Test Type | Standard Method | Acceptance Criteria | Frequency | Documentation |
---|---|---|---|---|
Chemical Analysis | ASTM A751 | Per grade specification (API 5L, ASTM A252, etc.) | Each heat/lot | Chemical analysis report |
Tensile Testing | ASTM A370 | Per grade specification | Each heat/lot | Mechanical test report |
Impact Testing | ASTM A370/E23 | Minimum energy absorption at specified temperature | Each heat/lot | Impact test report |
Ultrasonic Inspection | ASTM A578 | No laminations exceeding specified size | As specified | UT inspection report |
Surface Inspection | Visual/Automated | No defects exceeding allowable limits | 100% | Inspection report |
5.2 In-Process Inspection and Testing
During manufacturing, several critical quality control points must be monitored:
Forming Process Controls:
- Spiral forming angle verification
- Edge alignment monitoring
- Dimensional checks during forming
Welding Process Monitoring:
- Welding parameter verification and recording (current, voltage, travel speed)
- Shielding gas flow and composition (for certain welding processes)
- Weld bead profile and appearance inspection
- Weld temperature monitoring when applicable
Post-Weld Inspection:
- Visual inspection of weld quality
- Weld reinforcement height measurement
- Automated ultrasonic testing (AUT) of weld seams
- Radiographic testing of welds (sampling or 100% as specified)
Table 6: Common Welding Defects and Detection Methods
Defect Type | Potential Causes | Primary Detection Method | Secondary Verification |
---|---|---|---|
Lack of Fusion | Improper welding parameters, poor edge preparation | Ultrasonic Testing (UT) | Radiographic Testing (RT) |
Porosity | Moisture, contamination, improper gas shielding | Radiographic Testing (RT) | Visual Inspection |
Undercut | Excessive current, improper angle | Visual Inspection | Magnetic Particle Testing |
Incomplete Penetration | Inadequate root gap, excessive travel speed | Ultrasonic Testing (UT) | Radiographic Testing (RT) |
Cracks | High restraint, hydrogen contamination | Magnetic Particle Testing (MT) | Penetrant Testing (PT) |
Slag Inclusion | Inadequate cleaning between passes | Radiographic Testing (RT) | Ultrasonic Testing (UT) |
5.3 Final Inspection and Testing Methods
Completed spiral welded pipes undergo comprehensive testing before acceptance:
Dimensional Inspection:
- Outside diameter measurement at multiple points
- Wall thickness verification
- Straightness and roundness assessment
- End squareness checking
- Overall length verification
Non-Destructive Examination:
- Ultrasonic Testing (UT): Detects internal defects such as laminations, lack of fusion, and cracks
- Radiographic Testing (RT): Provides visual confirmation of weld quality and internal defects
- Magnetic Particle Inspection (MPI): Identifies surface and near-surface defects in the weld area
- Liquid Penetrant Testing (PT): Alternative method for detecting surface-breaking defects
Hydrostatic Testing:
- Pressure testing to verify structural integrity
- Typically performed at 1.5 times the design pressure
- Minimum hold time as specified by applicable standards
- Visual inspection for leaks during testing
Mechanical and Metallurgical Testing:
- Flattening tests to verify weld integrity
- Guided bend tests for weld ductility assessment
- Macro-etching for weld profile examination
- Hardness testing in the weld and heat-affected zone
WUZHOU’s comprehensive testing protocol ensures product reliability: “Every spiral steel pipe produced by our factory is quality inspected through water pressure tests, ultrasonic tests, and X-ray tests. This rigorous approach ensures that our products meet or exceed client specifications and industry standards.”
5.4 Coating and Lining Inspection
For coated pipes, additional quality checks are essential:
Surface Preparation Inspection:
- Blast cleaning profile measurement
- Surface cleanliness assessment
- Salt contamination testing when specified
- Temperature and humidity monitoring
Coating Application Inspection:
- Wet and dry film thickness measurement
- Holiday (pinhole) detection
- Adhesion testing
- Cure testing for certain coating types
Coating Performance Testing:
- Impact resistance testing
- Cathodic disbondment testing
- Water immersion testing
- Chemical resistance verification
5.5 Documentation and Traceability Requirements
Complete documentation is essential for quality assurance and regulatory compliance:
Essential Documentation Package:
- Material Test Reports (MTRs) for steel coil
- Manufacturing Process Records
- Dimensional Inspection Reports
- Non-Destructive Examination Reports
- Hydrostatic Test Records
- Coating Inspection Reports
- Certificate of Compliance to Specified Standards
- Traceability Documentation (heat numbers, lot identifiers)
“From raw material selection through final testing, we maintain comprehensive documentation for every pipe we produce,” explains WUZHOU’s Quality Assurance Manager. “This documentation provides our customers with confidence in our products and facilitates their compliance with project and regulatory requirements.”
5.6 Third-Party Inspection Considerations
For critical applications, third-party inspection provides additional verification:
Inspection Agency Selection Criteria:
- Accreditation and certification status
- Experience with spiral welded pipe manufacturing
- Familiarity with applicable standards and specifications
- Personnel qualifications and certifications
- References from similar projects
Inspection Witness and Hold Points:
- Clearly define required witness and hold points in purchase documentation
- Typical witness points include:
- Material verification
- First article inspection
- Welding procedure qualification
- Production welding witness
- Non-destructive examination verification
- Hydrostatic testing
- Final inspection and release
Third-Party Inspector Qualifications:
- API, ASNT, AWS, or equivalent certifications
- Specific experience with spiral welded pipe inspection
- Familiarity with testing methods and acceptance criteria
By specifying appropriate quality control requirements and thoroughly evaluating test results, procurement professionals can significantly reduce the risk of receiving non-conforming products that could lead to project failures or safety incidents.
