Understanding Spiral Welded Pipes for Oil & Gas Applications
March 17, 2025
Share This Article
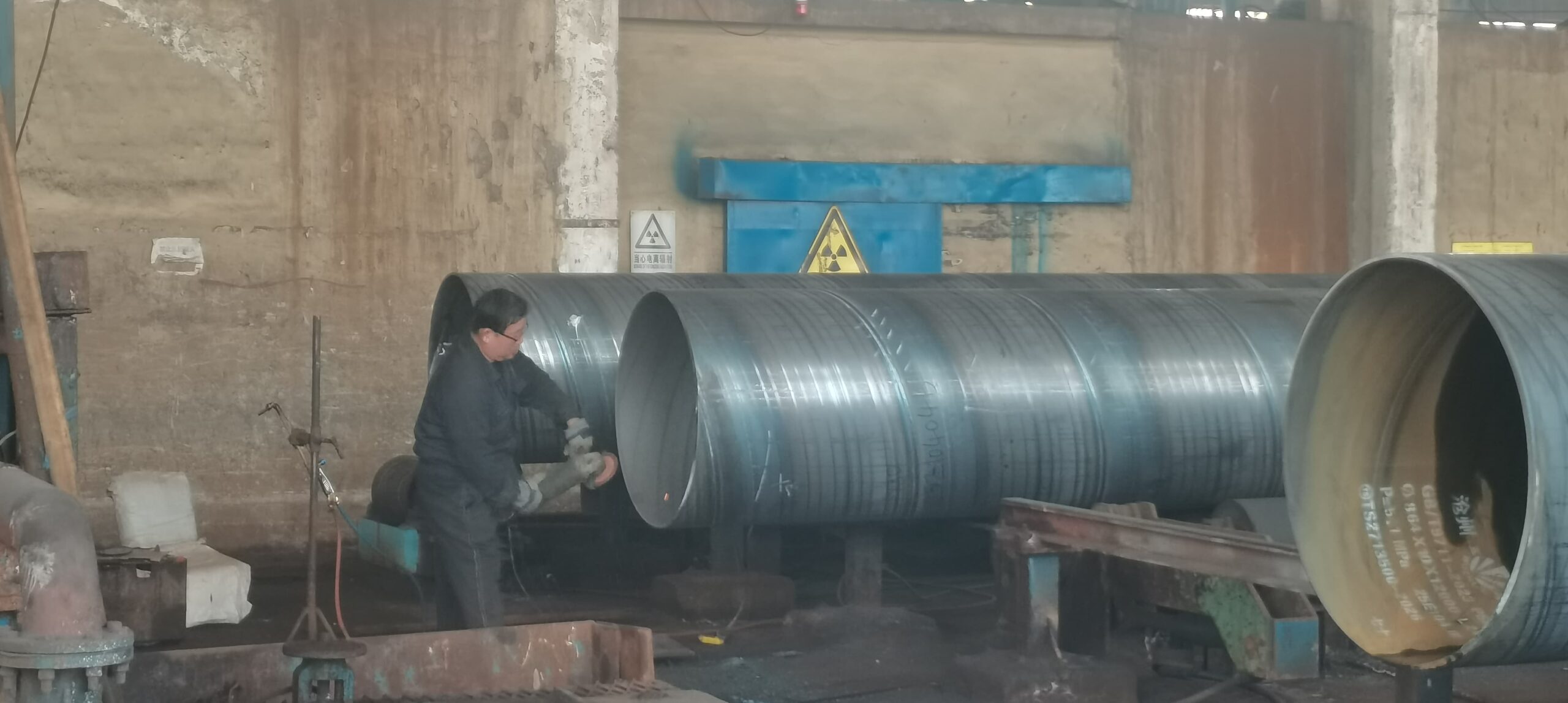
1. Introduction: The Critical Role of Spiral Welded Pipes in Oil & Gas Infrastructure
In the complex and demanding world of oil and gas transportation, the selection of appropriate pipeline materials plays a pivotal role in determining operational efficiency, safety standards, and long-term economic viability. Spiral welded steel pipes have emerged as a preferred solution for large-diameter pipeline systems that form the backbone of global energy infrastructure.
The oil and gas industry faces unique challenges in pipeline construction – from traversing diverse geographical terrains to withstanding extreme pressure conditions and corrosive environments. In this context, spiral welded pipes have gained significant traction among wholesale buyers, engineering procurement contractors (EPCs), and oil & gas companies seeking reliable, cost-effective transmission solutions.
According to recent industry data, the global spiral welded pipe market is projected to reach $40.82 billion by 2028, with the oil and gas sector contributing to approximately 40% of this demand. This growth trajectory underscores the increasing preference for spiral welded pipes in mission-critical applications.
