Spiral Welded Pipe vs. Straight Seam Welded Pipe: Which One to Choose?
March 19, 2025
Share This Article
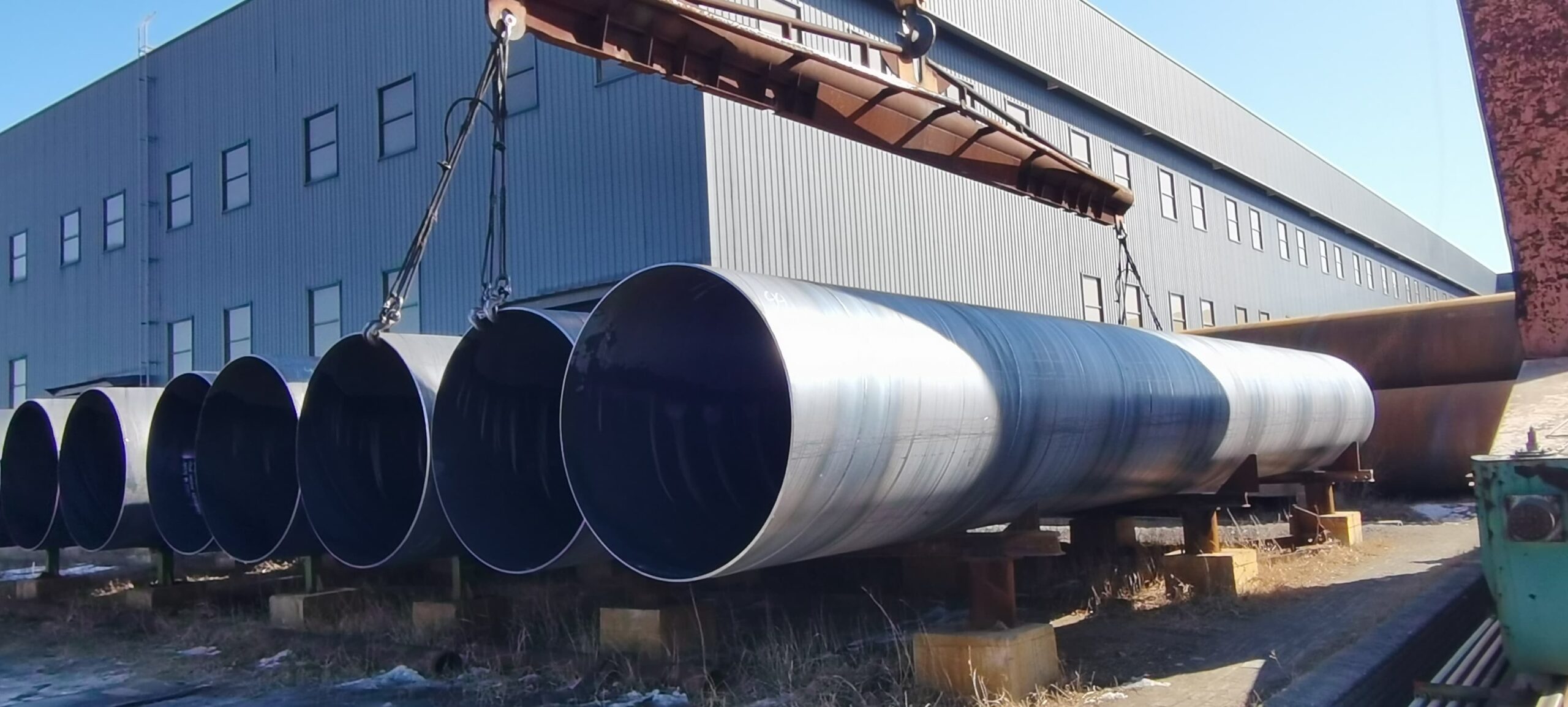
1. Introduction: Understanding Steel Pipe Manufacturing Methods
In the complex landscape of industrial piping systems, wholesale buyers, distributors, and project managers face critical decisions that impact project success, operational efficiency, and long-term cost-effectiveness. Among these decisions, selecting the right type of steel pipe stands paramount. Two major contenders in the steel pipe industry—spiral welded pipes and straight seam welded pipes—offer distinct advantages that must be carefully weighed against specific project requirements.
The global steel pipe market, valued at approximately $156.2 billion in 2022, is projected to reach $215.7 billion by 2030, growing at a CAGR of 4.1%. This growth underscores the increasing demand for high-quality piping solutions across oil and gas, water transmission, construction, and infrastructure development sectors. As industrial requirements become more sophisticated, understanding the nuances between different pipe manufacturing technologies becomes essential for procurement professionals and wholesale buyers.
The Importance of Proper Pipe Selection
Choosing between spiral welded pipe and straight seam welded pipe involves more than just comparing price points. The decision impacts:
- Project Economics: Initial procurement costs, installation expenses, and lifetime maintenance requirements
- Operational Performance: Pressure handling capabilities, flow efficiency, and resistance to various stresses
- Installation Logistics: Transportation challenges, on-site handling, and welding requirements
- Longevity and Maintenance: Corrosion resistance, fatigue performance, and long-term reliability
- Compliance Standards: Meeting industry-specific regulations and international quality benchmarks
For wholesale buyers and distributors looking to supply reliable piping solutions to end-users, understanding these differences provides a competitive edge. Making informed recommendations based on technical merit rather than just availability can strengthen business relationships and establish your position as a value-adding supply partner.
Critical Factors Driving Pipe Selection Decisions
Several key factors influence the selection between spiral and straight seam welded pipes:
Factor | Consideration Points |
---|---|
Project Parameters | Diameter requirements, pressure ratings, temperature conditions |
Application Environment | Exposure to corrosive elements, soil conditions, seismic activity |
Budget Constraints | Initial investment capabilities, lifecycle cost priorities |
Installation Conditions | Available equipment, geographical challenges, timeline requirements |
Material Specifications | Steel grade requirements, wall thickness needs, coating specifications |
Regulatory Requirements | Industry standards, regional code compliance, certification needs |
As we explore the characteristics, advantages, and limitations of both spiral welded and straight seam welded pipes in the following sections, keep these decision drivers in mind. The right choice ultimately depends on a nuanced understanding of how each pipe type’s inherent properties align with your specific project requirements.
2. What is Spiral Welded Pipe? Manufacturing Process & Characteristics
Spiral welded steel pipes represent an innovative approach to pipe manufacturing that offers unique advantages for specific applications. Unlike their straight seam counterparts, spiral welded pipes feature a distinctive helical seam that runs along the pipe’s circumference in a spiral pattern—a manufacturing technique that has revolutionized large-diameter pipe production.