6. Cost Considerations: Looking Beyond the Price Tag
While purchase price is undoubtedly important, true cost-effective procurement of spiral welded pipes requires considering multiple factors that contribute to total lifecycle costs.
6.1 Understanding Total Cost of Ownership (TCO)
Total Cost of Ownership analysis provides a comprehensive view of all costs associated with spiral welded pipe procurement and use:
Initial Acquisition Costs:
- Base pipe material cost
- Special material requirements premium
- Coating and lining costs
- Testing and inspection costs
- Transportation and logistics expenses
- Import duties and taxes (for international procurement)
Installation and Commissioning Costs:
- Field welding and joining expenses
- Special handling requirements
- Field testing costs
- Remediation of any quality issues
- Project delays due to material issues
Operational Lifetime Costs:
- Expected service life before replacement
- Maintenance and repair frequency
- Inspection and monitoring requirements
- Downtime costs associated with failures
- Environmental and safety risk exposure
End-of-Life and Replacement Costs:
- Decommissioning expenses
- Disposal or recycling costs
- Replacement timeline and inflation factors
Table 7: TCO Comparison Example for Pipeline Project
Cost Factor | Standard Spiral Pipe | Premium Spiral Pipe (e.g., WUZHOU) | Cost Differential |
---|---|---|---|
Initial Purchase | $1,000,000 | $1,150,000 | +$150,000 (15%) |
Transportation | $120,000 | $120,000 | $0 |
Installation | $350,000 | $315,000 | -$35,000 (-10%) |
Field Rework | $75,000 | $15,000 | -$60,000 (-80%) |
Maintenance (20 yr) | $400,000 | $200,000 | -$200,000 (-50%) |
Service Life | 25 years | 40 years | +15 years (+60%) |
Replacement Cost | $2,300,000 (at year 25) | Not required within 40-year project life | -$2,300,000 (-100%) |
Total 40-year TCO | $4,245,000 | $1,800,000 | -$2,445,000 (-58%) |
This example illustrates how premium quality pipes from manufacturers like WUZHOU may have higher initial costs but can deliver significantly lower total cost of ownership over the project lifecycle.
6.2 Cost-Quality Relationship Analysis
Understanding the relationship between cost and quality helps procurement professionals make informed decisions:
Quality Factors That Justify Premium Pricing:
- Superior raw material selection
- Advanced manufacturing processes
- Enhanced inspection and testing
- Specialized coatings and linings
- Proven long-term performance
- Comprehensive quality documentation
- Responsive technical support
False Economy Warning Signs:
- Prices significantly below market average
- Reluctance to provide quality verification
- Limited warranty coverage
- History of quality issues or failures
- Incomplete documentation
- Limited technical support capabilities
“The difference between a good pipe and an excellent pipe often represents only 10-15% of the purchase price,” notes a senior pipeline engineer, “but that difference can translate to 50% longer service life and 70% fewer maintenance issues. WUZHOU’s focus on quality delivers this kind of long-term value to our projects.”
6.3 Value-Added Services Impact on Total Cost
Many suppliers offer value-added services that can significantly reduce total project costs:
Technical Consultation Services:
- Application-specific material selection guidance
- Design optimization recommendations
- Corrosion protection strategy development
- Installation method consultation
Supply Chain Optimization:
- Just-in-time delivery scheduling
- Custom packaging for specific site conditions
- Specialized transportation arrangements
- Inventory management assistance
Field Support Services:
- On-site technical advisors during installation
- Field welding procedure development
- Troubleshooting assistance
- Commissioning support
Documentation and Compliance Services:
- Customized quality documentation packages
- Regulatory compliance assistance
- Digital documentation management
- Material traceability systems
WUZHOU exemplifies this comprehensive approach: “Beyond manufacturing excellence, we provide extensive technical support throughout the project lifecycle. Our engineering team works with customers to optimize specifications, resolve installation challenges, and ensure long-term performance, delivering value far beyond the physical product.”
6.4 Risk Mitigation Value
The cost of risk should be quantified when evaluating procurement options:
Project Delay Risk:
- Lost revenue from delayed operation
- Contract penalties for schedule overruns
- Additional project management costs
- Financing impact of extended timelines
Quality Failure Risk:
- Repair or replacement costs
- Operational downtime losses
- Environmental remediation expenses
- Regulatory penalties
- Reputational damage
Supply Chain Disruption Risk:
- Emergency procurement premiums
- Expediting fees for urgent replacements
- Project schedule recovery costs
- Contractor standby charges
Table 8: Quantifying Risk Mitigation Value
Risk Category | Probability with Standard Supplier | Probability with Premium Supplier | Potential Cost Impact | Risk-Adjusted Value Difference |
---|---|---|---|---|
Major Quality Failure | 5% | 0.5% | $2,000,000 | $90,000 |
Moderate Quality Issues | 15% | 3% | $500,000 | $60,000 |
Delivery Delay (>30 days) | 10% | 2% | $300,000 | $24,000 |
Documentation Deficiencies | 20% | 1% | $100,000 | $19,000 |
Total Risk-Adjusted Value | $193,000 |
This analysis demonstrates that the risk mitigation value of selecting a premium supplier like WUZHOU can substantially offset higher initial pricing, even before considering operational benefits.