Why Spiral Welded Pipes Matter for Industry Stakeholders:
Stakeholder | Key Concern | How Spiral Welded Pipes Address It |
---|---|---|
Pipeline Operators | Cost-effective transmission with minimal maintenance | High-capacity flow rates with excellent pressure resistance |
Project Engineers | Material reliability across varying conditions | Uniform wall thickness and superior mechanical properties |
Procurement Managers | Value proposition and supply chain reliability | Lower material waste, faster production cycles, competitive pricing |
Safety Compliance Officers | Meeting stringent industry regulations | Manufactured to international standards with comprehensive testing |
Investors | Long-term infrastructure ROI | Extended service life with proper corrosion protection |
Leading manufacturers like WUZHOU have revolutionized the spiral steel pipe production process, implementing advanced technologies and rigorous quality control measures that ensure their products exceed industry expectations. As the flagship brand of Cangzhou Spiral Steel Pipes Group, WUZHOU has established itself as a “Top 10 Chinese Brand of Steel Pipe,” delivering superior products that have been deployed in critical oil and gas projects worldwide.
In this comprehensive guide, we’ll explore why spiral welded pipes have become the preferred choice for oil and gas pipeline infrastructure, the technical considerations in selecting the right specifications, and how partnering with established manufacturers like WUZHOU can provide significant advantages for your next pipeline project.
2. Understanding Spiral Welded Steel Pipes: Manufacturing Process & Technical Specifications
The Evolution of Spiral Pipe Manufacturing
Spiral welded steel pipes represent a significant advancement in pipeline technology, offering distinct advantages over traditional longitudinal seam welded pipes, particularly for large-diameter applications. The manufacturing process has evolved considerably over the past decades, with modern facilities like WUZHOU implementing state-of-the-art production techniques that ensure consistent quality and performance.
Manufacturing Process: The Spiral Submerged Arc Welding (SSAW) Technique
The production of spiral welded pipes involves a sophisticated process that transforms flat steel coils into robust, large-diameter pipes through the following steps:
- Raw Material Selection and Testing: The process begins with the careful selection of high-quality steel coils with precise chemical composition and mechanical properties. Leading manufacturers like WUZHOU provide comprehensive raw material reports to ensure traceability and quality assurance.
- Edge Preparation: The steel coil edges are precisely milled to create the optimal profile for welding, ensuring strong fusion and minimal defects.
- Forming Process: The steel strip is fed through a forming machine at a specific angle, creating a continuous spiral shape that determines the pipe diameter. This spiral forming approach allows for greater flexibility in producing various pipe diameters from the same width of steel coil.
- Welding Operation: The most critical stage involves both internal and external submerged arc welding (SAW) along the spiral seam. This double-sided welding approach creates a strong, continuous joint that meets stringent integrity requirements.
- Internal welding is performed first, applying a uniform weld that penetrates approximately 60-70% of the thickness
- External welding follows, completing the joint with overlap to ensure complete fusion
- Non-Destructive Testing: Each weld undergoes comprehensive non-destructive testing (NDT), including ultrasonic testing (UT), radiographic testing (RT), and hydrostatic pressure testing to verify weld integrity.
- End Facing and Beveling: The pipe ends are precisely cut and beveled to facilitate field welding during pipeline construction.
- Coating Application: Depending on project requirements, various protective coatings may be applied, such as fusion-bonded epoxy (FBE), three-layer polyethylene (3LPE), or concrete weight coating.
Key Technical Specifications for Oil & Gas Applications
The specifications for spiral welded pipes in oil and gas applications are governed by international standards, with API 5L being the predominant specification. WUZHOU’s spiral steel pipes have passed API 5L certification from the American Petroleum Institute along with EU standards, demonstrating their compliance with global requirements.
Standard Dimensions and Grades for Oil & Gas Pipelines:
Parameter | Typical Range for Oil & Gas Applications | WUZHOU Capabilities |
---|---|---|
Diameter | 16″ (406.4mm) to 100″ (2540mm) | Wide range of custom diameters available across 11 production lines |
Wall Thickness | 6mm to 25mm | Precision thickness control with minimal variation |
Steel Grades | API 5L Grades B to X80 | Full range of grades with material certification |
Length | 12m to 18m (standard); custom lengths available | Custom lengths with precise cutting tolerance |
Pressure Rating | Up to 2500 psi depending on grade and thickness | Hydrostatic testing to verify pressure resistance |
Coating Options | FBE, 3LPE, 3LPP, concrete weight coating | Dedicated coating facilities with 2 specialized production lines |
Chemical Composition and Mechanical Properties:
The performance of spiral welded pipes in oil and gas environments depends significantly on their chemical composition and resulting mechanical properties. WUZHOU ensures strict adherence to international standards while offering enhanced properties for challenging applications:
- Carbon Equivalent (CE): Controlled to ensure weldability while maintaining strength
- Yield Strength: From 240 MPa (Grade B) to 555 MPa (X80)
- Tensile Strength: From 415 MPa (Grade B) to 625 MPa (X80)
- Elongation: Minimum 18% to ensure ductility during installation and operation
- Charpy V-Notch Impact Test: Conducted at specified temperatures to verify toughness in various operating environments
With 13 advanced production lines—11 dedicated to spiral steel pipes and 2 for coating and lining—WUZHOU’s manufacturing capabilities ensure not only high-capacity output but also the ability to meet diverse technical specifications with strict quality control measures.