Manufacturing Process of Spiral Welded Pipes
The production of spiral welded pipes involves a sophisticated manufacturing sequence that transforms flat steel coils into robust piping solutions. WUZHOU, as a leading manufacturer with 11 advanced spiral pipe production lines, has perfected this process to ensure exceptional quality control and precision:
- Raw Material Preparation: The process begins with high-quality steel coil selection. WUZHOU ensures rigorous material testing and provides comprehensive raw material reports to guarantee superior quality inputs.
- Coil Edge Preparation: The steel coil edges undergo precise milling to create optimal beveling for welding. This critical step ensures proper joint penetration and weld integrity.
- Forming Process: The steel coil passes through specialized forming machines that gradually bend it into a spiral configuration. The angle at which the steel strip is fed into the forming equipment determines the pipe’s diameter—a remarkable flexibility advantage.
- Double-sided Submerged Arc Welding (DSAW): WUZHOU employs advanced submerged arc welding techniques where both interior and exterior welds are created simultaneously. This process occurs as the formed pipe moves through the production line, with the weld hidden beneath a layer of flux that shields the molten metal from atmospheric contamination.
- Weld Inspection: Every spiral weld undergoes rigorous testing. WUZHOU implements comprehensive quality inspection protocols including ultrasonic testing, X-ray examination, and hydrostatic pressure testing to verify weld integrity.
- Finishing Operations: The pipe then undergoes sizing, straightening, and end facing to achieve precise dimensional specifications.
- Surface Treatment and Coating: Depending on application requirements, pipes receive appropriate surface treatments and protective coatings. WUZHOU maintains dedicated coating and lining production lines to provide comprehensive protection solutions.
This meticulous manufacturing process, combined with WUZHOU’s strict adherence to international standards including API 5L and EU standards, ensures that each spiral welded pipe meets the highest quality benchmarks.
Key Characteristics of Spiral Welded Pipes
Spiral welded pipes offer several distinctive characteristics that make them particularly valuable for specific applications:
1. Structural Properties
- Enhanced Strength Distribution: The helical welding pattern distributes stresses more uniformly around the pipe circumference, particularly beneficial for handling external loads.
- Superior Buckling Resistance: The spiral seam configuration inherently provides better resistance to buckling under external pressures compared to straight seam alternatives.
- Excellent Fracture Resistance: The spiral weld pattern inhibits crack propagation, as any fracture would need to navigate the non-linear weld path.
2. Manufacturing Advantages
- Flexible Diameter Range: Using the same width of steel coil, manufacturers like WUZHOU can produce various pipe diameters by simply adjusting the forming angle—a significant production advantage.
- Efficient Material Utilization: The spiral manufacturing process typically results in less material waste, contributing to more competitive pricing for larger diameter pipes.
- Length Flexibility: Production lines can create virtually any practical length, limited primarily by transportation logistics rather than manufacturing constraints.
3. Performance Characteristics
- Pressure Handling: Properly manufactured spiral welded pipes exhibit excellent pressure containment capabilities, with WUZHOU’s products routinely exceeding industry standard pressure requirements.
- Flow Efficiency: Contrary to common misconceptions, modern spiral welded pipes with properly finished internal surfaces show negligible flow resistance differences compared to straight seam alternatives.
- Fatigue Performance: The spiral weld distribution can provide advantages in applications with cyclic loading conditions.
Typical Specifications and Ranges
WUZHOU’s spiral welded pipe production capabilities exemplify the versatility of this manufacturing approach:
Specification | Range |
---|---|
Diameter Range | 406mm (16″) to 3500mm (138″) |
Wall Thickness | 6mm to 25mm |
Steel Grades | X42, X46, X52, X56, X60, X65, X70, and custom specifications |
Length | Standard 12m or customized lengths up to 18m |
Coating Options | 3PE, FBE, Coal Tar Epoxy, Cement Mortar Lining |
Production Standards | API 5L, ASTM A252, AWWA C200, EN 10217, ISO 3183 |
With an annual production capacity of 400,000 tons across its four production bases and six workshops, WUZHOU has established itself as a reliable supplier of high-quality spiral welded pipes for demanding applications worldwide.
3. What is Straight Seam Welded Pipe? Manufacturing Process & Characteristics
Straight seam welded pipes, also known as longitudinal seam welded pipes, represent one of the most traditional and widely used pipe manufacturing methods in the steel industry. These pipes feature a single longitudinal weld running parallel to the pipe axis, creating a straight line from end to end—a fundamental difference from the helical pattern found in spiral welded alternatives.
Manufacturing Process of Straight Seam Welded Pipes
The production of straight seam welded pipes follows a methodical sequence that transforms flat steel plates or coils into cylindrical piping solutions:
- Raw Material Selection: The process begins with steel plates or coils, with the width of these materials directly determining the circumference (and thus diameter) of the final pipe.
- Edge Preparation: The edges of the steel plate undergo precise machining to create a beveled profile that facilitates proper weld penetration and joint strength.
- Forming Operation: The steel plate passes through a series of forming rolls that gradually bend it into a cylindrical shape. This typically occurs in one of two processes:
- U-O-E Process: For larger diameter pipes, the plate first forms a U-shape, then an O-shape, before being mechanically Expanded to final dimensions.
- Continuous Roll Forming: For smaller diameter pipes, the plate passes through a continuous series of rollers that progressively bend it into a tube.
- Welding Process: Once formed, the edges are brought together and welded using one of several methods:
- Submerged Arc Welding (SAW): Common for larger diameter, thicker-walled pipes
- Electric Resistance Welding (ERW): Typically used for smaller diameter, thinner-walled pipes
- High-Frequency Welding (HFW): A specialized form of ERW used for particular applications
- Weld Inspection: The longitudinal seam undergoes non-destructive testing such as ultrasonic or radiographic inspection to verify weld integrity and identify any defects.
- Sizing and Straightening: The welded pipe passes through sizing rolls that ensure precise dimensional control and straightness.
- End Preparation and Finishing: Pipe ends are precisely trimmed and may receive additional preparations such as beveling for field welding.
- Hydrostatic Testing: Each pipe is pressure tested to verify its structural integrity and ensure it meets specified pressure ratings.
- Coating and Surface Treatments: Depending on application requirements, pipes may receive various protective coatings to enhance corrosion resistance and durability.