6.5 Cost Optimization Strategies
Several strategies can help optimize the cost-value equation in spiral welded pipe procurement:
Specification Optimization:
- Ensure specifications are appropriate but not excessive for the application
- Consider performance-based specifications rather than prescriptive requirements
- Standardize specifications across projects when possible to leverage volume
Strategic Supplier Relationships:
- Develop long-term relationships with proven suppliers like WUZHOU
- Consider framework agreements for multiple projects
- Explore strategic alliances that align supplier success with project outcomes
Procurement Timing:
- Monitor steel market trends and time major purchases accordingly
- Consider advance purchases during favorable market conditions
- Balance inventory carrying costs against price volatility protection
Value Engineering:
- Collaborate with suppliers to identify cost-saving alternatives
- Consider total installed cost when evaluating options
- Explore innovative solutions that reduce lifetime costs
By looking beyond the price tag to consider these comprehensive cost factors, procurement professionals can make truly value-optimized decisions that benefit their organizations over the entire infrastructure lifecycle.
7. Logistics and Supply Chain Challenges in Spiral Pipe Procurement
The physical characteristics of spiral welded pipes—their size, weight, and length—create unique logistics challenges that must be addressed during procurement planning. Failure to consider these factors can lead to significant cost overruns, schedule delays, and damaged materials.
7.1 Transportation Planning and Considerations
The transportation of spiral welded pipes requires careful planning and specialized equipment:
Mode Selection Factors:
- Ocean Freight: Often necessary for international procurement, requiring special handling at ports
- Rail Transport: Efficient for long distances, but limited by rail infrastructure and loading facilities
- Truck Transportation: Provides flexibility but faces length and weight restrictions
- Barge Shipping: Suitable for waterway-accessible projects, but weather-dependent and slower
Critical Dimensional Considerations:
- Maximum pipe length based on transportation mode constraints
- Diameter limitations for road transport (oversized load regulations)
- Weight restrictions on highways and bridges
- Stacking limitations during transport
Table 9: Transportation Mode Comparison for Spiral Welded Pipes
Transport Mode | Typical Max Length | Weight Capacity | Cost Efficiency | Handling Considerations | Typical Lead Time |
---|---|---|---|---|---|
Ocean Freight | No practical limit | Very high | High for long distances | Port handling, marine exposure | 4-8 weeks |
Rail | Up to 80 ft (24m) | Very high | Medium-high | Loading/unloading facilities required | 2-4 weeks |
Truck (standard) | 40-45 ft (12-14m) | Limited by road regulations | Medium | More flexible delivery locations | 1-2 weeks |
Truck (oversized) | Up to 80 ft (24m) | Limited by permits | Low-medium | Permits, escorts, route restrictions | 2-3 weeks |
Barge | No practical limit | Very high | Medium | Waterway access required | 3-6 weeks |
Transportation Cost Optimization:
- Maximize loading efficiency (weight and space utilization)
- Coordinate deliveries to reduce partial loads
- Consider pipe nesting for certain diameters
- Evaluate multi-modal transportation options
- Schedule deliveries to avoid peak shipping rates
WUZHOU’s logistics experts note: “Transportation planning should begin during the specification phase. By optimizing pipe lengths to match both application requirements and logistical constraints, we can help customers significantly reduce transportation costs while ensuring safe delivery.”
7.2 Packaging and Protection Requirements
Proper packaging is essential to prevent damage during transportation and storage:
End Protection Options:
- Plastic caps or plugs to prevent debris entry and protect beveled ends
- Steel protectors for heavy-duty applications
- Weather-resistant coverings for extended storage
Pipe Body Protection:
- External coating protection methods
- Protective wrapping for coated pipes
- Separation materials to prevent damage during stacking
- UV protection for extended storage
Bundle Securing Methods:
- Steel strapping requirements and spacing
- Wooden dunnage specifications and placement
- Bundle size optimization for handling
Special Requirements for Coated Pipes:
- Padding between pipes to protect coating
- Temperature considerations during transport and storage
- Handling restrictions to prevent coating damage
“Proper packaging isn’t just about preventing physical damage,” explains WUZHOU’s shipping coordinator. “It’s about preserving the integrity of the entire pipe system, particularly for coated products where surface protection is critical to long-term performance.”