Key Characteristics of Straight Seam Welded Pipes
Straight seam welded pipes possess several distinctive characteristics that make them appropriate for specific applications:
1. Structural Properties
- Predictable Stress Distribution: The longitudinal weld creates a symmetrical stress pattern that engineers can readily model and account for in design calculations.
- Uniform Wall Thickness: Straight seam manufacturing typically delivers highly consistent wall thickness around the pipe circumference.
- Defined Weak Point: The longitudinal seam presents a known location for potential failure under extreme conditions, which can be advantageous for predictive engineering and strategic positioning during installation.
2. Manufacturing Considerations
- Diameter Limitations: Each pipe diameter requires specific plate or coil width, creating distinct tooling requirements for different sizes.
- Production Efficiency: For smaller diameters, straight seam manufacturing can offer high production speeds and efficiency.
- Dimensional Control: The manufacturing process allows for precise control of diameter tolerances.
3. Performance Characteristics
- Pressure Rating: Properly manufactured straight seam pipes demonstrate excellent pressure containment capabilities, especially in smaller diameter applications.
- Axial Load Handling: The longitudinal weld orientation aligns well for handling axial loads in certain applications.
- Specialized Application Suitability: The uniform properties make straight seam pipes particularly well-suited for applications requiring predictable mechanical behavior.
Typical Specifications and Ranges
Straight seam welded pipes are available in various specifications to meet diverse industrial requirements:
Specification | Typical Range |
---|---|
Diameter Range | 20mm (3/4″) to 2540mm (100″) |
Wall Thickness | 2mm to 50mm |
Steel Grades | Carbon steel, low-alloy steel, stainless steel grades |
Length | Standard 6m and 12m, with custom options available |
Manufacturing Standards | API 5L, ASTM A53, ASTM A106, EN 10217 |
Welding Methods | ERW, HFW, SAW, DSAW |
While straight seam welded pipes have traditionally dominated many sectors of the pipe market, the evolution of spiral welded pipe manufacturing—exemplified by manufacturers like WUZHOU with their advanced production capabilities—has created more nuanced selection considerations for wholesale buyers and project engineers. The growing recognition of spiral welded pipes’ advantages for certain applications has led to their increased adoption, particularly in large-diameter transmission systems.
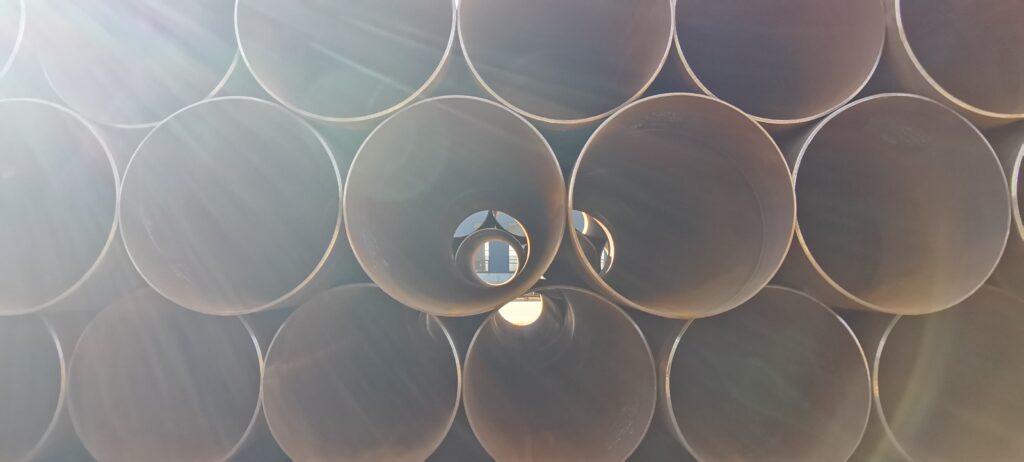
4. Key Differences: Spiral vs. Straight Seam Welded Pipes
When analyzing spiral and straight seam welded pipes for wholesale procurement or project specification, understanding their fundamental differences becomes crucial for making optimal selections. These differences impact not only initial costs but also installation procedures, performance characteristics, and long-term reliability.
Structural Integrity and Strength Characteristics
The fundamental difference in weld orientation creates distinct structural behaviors:
- Weld Pattern Impact: Spiral welded pipes distribute stress along a helical path, effectively dispersing pressure across a larger area. This can be advantageous in applications with variable ground conditions or external pressure considerations. WUZHOU’s advanced double-sided submerged arc welding technique further enhances this inherent strength advantage through superior weld penetration and consistency.
- Stress Distribution: Under internal pressure, straight seam pipes concentrate stress along the longitudinal weld, while spiral welded pipes distribute it across multiple planes. As a leading manufacturer, WUZHOU ensures their spiral welded pipes capitalize on this natural advantage through precise spiral angle calculations tailored to each application’s pressure requirements.
- Buckling Resistance: Spiral welded pipes generally demonstrate superior resistance to buckling under external loads—a critical consideration for buried pipelines. WUZHOU’s manufacturing processes optimize this characteristic through computer-controlled forming and consistent weld quality verification.
Property | Spiral Welded Pipe | Straight Seam Welded Pipe |
---|---|---|
Stress Distribution | Distributed along helical path | Concentrated along longitudinal line |
Buckling Resistance | Generally superior for large diameters | May require thicker walls for equivalent resistance |
Bending Strength | Good, with stress distributed across multiple planes | Directionally dependent relative to weld position |
Fatigue Resistance | Enhanced for variable load conditions | More predictable under consistent loads |
Manufacturing Considerations and Production Efficiency
The production methodologies for these pipe types present different advantages:
- Raw Material Requirements: Spiral pipes can be produced from narrower steel coils, offering material sourcing flexibility. WUZHOU leverages this advantage by maintaining strategic relationships with premier steel suppliers, ensuring consistent raw material quality while optimizing production costs.
- Diameter Flexibility: A single production line at WUZHOU can produce multiple diameter sizes without major retooling, simply by adjusting the spiral angle. This allows for more responsive production scheduling and can significantly reduce lead times for wholesale buyers with diverse diameter requirements.
- Production Throughput: For larger diameters (typically above 24 inches), spiral welded manufacturing offers efficiency advantages. WUZHOU’s 11 dedicated spiral pipe production lines demonstrate this scale advantage, enabling their annual output capacity of 400,000 tons.
- Quality Control Challenges: The longer weld length in spiral pipes requires sophisticated inspection systems. WUZHOU has invested in advanced ultrasonic, X-ray, and hydrostatic testing facilities to ensure every inch of weld meets rigorous quality standards, providing comprehensive quality inspection reports with each shipment.
Cost Implications for Wholesale Buyers
Understanding the economic factors helps procurement professionals make value-based decisions:
- Material Utilization: Spiral welded pipes typically require less material overlap and can be produced from narrower steel coils, potentially reducing raw material costs—a savings WUZHOU passes on to wholesale customers.
- Production Efficiency: For large diameter applications, the production efficiency of spiral welded pipes often translates to cost advantages. WUZHOU’s economies of scale across their four production bases enable competitive pricing without compromising quality.
- Transportation Logistics: While both pipe types face similar shipping challenges, the ability to produce spiral welded pipes in longer lengths can reduce the number of field welds required—a significant installation cost consideration that WUZHOU’s technical consultants help customers evaluate during the specification process.
- Lifecycle Considerations: When accounting for installation, maintenance, and service life, the initially higher cost of premium spiral welded pipes from manufacturers like WUZHOU often results in lower total ownership costs—an important consideration for long-term infrastructure investments.
5. Comparative Analysis: Strength, Cost, and Application Advantages
To help wholesale buyers and project engineers make informed decisions, this section provides a comprehensive comparison across key performance metrics.
Strength and Performance Comparison
The inherent structural characteristics of each pipe type create distinct performance profiles:
Pressure Handling Capabilities
- Spiral Welded Pipes: The helical weld pattern effectively distributes hoop stress, allowing WUZHOU’s spiral welded pipes to excel in high-pressure applications. Their double-sided submerged arc welding process ensures complete penetration and fusion, maximizing pressure containment capabilities.
- Straight Seam Pipes: While capable of high-pressure applications, straight seam pipes may require thicker walls to achieve equivalent pressure ratings for larger diameters, potentially increasing weight and cost.
Bending and Flexibility Characteristics
- Spiral Welded Pipes: The helical weld orientation provides inherent resistance to both longitudinal and circumferential stresses. WUZHOU engineers their spiral pipes with optimal spiral angles to enhance this natural advantage, making them particularly suitable for areas with soil movement or seismic activity.
- Straight Seam Pipes: These pipes demonstrate predictable behavior under bending forces, but their performance is directionally dependent relative to weld orientation. They may be preferred for applications with predominantly axial loading conditions.
Fatigue and Cyclic Loading Response
- Spiral Welded Pipes: The distributed stress pattern makes WUZHOU’s spiral welded pipes particularly resistant to fatigue under variable loading conditions, such as those experienced in water hammer scenarios or pressure cycling applications.
- Straight Seam Pipes: These pipes exhibit more predictable fatigue behavior, making them suitable for applications with well-defined, consistent loading patterns.
Economic Considerations for Project Planning
For wholesale distributors and project managers, understanding the economic implications is essential for competitive bidding and project budgeting:
Initial Procurement Costs
Diameter Range | Cost-Effective Option | Contributing Factors |
---|---|---|
Small (< 24″) | Typically Straight Seam | Higher production speeds, established manufacturing base |
Medium (24″-48″) | Application Dependent | Consider pressure requirements, installation conditions |
Large (> 48″) | Typically Spiral Welded | Material efficiency, production advantages |
WUZHOU’s manufacturing scale and production efficiency enable competitive pricing across all diameter ranges, with particular advantages in the medium to large diameter segments where spiral welded pipes demonstrate inherent cost efficiencies.
Installation Cost Factors
- Field Welding Requirements: Spiral welded pipes from WUZHOU can be produced in longer lengths, potentially reducing the number of field joints and associated welding costs.
- Handling Equipment: The weight efficiency of spiral welded pipes may reduce heavy equipment requirements during installation, particularly for remote project sites.
- Testing and Commissioning: WUZHOU’s comprehensive factory testing reduces the need for extensive field testing, potentially accelerating project timelines and reducing commissioning costs.
Lifecycle Cost Analysis
When evaluating total cost of ownership, several factors favor high-quality spiral welded pipes like those manufactured by WUZHOU:
- Maintenance Requirements: The superior corrosion resistance provided by WUZHOU’s advanced coating options extends service life and reduces maintenance frequency.
- Service Life Expectations: Premium spiral welded pipes with proper coating systems regularly achieve 50+ year service lives in appropriate applications.
- Replacement Economics: The higher initial quality of WUZHOU pipes translates to longer replacement intervals, reducing the annualized cost of infrastructure.
Application-Specific Suitability Analysis
Different operating environments and service requirements may favor one pipe type over another:
Oil and Gas Transportation
- High-Pressure Transmission: WUZHOU’s spiral welded pipes excel in high-pressure oil and gas transmission due to their superior pressure containment characteristics and API 5L certification.
- Gathering Systems: Straight seam pipes may be preferred for smaller diameter gathering lines where their standardized dimensions integrate well with conventional fittings.
- Offshore Applications: The enhanced buckling resistance of WUZHOU’s spiral welded pipes makes them ideal for challenging offshore environments subject to external pressures.
Water Infrastructure Projects
- Large Diameter Transmission: Spiral welded pipes from WUZHOU offer cost and performance advantages for major water transmission projects, with their cement mortar lining options providing excellent flow characteristics.
- Distribution Networks: Straight seam pipes typically dominate smaller diameter distribution applications, though WUZHOU’s spiral options remain competitive even in these segments.
- Penstocks and Hydropower: The pressure cycling resistance of spiral welded pipes makes them ideal for hydroelectric applications, an area where WUZHOU has delivered numerous successful projects.
Construction and Structural Applications
- Piling and Foundation: WUZHOU’s spiral welded pipes demonstrate excellent compression strength for pile applications, with their manufacturing process allowing for cost-effective production of the large diameters typically required.
- Bridge Supports: The consistent dimensional control and structural integrity of both pipe types make them suitable for bridge support applications, with selection often depending on diameter requirements.
- Building Columns: Straight seam pipes have traditionally dominated smaller diameter structural applications, though WUZHOU’s spiral welded options provide compelling alternatives for larger structural elements.
6. Industry-Specific Applications: When to Choose Each Type
Different industries have developed preferences based on historical performance and specific operating requirements. Understanding these industry-specific considerations helps wholesale buyers provide more targeted recommendations to their customers.
Oil and Gas Industry Applications
The demanding requirements of oil and gas transportation have made this industry particularly discerning in pipe selection:
Transmission Pipelines
- Spiral Welded Advantage: For long-distance, large-diameter transmission lines, WUZHOU’s spiral welded pipes offer several compelling advantages:
- Cost-effective production in large diameters
- Superior resistance to buckling under burial loads
- Excellent fatigue resistance for pressure cycling scenarios
- API 5L certification ensuring compliance with stringent industry standards
- Application Examples: Major cross-country transmission systems, export pipelines from production facilities, and trunk lines connecting processing plants have successfully utilized WUZHOU’s spiral welded pipes, with their ISO 9001 quality management system ensuring consistent performance.