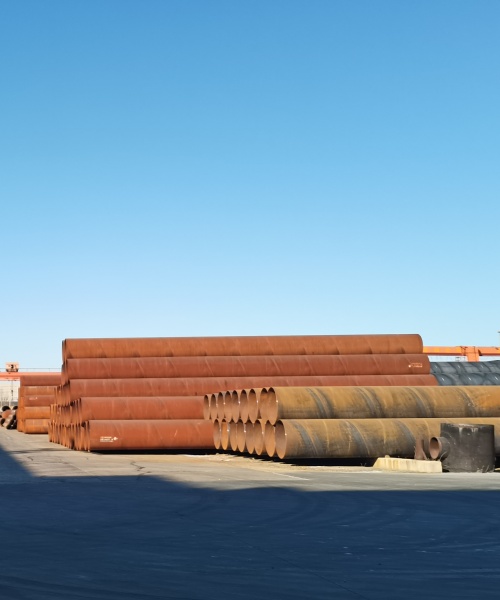
7.3 Receiving and Storage Best Practices
Upon delivery, proper handling and storage procedures are essential:
Receiving Inspection Checklist:
- Visual inspection for transportation damage
- Verification of pipe markings and traceability information
- Coating inspection (if applicable)
- Documentation review and verification
- Quantity verification against shipping documents
Storage Area Requirements:
- Level, well-drained surface
- Sufficient space for organization by size and heat number
- Protection from contaminants and debris
- Security considerations for valuable materials
Stacking and Support Guidelines:
- Maximum stack height recommendations
- Proper dunnage placement and spacing
- End alignment considerations
- Separation of different sizes and specifications
Storage Period Considerations:
- Periodic inspection requirements for long-term storage
- Rotation of stock for extended storage periods
- Additional protection for prolonged exposure to elements
- Special considerations for coated pipes
Table 10: Pipe Storage Best Practices
Storage Factor | Best Practice | Consequences of Non-Compliance | Maintenance Requirements |
---|---|---|---|
Ground Preparation | Level, compacted surface with drainage | Pipe deformation, coating damage | Periodic inspection and maintenance |
Support Spacing | 1/4 points minimum, aligned vertically in stacks | Pipe bending, coating damage | Check alignment after pipe movement |
Maximum Stack Height | Typically 3-4 meters (varies by diameter) | Stack collapse, worker safety hazards | Regular stability inspection |
Weather Protection | End caps, tarps for coated pipe | Corrosion, coating degradation, debris accumulation | Inspection after severe weather events |
Segregation | By size, specification, heat number | Material mix-up, project delays | Clear marking and organization system |
7.4 International Procurement Challenges
For global procurement, additional factors come into play:
Import Documentation Requirements:
- Commercial invoice requirements
- Packing list specifications
- Certificate of origin
- Inspection certificates
- Compliance with importing country regulations
Customs Clearance Considerations:
- Harmonized tariff code identification
- Duty and tax calculations
- Import license requirements (where applicable)
- Customs broker selection and management
International Quality Verification:
- Third-party inspection requirements
- Pre-shipment inspection protocols
- Laboratory testing and certification
Contractual Protections:
- Appropriate Incoterms selection (FOB, CIF, DDP, etc.)
- Payment terms and security instruments
- Quality claim procedures
- Force majeure provisions
WUZHOU’s experience with international shipping provides valuable insights: “We’ve developed comprehensive protocols for international deliveries, ensuring proper documentation, packaging, and coordination with shipping partners. This systematic approach minimizes delays at customs and ensures pipes arrive in optimal condition regardless of destination.”
7.5 Just-In-Time Delivery Coordination
For large projects, coordinating deliveries to match installation schedules can provide significant benefits:
JIT Benefits:
- Reduced on-site storage requirements
- Minimized material handling
- Lower risk of damage or deterioration
- Improved cash flow management
- Enhanced coordination with installation activities
JIT Implementation Requirements:
- Detailed installation schedule development
- Supplier production capacity reservation
- Clear communication protocols for schedule changes
- Contingency planning for potential delays
- Buffer stock strategy for critical components
Sequence Delivery Planning:
- Delivery organization based on installation sequence
- Load planning to match daily installation requirements
- Identification marking for installation location
- Documentation organization by installation zone
7.6 Contingency Planning for Supply Chain Disruptions
Robust procurement strategies include plans for managing potential disruptions:
Common Supply Chain Risks:
- Raw material shortages or price volatility
- Production capacity constraints
- Transportation disruptions or delays
- Geopolitical issues affecting international shipments
- Extreme weather events
- Labor disputes affecting production or logistics
Mitigation Strategies:
- Multiple qualified supplier relationships
- Strategic inventory buffers for critical items
- Alternative transportation mode identification
- Regular supplier capability assessment
- Contractual protections and incentives
By addressing these logistics and supply chain considerations proactively, procurement professionals can prevent costly delays and ensure materials arrive in optimal condition for installation.
8. Long-term Partnership Benefits: Why Supplier Relationships Matter
In the context of industrial pipe procurement, transactional purchasing approaches often fail to deliver optimal value. Developing strategic supplier relationships, particularly with established manufacturers like WUZHOU, can yield substantial benefits over time.
8.1 Evolution from Vendor to Strategic Partner
The supplier relationship continuum represents various engagement levels, each offering different value propositions:
Transactional Vendor:
- Focused primarily on price and basic compliance
- Limited information sharing and collaboration
- Reactive problem-solving approach
- Minimal performance feedback
Preferred Supplier:
- Regular business volume with preferential terms
- Basic information sharing on requirements
- Responsive to special requests
- Performance monitoring and feedback
Strategic Partner:
- Deep understanding of business needs and challenges
- Proactive problem-solving and innovation
- Collaborative planning and continuous improvement
- Mutual investment in relationship success
“Our most successful client relationships have evolved from basic transactions to true partnerships,” notes WUZHOU’s Business Development Director. “When we understand a customer’s business challenges and long-term goals, we can deliver far greater value than simply providing compliant products at competitive prices.”