Offshore and Challenging Environments
- Selection Considerations: Offshore applications present unique challenges including external pressure, corrosive environments, and installation stresses.
- WUZHOU Solution: Their spiral welded pipes with specialized coatings and enhanced wall thickness calculations provide superior performance in these demanding applications. The company’s ISO 14001 Environmental Management System certification further demonstrates commitment to sustainable production practices important for sensitive marine environments.
Application | Recommended Type | Key Advantages |
---|---|---|
High-Pressure Gas Transmission | WUZHOU Spiral Welded (X65-X70) | Superior pressure containment, cost-effective in large diameters |
Offshore Gathering Systems | WUZHOU Spiral Welded with Specialized Coatings | Enhanced corrosion resistance, buckling performance |
Sour Service Applications | Application-Specific (Material Selection Critical) | Requires specialized metallurgy and welding procedures |
Refined Product Pipelines | Either Type (Based on Diameter/Pressure) | Selection depends on specific project parameters |
Water Infrastructure Projects
Water transmission and management systems represent another major application area with specific requirements:
Large Municipal Water Systems
- Spiral Welded Advantages: WUZHOU’s spiral welded pipes offer particular benefits for municipal water transmission:
- Cost-effective production in the large diameters (48″-138″) often required
- Ability to provide factory-applied cement mortar lining for flow efficiency
- Superior beam strength for spanning uneven terrain or settlement zones
- Extended service life through advanced coating systems
- Case Examples: WUZHOU has supplied spiral welded pipes for numerous municipal water transmission projects, with their comprehensive quality inspection protocols (including hydrostatic testing and ultrasonic examination) ensuring system reliability.
Irrigation and Agricultural Systems
- Selection Factors: Agricultural applications often require balancing cost considerations with performance requirements.
- WUZHOU Approach: Their efficient production processes and material optimization enable competitive pricing without compromising performance, making their spiral welded pipes increasingly popular for large irrigation projects where larger diameters deliver flow efficiency advantages.
Hydropower and Dam Projects
- Critical Requirements: These applications demand exceptional pressure handling, fatigue resistance, and dimensional precision.
- Optimal Solution: WUZHOU’s spiral welded pipes with enhanced wall thickness and specialized coating systems provide the necessary performance characteristics for these demanding applications, supported by comprehensive material and quality inspection reports.
Construction and Infrastructure Development
Beyond fluid transportation, steel pipes play vital roles in structural applications:
Foundation and Piling Applications
- Spiral Welded Advantages: WUZHOU’s spiral welded pipes offer several benefits for foundation work:
- Cost-effective production in larger diameters
- Excellent compression strength for load-bearing applications
- Consistent dimensional control for predictable driving performance
- Ability to customize lengths to project requirements
- Implementation Examples: Major infrastructure projects, including bridges, commercial buildings, and port facilities, have utilized WUZHOU spiral welded pipes for pile foundations, benefiting from their structural integrity and cost efficiency.
Structural Columns and Support Elements
- Selection Considerations: Building structural applications require precise dimensional control and certified mechanical properties.
- Application-Specific Recommendations: While straight seam pipes traditionally dominated smaller structural applications, WUZHOU’s spiral welded pipes have gained acceptance for larger structural elements where their production efficiencies deliver cost advantages without compromising structural integrity.
This industry-specific analysis demonstrates that while certain applications have historical preferences, the continued advancement of spiral welded pipe manufacturing—exemplified by WUZHOU’s state-of-the-art production facilities and rigorous quality control—has expanded their suitability across virtually all application categories, particularly in larger diameters where their inherent advantages are most pronounced.
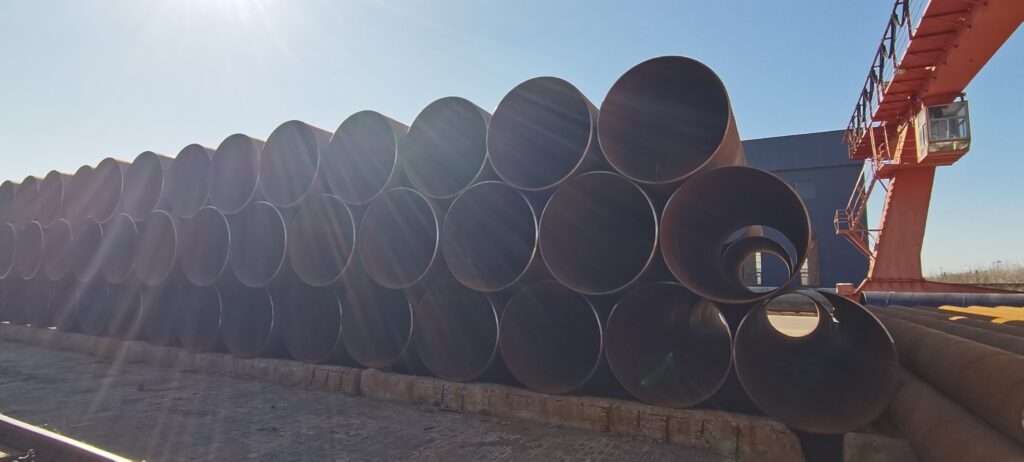
7. Quality Considerations: What Wholesale Buyers Should Look For
For wholesale buyers and distributors sourcing steel pipes, understanding quality indicators is essential for ensuring that the products they supply meet end-user expectations and project specifications. Quality considerations extend beyond basic dimensional compliance to encompass manufacturing processes, material properties, testing protocols, and certification standards.
Critical Quality Indicators in Steel Pipe Selection
When evaluating potential pipe suppliers, wholesale buyers should focus on several key quality indicators:
1. Raw Material Integrity
The foundation of pipe quality begins with raw material selection and verification:
- Steel Grade Certification: Reputable manufacturers like WUZHOU provide comprehensive material certifications documenting the chemical composition and mechanical properties of steel used in pipe production. Their raw material reports verify compliance with specified steel grades such as X42, X52, X65, or X70.
- Coil/Plate Quality Control: Superior manufacturers implement rigorous inspection of incoming steel, checking for surface defects, thickness consistency, and mechanical properties before production begins.
- Traceability Systems: WUZHOU maintains complete traceability from raw material to finished product, allowing wholesale buyers to verify material provenance and quality parameters throughout the production chain.