8.2 Tangible Benefits of Strategic Supplier Relationships
Research consistently demonstrates that strategic supplier relationships deliver measurable advantages:
Quality and Performance Improvements:
- Reduced defect rates and non-conformances
- Customized solutions for specific application challenges
- Continuous product and process improvement
- Enhanced technical support and problem resolution
Cost Optimization Beyond Price:
- Reduced total cost of ownership
- Process efficiency improvements
- Inventory optimization opportunities
- Reduced quality-related costs
Supply Chain Resilience:
- Higher priority during capacity constraints
- More flexible response to changing requirements
- Better communication during disruptions
- Collaborative contingency planning
Innovation and Knowledge Transfer:
- Earlier access to new technologies and processes
- Collaborative product development opportunities
- Industry insights and market intelligence
- Technical expertise and application knowledge
Table 11: Strategic Partnership Value Metrics
Value Category | Typical Improvement | Measurement Approach | Examples from WUZHOU Partnerships |
---|---|---|---|
Quality Performance | 40-60% reduction in defects | Defect rates, field failures | 57% reduction in field issues over 3 years |
Total Cost | 15-25% reduction in TCO | Life-cycle cost analysis | 22% total cost reduction for major pipeline operator |
Supply Assurance | 30-50% reduction in delays | On-time delivery, lead time variance | 98.3% on-time delivery during material shortages |
Technical Support | 50-70% faster resolution | Response time, solution effectiveness | Same-day technical support response |
Innovation | 2-3x more improvement ideas | Implemented suggestions, value improvements | Joint development of enhanced coating system |
8.3 Building Effective Supplier Relationships
Developing strategic supplier relationships requires intentional effort and commitment:
Information Sharing and Transparency:
- Share long-term project pipelines and forecasts
- Communicate business challenges and priorities
- Provide clear feedback on performance
- Maintain open dialogue about market conditions
Fair and Balanced Commercial Approaches:
- Recognize value beyond lowest price
- Develop mutually beneficial commercial terms
- Share risks and rewards appropriately
- Consider total cost impact in negotiations
Collaborative Problem-Solving:
- Involve suppliers early in problem identification
- Focus on solutions rather than blame
- Leverage supplier expertise and experience
- Document lessons learned for future improvement
Performance Management and Recognition:
- Establish clear performance metrics and expectations
- Provide regular feedback on performance
- Recognize and reward exceptional performance
- Address issues promptly and constructively
WUZHOU exemplifies this collaborative approach: “We view ourselves as an extension of our customers’ teams. Our technical experts work closely with client engineers to optimize specifications, troubleshoot challenges, and identify opportunities for improvement. This collaborative approach has resulted in significant cost savings and performance enhancements for our partners.”
8.4 Technology Collaboration Opportunities
Advanced suppliers can contribute significantly to technological advancement:
Digital Documentation and Traceability:
- Electronic material certification and test reports
- QR-coded traceability systems
- Cloud-based documentation management
- Real-time production status tracking
Advanced Testing and Validation:
- Custom testing protocols for specific applications
- Accelerated life testing methodologies
- Field performance correlation studies
- Application-specific validation methods
Manufacturing Process Innovation:
- Advanced welding technology implementation
- Automated inspection and quality control
- Enhanced coating application methods
- Specialized end treatments and connections
WUZHOU demonstrates leadership in technological innovation: “Our state-of-the-art production, strict quality control, and dedication to customer satisfaction set the standard in the steel pipe manufacturing industry. We continuously invest in advanced technology to improve product performance and manufacturing efficiency.”
8.5 Long-term Agreement Structures
For ongoing procurement needs, formalized long-term agreements can provide structure for strategic relationships:
Framework Agreement Benefits:
- Simplified procurement process for repeat orders
- Volume-based pricing incentives
- Capacity reservation and priority production
- Streamlined quality requirements and testing
- Collaborative continuous improvement mechanisms
Key Agreement Components:
- Performance metrics and expectations
- Pricing mechanisms and adjustment procedures
- Quality requirements and verification methods
- Technical support and service levels
- Issue resolution procedures
- Continuous improvement targets
- Term and renewal provisions
By investing in strategic supplier relationships, organizations can transform procurement from a transactional function to a strategic advantage that enhances product quality, reduces total costs, and improves operational performance.
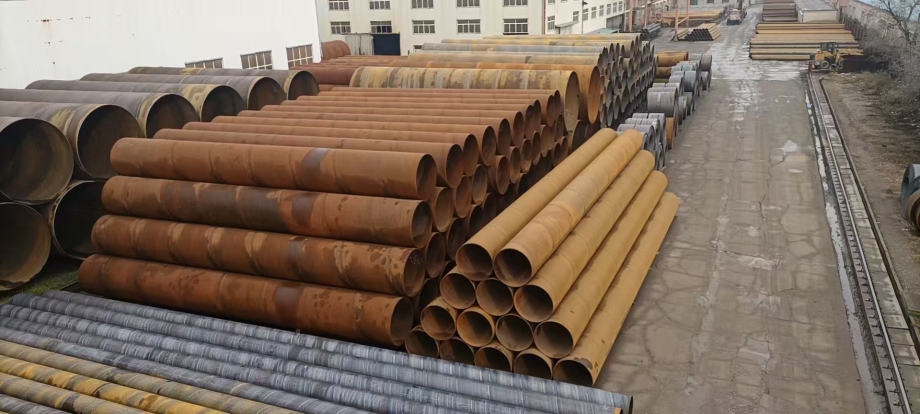
9. FAQs: Expert Answers to Common Questions About Spiral Welded Pipe Purchasing
Q1: What is the key difference between spiral welded pipe and longitudinal welded pipe?
Answer: The primary difference lies in the welding seam orientation and manufacturing process. Spiral welded pipes feature a helical weld seam that spirals around the pipe circumference, while longitudinal welded pipes have straight seams running parallel to the pipe axis.
Spiral welded pipes offer several distinct advantages:
- Material Efficiency: Spiral pipes can be manufactured from narrower steel coils, allowing more flexible raw material sourcing and often better material properties.
- Size Range Flexibility: Manufacturers like WUZHOU can produce various diameters using the same steel coil width by adjusting the spiral angle.
- Enhanced Pressure Resistance: The spiral weld distributes stress more evenly around the circumference, potentially offering better pressure performance.
- Larger Diameter Capabilities: Spiral welding enables the production of very large diameter pipes (up to 120 inches or more) that would be difficult to manufacture with longitudinal welding.
Longitudinal welded pipes have traditionally been preferred for certain high-pressure applications, but advances in spiral welding technology by manufacturers like WUZHOU have narrowed this gap significantly. Modern double-sided submerged arc welded spiral pipes meet or exceed the performance of longitudinal pipes in most applications.
Q2: What are the most important standards and specifications for spiral welded pipe procurement?
Answer: Several key standards govern spiral welded pipe manufacturing and testing:
API 5L: The American Petroleum Institute standard for line pipe, which covers pipes used in oil and gas transmission. This comprehensive standard defines requirements for chemical composition, mechanical properties, dimensions, testing, and inspection for various pipe grades (from B to X80).
ASTM A252: Standard specification for welded steel pipe piles, commonly used for foundation piling, marine structures, and similar applications. This standard covers three grades with different strength requirements.
AWWA C200: American Water Works Association standard for steel water pipe, focused on pipes for water transmission and distribution systems. This standard addresses requirements specific to potable water applications.
ISO 3183: International standard for petroleum and natural gas industries – Steel pipe for pipeline transportation systems. This standard harmonizes requirements globally and includes provisions for sour service and offshore applications.
EN 10219: European standard for cold-formed welded structural hollow sections, which includes spiral welded pipes used in structural applications.
For specific applications, additional standards may apply:
- ASME B31.3: Process piping requirements
- ASME B31.4: Pipeline transportation systems for liquid hydrocarbons
- ASME B31.8: Gas transmission and distribution piping systems
- DNV-OS-F101: Submarine pipeline systems (for offshore applications)
WUZHOU’s comprehensive certification portfolio ensures compliance with these global standards: “Our double-sided submerged arc welded spiral steel pipes have passed the API 5L standard of the American Petroleum Institute and the EU standard. We also maintain ISO 9001 and ISO 14001 quality management systems and Environmental Management System Certification.”
Q3: How do I determine the appropriate wall thickness for my spiral welded pipe application?
Answer: Determining the appropriate wall thickness involves considering multiple factors:
Internal Pressure Requirements:
The primary calculation for pressure-containing pipes uses the hoop stress formula:
t = (P × D) / (2 × S × F × E)
Where:
- t = required wall thickness
- P = design pressure
- D = pipe outside diameter
- S = allowable stress value for the material
- F = design factor (safety factor)
- E = weld joint efficiency factor
External Load Considerations:
For buried pipes or those subject to external loads, additional calculations are required:
- Soil overburden pressure
- Traffic or surface loads
- Vacuum or external pressure conditions
- Handling and installation stresses
Corrosion Allowance:
Add additional thickness to account for:
- Internal corrosion/erosion rate × design life
- External corrosion potential
- Manufacturing tolerance (typically subtract from the calculated thickness)
Applicable Code Requirements:
Different standards prescribe minimum thicknesses and calculation methods:
- API 5L provides minimum thickness for each pipe diameter
- ASME B31.3/B31.4/B31.8 provide calculation methods for process and pipeline applications
- AWWA C200 addresses water transmission requirements
WUZHOU’s engineering team can provide valuable support in this determination: “Our technical experts regularly assist customers in optimizing wall thickness calculations to ensure safety and compliance while avoiding unnecessary over-specification that adds cost without benefit. This collaborative approach ensures the most cost-effective solution that meets all performance requirements.”
Q4: What coating systems are recommended for buried spiral welded pipe applications?
Answer: Several coating systems are suitable for buried pipelines, each with specific advantages:
Fusion Bonded Epoxy (FBE):
- Single-layer epoxy powder coating applied to heated pipe
- Excellent corrosion protection and adhesion
- Good resistance to soil stress and moderate temperatures
- Relatively thin coating (14-28 mils) with excellent adhesion
- Widely accepted in oil, gas, and water industries
Three-Layer Polyethylene/Polypropylene (3LPE/3LPP):
- System consisting of epoxy primer, adhesive middle layer, and PE/PP outer layer
- Superior mechanical protection combined with excellent corrosion resistance
- Better resistance to higher temperatures (3LPP) and mechanical damage
- Thicker system (60-120 mils) providing enhanced protection
- Ideal for directional drilling installations and rocky terrains
Liquid Epoxy:
- Field-applied system used primarily for joint coatings
- Compatible with most factory-applied systems
- Variable thickness depending on application method
- Good corrosion protection when properly applied
Coal Tar Enamel:
- Traditional coating with excellent water resistance
- Less commonly used in new installations
- Good performance in wet burial conditions
- Environmental and application concerns limiting new applications
Factors Affecting Coating Selection:
- Soil conditions (rocky, wet, contaminated)
- Operating temperature range
- Installation method (open cut, directional drilling, etc.)
- Service environment (pH, stray currents, bacteria)
- Design life expectations
- Available application facilities
WUZHOU’s coating capabilities address these varied requirements: “Our dedicated coating production lines enable us to offer a comprehensive range of protection systems tailored to specific project environments. We work closely with clients to select the optimal coating system based on installation conditions, soil characteristics, and design life requirements.”
Q5: How important is third-party inspection during spiral welded pipe manufacturing?