2. Manufacturing Process Controls
The production process significantly impacts final pipe quality:
- Forming Precision: Accurate forming ensures dimensional consistency and minimizes residual stresses. WUZHOU’s computer-controlled forming processes maintain tight tolerances throughout production.
- Welding Parameter Monitoring: Advanced manufacturers continuously monitor critical welding parameters including current, voltage, travel speed, and heat input. WUZHOU’s automated welding systems maintain these parameters within optimal ranges to ensure weld quality.
- Post-Weld Heat Treatment: For higher-grade pipes or specific applications, proper heat treatment is essential for stress relief and achieving desired mechanical properties. WUZHOU’s production facilities include specialized heat treatment capabilities for applications requiring enhanced metallurgical properties.
3. Comprehensive Testing Protocols
Rigorous testing differentiates premium manufacturers from standard producers:
- Non-Destructive Examination (NDE): WUZHOU implements multiple NDE methods including:
- Ultrasonic testing for detecting internal weld discontinuities
- X-ray examination for comprehensive weld evaluation
- Magnetic particle or dye penetrant testing for surface defect detection
- Mechanical Property Verification: Quality-focused manufacturers regularly test mechanical properties including yield strength, tensile strength, and impact toughness. WUZHOU’s in-house testing facilities verify that every production batch meets specified mechanical requirements.
- Hydrostatic Testing: WUZHOU conducts hydrostatic pressure testing on 100% of produced pipes, ensuring leak-tight performance and structural integrity under pressure.
Certification Standards and Compliance Requirements
Understanding relevant standards helps wholesale buyers ensure that sourced pipes meet industry requirements:
International Standards Compliance
Reputable manufacturers maintain certification to multiple international standards:
- API 5L Certification: This American Petroleum Institute standard is critical for oil and gas applications. WUZHOU’s spiral welded pipes are certified to API 5L, ensuring compliance with stringent oil and gas industry requirements.
- ASTM Standards: Including ASTM A252 for piling applications and ASTM A139 for pressure applications.
- AWWA Standards: Particularly AWWA C200 for water transmission applications, establishing requirements for steel water pipe manufacturing.
- ISO Certifications: WUZHOU maintains ISO 9001 quality management and ISO 14001 environmental management certifications, demonstrating commitment to consistent quality and sustainable production practices.
Quality Management Systems
Beyond product standards, comprehensive quality management systems distinguish premium suppliers:
- Documentation Systems: Leading manufacturers maintain extensive documentation of all quality activities, including inspection records, test results, and non-conformance reports.
- Calibration Programs: Regular calibration of measuring and testing equipment ensures accuracy and reliability of quality data.
- Continuous Improvement Processes: WUZHOU implements formal continuous improvement methodologies to systematically enhance production processes and product quality.
Comparative Quality Considerations: Spiral vs. Straight Seam
When specifically comparing quality aspects between spiral and straight seam welded pipes:
Quality Aspect | Spiral Welded Pipe Considerations | Straight Seam Pipe Considerations |
---|---|---|
Weld Length | Longer weld length per unit pipe length requires more comprehensive inspection | Shorter weld length per unit pipe length may simplify inspection |
Weld Stress Distribution | Helical weld pattern distributes stresses across multiple planes | Longitudinal weld concentrates stress along a single line |
Dimensional Control | May have slightly wider tolerances for large diameters | May achieve tighter dimensional tolerances in smaller diameters |
End Preparation | May require more complex end preparation for field welding | Generally simpler end preparation for field connections |
Coating Adherence | Excellent coating performance with proper surface preparation | Similar coating performance with appropriate preparation |
WUZHOU’s Quality Differentiation
As a premier manufacturer of spiral welded steel pipes, WUZHOU differentiates its products through several quality-focused initiatives:
- Integrated Quality Assurance: From raw material selection through final inspection, quality verification occurs at every production stage. Their comprehensive quality inspection reports document all testing performed on each production batch.
- Advanced Testing Technologies: WUZHOU has invested in state-of-the-art testing equipment to detect even minor imperfections that might affect pipe performance, including automated ultrasonic testing systems that examine 100% of weld seams.
- Material Engineering Expertise: Their engineering team works closely with customers to select optimal material specifications for each application, ensuring that pipes not only meet but exceed performance requirements for specific operating conditions.
- Coating Excellence: With dedicated coating production lines, WUZHOU ensures superior corrosion protection through precise application of 3PE, FBE, coal tar epoxy, or cement mortar linings according to project specifications.
For wholesale buyers seeking reliable suppliers of high-quality spiral welded pipes, WUZHOU’s commitment to quality excellence—evidenced by their comprehensive testing protocols, international certifications, and documented quality management systems—provides assurance that pipes will meet the most demanding project requirements.
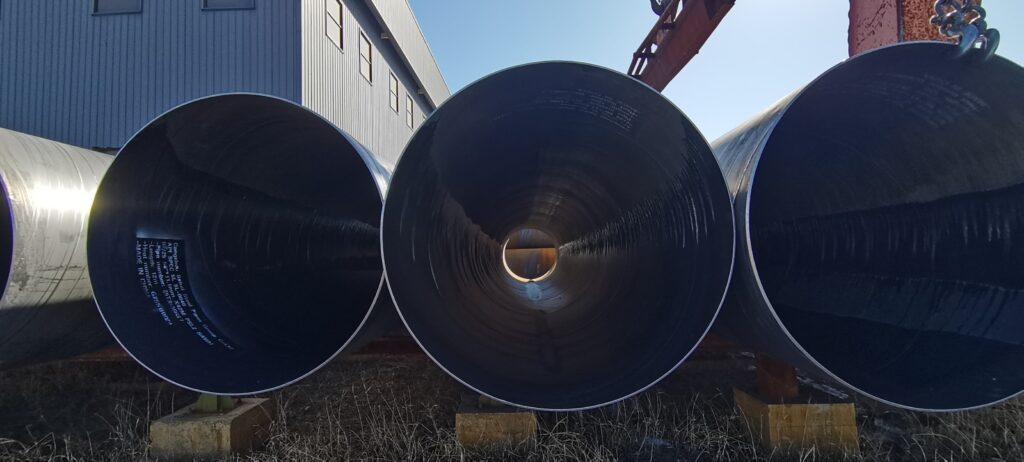
8. WUZHOU: Setting the Standard in Spiral Steel Pipe Manufacturing
When evaluating spiral steel pipe suppliers, wholesale buyers and distributors need partners who combine manufacturing excellence with responsive service and consistent quality. WUZHOU has established itself as an industry leader through continuous investment in manufacturing technology, quality control systems, and customer-focused solutions.