Answer: Third-party inspection plays a crucial role in quality assurance, particularly for critical applications:
Value of Independent Verification:
- Provides unbiased verification of compliance with specifications
- Confirms proper execution of quality control procedures
- Documents quality at various manufacturing stages
- Reduces risk of accepting non-conforming materials
- Often required by end clients, insurance, or regulatory bodies
Key Inspection Stages:
- Raw Material Verification: Confirms steel grade and properties
- Manufacturing Process: Witnesses critical operations and parameter settings
- Non-Destructive Testing: Verifies execution and interpretation of NDT results
- Mechanical Testing: Witnesses mechanical property testing
- Final Inspection: Comprehensive verification of dimensions, appearance, and documentation
- Loading Supervision: Ensures proper handling and protection during loading
Scope Determination Factors:
- Project criticality and consequence of failure
- Familiarity with the manufacturer’s quality systems
- Past experience with similar materials
- Regulatory or client requirements
- Risk assessment results
WUZHOU regularly accommodates third-party inspection: “We welcome third-party inspectors and provide full access to our manufacturing processes, testing facilities, and quality records. Our transparent quality management system and comprehensive documentation make the inspection process efficient and effective, providing customers with additional confidence in our products.”
Q6: What are the key differences between water, oil, and gas pipeline spiral welded pipe requirements?
Answer: While the basic manufacturing process is similar, each application has specific requirements:
Oil Pipeline Requirements:
- Emphasis on fracture toughness and crack arrest properties
- Stringent requirements for weld quality and NDT
- Usually requires higher grade materials (X52-X70)
- Specific requirements for sour service when H₂S is present
- May require specialized coating for higher operating temperatures
- Rigorous pressure testing and leak detection
Natural Gas Pipeline Requirements:
- Critical focus on fracture control and crack propagation resistance
- Requires specific Charpy impact testing at design temperatures
- Higher emphasis on material cleanliness and inclusion control
- Typically uses X42-X80 grades depending on pressure
- Strict requirements for dimensional tolerances
- Enhanced focus on weld quality and inspection
Water Transmission Pipeline Requirements:
- Focus on internal lining for potable water compatibility
- Corrosion protection for expected service life (50+ years)
- Often requires NSF/ANSI 61 certification for drinking water
- May use lower strength grades (X42-X60) but with tight roundness requirements
- Specialized design for external loads (soil, traffic, etc.)
- Hydrostatic testing focused on leak prevention
Table 12: Application-Specific Requirements Comparison
Requirement Area | Oil Pipelines | Gas Pipelines | Water Pipelines |
---|---|---|---|
Typical Grades | X52-X70 | X42-X80 | X42-X60 |
Critical Properties | Toughness, fatigue resistance | Fracture control, toughness | Corrosion resistance, watertightness |
Coating Focus | Chemical resistance, thermal stability | Mechanical protection, CP compatibility | Long-term corrosion protection, potable water safety |
Testing Emphasis | Weld quality, material properties | Fracture mechanics, toughness | Hydrostatic integrity, lining quality |
Standards | API 5L, ASME B31.4 | API 5L, ASME B31.8 | AWWA C200, NSF/ANSI 61 |
Special Requirements | Sour service testing when applicable | Crack arrest verification | Potable water certification |
WUZHOU’s versatile production capabilities address all these applications: “Our manufacturing processes are qualified to meet the specific requirements of oil, gas, and water transmission applications. We maintain separate quality procedures for each industry to ensure compliance with the unique demands of each application type.”
Q7: How can I verify the quality and authenticity of spiral welded pipe test reports?
Answer: Verifying test reports involves several important steps:
Documentation Verification Elements:
- Material Test Report (MTR) Review:
- Check that chemical composition matches specified grade requirements
- Verify mechanical properties meet or exceed specifications
- Confirm heat/lot numbers match between MTR and pipe marking
- Verify testing laboratory accreditation when applicable
- Manufacturing Test Report Verification:
- Confirm all required tests were performed (NDT, hydrostatic, etc.)
- Check acceptance criteria alignment with project specifications
- Verify calibration status of testing equipment
- Confirm qualified personnel performed critical tests
- Authentication Steps:
- Check for proper signatures and authorization
- Verify consistency of documentation formatting
- Contact testing laboratories directly for verification of major projects
- Compare with reference documents from previous orders
- Look for digital security features (QR codes, secure PDFs)
Red Flags That Warrant Further Investigation:
- Properties exactly matching specification minimums across all tests
- Inconsistent reporting formats or data presentation
- Missing test data for required properties
- Unclear traceability between raw material and finished product
- Documentation that appears altered or edited
WUZHOU ensures documentation integrity through comprehensive systems: “We employ a rigorous documentation process with multiple verification steps. Each test report undergoes technical review and authorization before release. For enhanced security and traceability, we offer digital documentation with secure verification features that allow customers to confirm authenticity.”
Q8: What are the most critical quality tests to specify for spiral welded pipes?
Answer: Several key tests are particularly important for verifying spiral welded pipe quality:
Non-Destructive Examination of Welds:
- Ultrasonic Testing (UT): Most effective for detecting lack of fusion, laminations, and internal defects
- Radiographic Testing (RT): Provides visual evidence of weld quality and internal defects
- Magnetic Particle Inspection (MPI): Effective for surface and near-surface defects
- Recommended minimum: 100% UT of weld seam plus targeted RT for critical applications
Mechanical Property Verification:
- Tensile Testing: Confirms yield strength, tensile strength, and elongation
- Charpy V-Notch Impact Testing: Verifies material toughness at design temperature
- Hardness Testing: Ensures material is within acceptable hardness range
- Flattening Test: Verifies weld integrity under severe deformation
- Recommended minimum: Testing from each heat of material plus periodic production testing
Dimensional Inspection:
- Diameter and Roundness: Critical for field fit-up and hydraulic efficiency
- Wall Thickness: Essential for pressure containment and structural integrity
- Straightness: Important for installation and alignment
- End Preparation: Critical for successful field welding
- Recommended minimum: Statistical inspection plan with increased frequency for critical dimensions
Hydrostatic Testing:
- Verifies structural integrity and leak-tightness
- Typically performed at 1.5 times design pressure (minimum)
- Minimum hold time based on applicable standard (typically 10-60 seconds)
- Essential for all pressure-containing applications
Coating and Lining Inspection:
- Holiday Detection: Identifies pinholes and defects in coating
- Adhesion Testing: Verifies coating bond strength
- Thickness Measurement: Ensures specified protection is provided
- Visual Inspection: Identifies surface defects and appearance issues
- Recommended minimum: 100% holiday detection plus statistical sampling for other properties
WUZHOU’s comprehensive testing protocol exceeds industry standards: “Every spiral steel pipe produced by our factory undergoes rigorous quality inspection including water pressure testing, ultrasonic testing, and X-ray testing. We maintain complete testing records and make these available to customers as part of our quality documentation package.”
Q9: What are the advantages of working with a manufacturer like WUZHOU compared to distributors or trading companies?
Answer: Direct manufacturer relationships offer several significant advantages:
Technical Expertise and Support:
- Direct access to production engineers and metallurgists
- Ability to customize specifications for specific applications
- Detailed understanding of manufacturing capabilities and limitations
- Collaborative problem-solving for technical challenges
- Application-specific recommendations based on manufacturing expertise
Quality Control and Traceability:
- Complete visibility into manufacturing processes
- Direct control over quality testing and verification
- Unbroken chain of custody for materials and documentation
- Ability to witness critical manufacturing stages
- Simplified resolution of quality issues
Supply Chain Transparency:
- Clear visibility into production scheduling and capacity
- Accurate lead time information and production updates
- Direct communication regarding material availability
- Streamlined logistics coordination
- Reduced risk of counterfeit or substituted materials
Cost and Value Optimization:
- Elimination of intermediary markups
- Opportunity for value engineering and specification optimization
- Potential for just-in-time manufacturing coordination
- Simplified warranty and claims processing
- Volume-based pricing opportunities
WUZHOU’s integrated manufacturing capabilities exemplify these advantages: “With 3 subsidiaries, 2 factories, 4 production bases, 6 production workshops, 11 spiral pipe production lines, and 2 coating lining production lines, we offer complete control over the entire production process. This integration allows us to provide unmatched quality assurance, production flexibility, and technical support directly to our customers.”
Q10: What recent innovations or advancements should buyers be aware of in spiral welded pipe technology?
Answer: Several important developments are changing the spiral welded pipe landscape:
Advanced Steel Metallurgy:
- Higher strength grades (X80-X120) with improved weldability
- Enhanced low-temperature toughness for arctic applications
- Improved hydrogen-induced cracking resistance for sour service
- Corrosion-resistant alloy cladding for aggressive environments
Manufacturing Process Innovations:
- Improved forming techniques for tighter dimensional control
- Advanced automation in welding parameter control
- Real-time weld monitoring and adaptive control systems
- Enhanced heat treatment methods for optimized properties
Inspection Technology Advancements:
- Phased array ultrasonic testing for superior defect detection
- Automated visual inspection systems with machine learning
- Integrated testing data management for enhanced traceability
- Digital twin technology for production monitoring and quality prediction
Coating and Protection Developments:
- Advanced multi-layer coating systems with enhanced mechanical properties
- Nano-technology additives for improved corrosion resistance
- Self-healing coating technologies for damage resistance
- Environmentally friendly coating options with reduced VOCs
Digital and Documentation Innovations:
- Blockchain-based material traceability systems
- Digital material certification with enhanced security features
- IoT sensors for in-service monitoring and predictive maintenance
- Virtual and augmented reality tools for installation training
WUZHOU remains at the forefront of these innovations: “Our state-of-the-art production facilities incorporate the latest technology advancements, ensuring our products meet evolving industry requirements. We continually invest in research and development to improve manufacturing processes, enhance product performance, and deliver greater value to our customers.”
Conclusion: Making Informed Spiral Welded Pipe Procurement Decisions
The procurement of spiral welded steel pipes represents a significant investment with long-term implications for project success, operational performance, and safety. By understanding and avoiding common procurement mistakes, buyers can make more informed decisions that optimize value beyond initial purchase price.
Key takeaways from this comprehensive guide include:
- Technical specifications must be comprehensive and application-appropriate, addressing all critical performance requirements while avoiding unnecessary over-specification.
- Supplier selection should evaluate manufacturing capabilities, quality systems, and track record rather than focusing primarily on price considerations.
- Quality control requirements and verification methods must be clearly defined to ensure receipt of pipes that meet project specifications and performance expectations.
- Total cost of ownership analysis provides a more accurate value assessment than purchase price alone, accounting for installation, maintenance, and lifecycle performance.
- Logistics planning and supply chain considerations significantly impact project timelines and should be addressed early in the procurement process.
- Strategic supplier relationships deliver substantial value beyond transactional purchasing, including technical expertise, supply assurance, and continuous improvement opportunities.
WUZHOU exemplifies the ideal manufacturing partner for critical spiral welded pipe applications. With comprehensive production facilities, rigorous quality control, international certifications, and customer-focused support, WUZHOU delivers the quality, reliability, and value that sophisticated buyers demand.
“WUZHOU stands for unmatched precision, superior quality, and unwavering trust,” the company’s CEO emphasizes. “Our state-of-the-art production, strict quality control, and dedication to customer satisfaction set the standard in the steel pipe manufacturing industry.”
By implementing the best practices outlined in this guide and partnering with established manufacturers like WUZHOU, procurement professionals can ensure they receive spiral welded pipes that meet performance requirements, enhance project outcomes, and deliver optimal lifecycle value.