Manufacturing Excellence and Production Capabilities
WUZHOU’s production infrastructure represents one of the industry’s most comprehensive spiral steel pipe manufacturing operations:
Advanced Production Facilities
The company’s manufacturing footprint includes:
- 3 Subsidiaries: Providing integrated operations from raw material processing to finished pipe delivery
- 2 Factories: Housing state-of-the-art production equipment in strategic locations
- 4 Production Bases: Strategically positioned to serve domestic and international markets efficiently
- 6 Production Workshops: Specialized facilities focused on specific aspects of pipe manufacturing
- 11 Spiral Pipe Production Lines: Dedicated to producing pipes across a wide diameter range
- 2 Coating and Lining Production Lines: Ensuring comprehensive corrosion protection solutions
This extensive production infrastructure enables WUZHOU to maintain an annual output of 400,000 tons of spiral welded pipes, ensuring capacity for even the largest project requirements.
Manufacturing Technology Advantages
WUZHOU’s technological advantages include:
- Computer-Controlled Forming: Ensuring precise dimensional control throughout the production process
- Advanced Double-Sided Submerged Arc Welding: Providing superior weld penetration and consistency
- Automated Inspection Systems: Incorporating ultrasonic, radiographic, and hydrostatic testing technologies
- Specialized Coating Applications: Including 3PE, FBE, coal tar epoxy, and cement mortar lining capabilities
These technological investments enable WUZHOU to produce spiral welded pipes that consistently exceed industry standards for dimensional accuracy, weld integrity, and overall performance.
Product Range and Customization Capabilities
WUZHOU’s comprehensive product range addresses diverse industry needs:
Standard Product Specifications
Their standard spiral welded pipe offerings include:
- Diameter Range: 406mm (16″) to 3500mm (138″)
- Wall Thickness: 6mm to 25mm
- Steel Grades: X42, X46, X52, X56, X60, X65, X70, and custom specifications
- Coating Options: 3PE, FBE, coal tar epoxy, cement mortar lining
- Length Options: Standard 12m with custom lengths available
Application-Specific Customization
Beyond standard specifications, WUZHOU provides customized solutions for specialized applications:
- Custom Material Formulations: Working with customers to develop specialized steel formulations for unique operating environments
- Enhanced Corrosion Protection: Tailored coating systems for extreme conditions such as highly corrosive soils or marine environments
- Special End Preparations: Custom beveling and end finishing for specialized connection requirements
- Project-Specific Testing Protocols: Developing enhanced testing methodologies for critical applications
This commitment to customization ensures that wholesale buyers can source exactly the right pipe specifications for their customers’ specialized requirements.
Quality Assurance and Testing Protocols
WUZHOU’s reputation for quality is built on rigorous testing and verification procedures:
Comprehensive Testing Methodology
Each spiral welded pipe undergoes a systematic testing sequence:
- Raw Material Testing: Verification of chemical composition and mechanical properties before production begins
- In-Process Inspection: Continuous monitoring of forming accuracy and welding parameters
- Non-Destructive Examination: 100% of welds undergo ultrasonic testing to detect internal discontinuities
- X-Ray Inspection: Radiographic examination verifies weld integrity throughout the pipe length
- Hydrostatic Testing: Pressure testing confirms structural integrity and leak-tight performance
- Dimensional Verification: Comprehensive measurement ensures compliance with specified tolerances
- Coating Inspection: Verification of coating thickness, adhesion, and holiday detection
This systematic approach ensures that every WUZHOU pipe meets the highest quality standards before shipment.
Documentation and Certification
WUZHOU provides comprehensive documentation with each shipment:
- Material Test Reports: Documenting chemical composition and mechanical properties
- Manufacturing Process Records: Verifying adherence to specified production parameters
- Inspection Certificates: Detailing results of all testing performed
- Compliance Certifications: Confirming adherence to applicable international standards
This detailed documentation gives wholesale buyers complete confidence in the quality and compliance of WUZHOU products.
International Recognition and Industry Leadership
WUZHOU’s commitment to excellence has earned significant industry recognition:
Certifications and Accreditations
The company maintains numerous certifications including:
- API 5L Certification: Confirming compliance with oil and gas industry requirements
- ISO 9001 Certification: Verifying comprehensive quality management systems
- ISO 14001 Certification: Demonstrating commitment to environmental responsibility
- EU Standard Compliance: Enabling access to European markets with full regulatory compliance
Industry Recognition
WUZHOU has received numerous industry accolades, including recognition as a “Top 10 Chinese Brand of Steel Pipe,” acknowledging their leadership in quality, innovation, and customer service.
Customer-Centric Approach and Support Services
Beyond manufacturing excellence, WUZHOU differentiates itself through comprehensive customer support:
Technical Consultation Services
WUZHOU’s engineering team provides valuable expertise to wholesale buyers and end-users:
- Application Engineering: Assistance in selecting optimal pipe specifications for specific projects
- Installation Consultation: Technical guidance on proper handling, installation, and field welding
- Performance Optimization: Recommendations for maximizing service life and operational efficiency
Logistics Support and Global Delivery
With global customers in mind, WUZHOU offers comprehensive logistics solutions:
- Packaging Engineering: Customized packaging designed for specific transportation modes and conditions
- Documentation Assistance: Support with export documentation and compliance requirements
- Delivery Coordination: Working with freight forwarders to ensure timely delivery to project sites worldwide
Long-Term Partnership Approach
WUZHOU focuses on building lasting relationships with wholesale buyers and distributors:
- Product Training: Educating distributor sales teams on technical aspects of spiral welded pipes
- Joint Marketing Initiatives: Supporting distributor marketing efforts with technical content and case studies
- Continuous Communication: Maintaining ongoing dialogue to address evolving market needs
For wholesale buyers seeking a reliable partner in spiral welded steel pipes, WUZHOU offers the ideal combination of manufacturing excellence, quality assurance, and customer-focused service—establishing them as the premier choice for demanding applications worldwide.
9. FAQs: Common Questions About Spiral and Straight Seam Welded Pipes
General Comparison Questions
Q: What is the fundamental difference between spiral welded and straight seam welded pipes?
A: The primary difference lies in the weld seam orientation. Spiral welded pipes feature a helical weld that wraps around the pipe circumference at an angle, while straight seam welded pipes have a longitudinal weld running parallel to the pipe axis. This difference affects stress distribution, manufacturing methods, and certain performance characteristics. WUZHOU specializes in spiral welded pipe manufacturing, utilizing advanced double-sided submerged arc welding technology to optimize the inherent advantages of the spiral welding process.
Q: Which type of welded pipe is stronger—spiral or straight seam?
A: Both pipe types can meet the same strength requirements when properly manufactured. However, they distribute stresses differently. Spiral welded pipes, like those produced by WUZHOU, distribute stresses across multiple planes due to their helical weld pattern, potentially offering advantages in buckling resistance and handling external loads. Straight seam pipes concentrate stresses along the longitudinal weld. The specific application requirements should drive the selection rather than a general strength comparison.
Q: Is there a significant cost difference between spiral and straight seam welded pipes?
A: Cost differences depend primarily on diameter, production volume, and market conditions. For large diameters (typically above 24″), spiral welded pipes often offer cost advantages due to production efficiencies and material utilization. WUZHOU leverages their large-scale production capacity (400,000 tons annually) to provide competitive pricing on spiral welded pipes across a wide diameter range. For smaller diameters, straight seam pipes may be more economical due to higher production speeds.
Technical and Performance Questions
Q: How do spiral welded pipes perform under high pressure compared to straight seam pipes?
A: Both pipe types can be engineered for high-pressure applications. WUZHOU’s spiral welded pipes excel in high-pressure scenarios due to their helical weld pattern, which distributes hoop stress more effectively. Each pipe undergoes rigorous hydrostatic testing to verify pressure containment capabilities. The company’s API 5L certification confirms compliance with oil and gas industry pressure requirements. For specific pressure ratings, the pipe’s wall thickness, material grade, and manufacturing quality are more important factors than weld type.
Q: Do spiral welded pipes have more weld length than straight seam pipes?
A: Yes, spiral welded pipes have a longer weld length per unit pipe length compared to straight seam pipes. However, WUZHOU’s advanced welding technology and 100% weld inspection processes ensure consistent weld quality throughout this longer seam. The distributed stress pattern of the spiral weld often compensates for the increased weld length, particularly in applications with variable or cyclic loading.
Q: Are there differences in field welding procedures between spiral and straight seam pipes?
A: Field welding procedures for joining pipe sections are generally similar for both types, though spiral pipes require attention to the weld intersection at the pipe ends. WUZHOU provides detailed welding procedure recommendations with their pipes and offers technical consultation to ensure proper field joining. Their precise end preparation and dimensional control facilitate efficient field connections.
Application and Selection Questions
Q: For water transmission applications, which type of welded pipe is preferred?
A: Both types are widely used in water transmission, with selection typically based on diameter, pressure requirements, and project economics. For large diameter water transmission lines (typically >48″), WUZHOU’s spiral welded pipes often offer advantages in cost-efficiency and performance. Their cement mortar lining option provides excellent flow characteristics and interior corrosion protection specifically designed for water service. For smaller diameter distribution systems, straight seam pipes have traditionally been more common.
Q: How do spiral and straight seam pipes compare for oil and gas transmission?
A: Both pipe types serve in oil and gas transmission when manufactured to appropriate standards. WUZHOU’s spiral welded pipes, certified to API 5L standards, are increasingly preferred for large diameter transmission lines due to their cost-effectiveness in larger sizes and excellent performance characteristics. Their sophisticated testing protocols, including ultrasonic, X-ray, and hydrostatic testing, ensure these pipes meet the stringent requirements of the oil and gas industry.
Q: Which pipe type performs better in areas with potential ground movement or seismic activity?
A: Spiral welded pipes generally demonstrate advantages in areas with ground movement due to their distributed stress pattern and inherent flexibility. WUZHOU engineers their spiral pipes with optimal spiral angles and material specifications to enhance performance in seismically active regions. Their technical team can provide specific recommendations for challenging installation environments based on soil conditions and seismic risk factors.
Manufacturing and Quality Questions
Q: What quality standards should wholesale buyers look for when sourcing welded steel pipes?
A: Key standards include:
- API 5L for oil and gas applications
- ASTM A252 for piling applications
- AWWA C200 for water transmission
- ISO 9001 for quality management systems
WUZHOU maintains certification to these and other international standards, providing comprehensive quality inspection reports and raw material documentation with every shipment. Wholesale buyers should always request verification of these certifications when sourcing pipes for critical applications.
Q: How can buyers verify the quality of spiral welded pipes?
A: Quality verification should include:
- Review of manufacturer certifications (API, ISO, etc.)
- Examination of material test reports documenting chemical composition and mechanical properties
- Verification of non-destructive examination results (ultrasonic, X-ray testing)
- Review of hydrostatic test records
- Physical inspection of dimensional tolerances and coating quality
WUZHOU provides comprehensive documentation packages with each shipment, including all relevant test reports and certifications to facilitate this verification process.
Q: What are the typical production lead times for spiral welded pipes?
A: Production lead times vary based on quantity, specifications, and current production schedules. WUZHOU’s extensive manufacturing capacity—with 11 spiral pipe production lines across multiple facilities—enables them to offer competitive lead times even for large-volume orders. Their production planning team works closely with wholesale buyers to establish realistic delivery schedules and provides regular progress updates throughout the manufacturing process.
Coating and Corrosion Protection Questions
Q: What coating options are available for spiral welded pipes?
A: WUZHOU offers comprehensive coating solutions including:
- 3-Layer Polyethylene (3PE) for superior corrosion protection
- Fusion Bonded Epoxy (FBE) for high-temperature applications
- Coal Tar Epoxy for buried service
- Cement Mortar Lining for water transmission applications
Their dedicated coating production lines ensure consistent application quality, with each coated pipe undergoing inspection for coating thickness, adhesion, and holiday detection before shipment.
Q: Is there any difference in coating adhesion between spiral and straight seam welded pipes?
A: When properly manufactured, both pipe types can achieve excellent coating adhesion. WUZHOU’s surface preparation processes, including abrasive blasting to a near-white metal finish, ensure optimal coating adhesion regardless of weld pattern. Their quality control processes verify coating adhesion through standardized testing methods, providing consistent performance in corrosive environments.
Q: What is the expected service life of properly coated spiral welded pipes?
A: With appropriate coating systems and installation practices, WUZHOU’s spiral welded pipes regularly achieve service lives exceeding 50 years. Their engineering team works with customers to select optimal coating systems based on soil conditions, operating temperatures, and other environmental factors, maximizing long-term performance and value.
This comprehensive FAQ section addresses the most common questions wholesale buyers and distributors encounter when evaluating spiral and straight seam welded pipe options. WUZHOU’s technical team remains available to address more specific inquiries related to particular applications or specialized requirements.