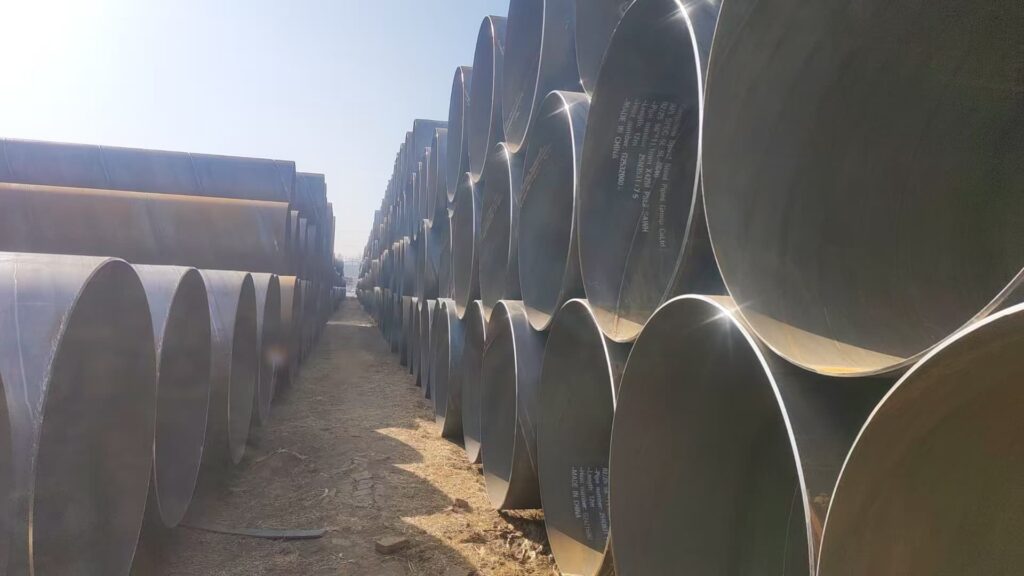
3. Key Advantages of Spiral Welded Pipes for Oil & Gas Transmission
The oil and gas industry demands pipeline solutions that offer reliability, cost-effectiveness, and adaptability to various operational challenges. Spiral welded steel pipes provide several distinct advantages that make them particularly suitable for oil and gas transmission applications:
3.1 Economic Benefits Through Optimized Material Utilization
Cost Efficiency in Raw Materials
Spiral welded pipe manufacturing offers significant economic advantages, making it particularly attractive for large-scale pipeline projects:
- Reduced Material Waste: The spiral manufacturing process typically results in 5-8% less steel usage compared to longitudinal seam welded pipes of equivalent specifications.
- Flexible Diameter Production: One of the most significant advantages is the ability to produce various pipe diameters using the same width of steel coil, simply by adjusting the forming angle. This flexibility allows manufacturers like WUZHOU to offer competitive pricing across a wide range of specifications.
- Coil-Based Production: Using steel coils rather than plates reduces material handling costs and allows for continuous production processes, enhancing manufacturing efficiency.
Comparative Cost Analysis:
Cost Factor | Spiral Welded Pipe | Longitudinal Seam Welded Pipe |
---|---|---|
Raw Material Utilization | 92-95% efficiency | 85-90% efficiency |
Production Speed | Higher throughput for large diameters | Lower throughput for large diameters |
Setup Costs for Diameter Changes | Minimal (adjustment of forming angle) | Significant (potential equipment changes) |
Transportation Efficiency | Optimized length-to-weight ratio | Standard length-to-weight ratio |
Overall Project Cost Impact | 10-15% cost reduction potential for large projects | Baseline comparison |
WUZHOU leverages these economic advantages through its advanced production facilities, passing the cost benefits to wholesale buyers and project developers while maintaining industry-leading quality standards.
3.2 Superior Mechanical Properties for Demanding Conditions
The spiral welding process creates pipes with excellent mechanical characteristics that are particularly beneficial for oil and gas applications:
Enhanced Pressure Resistance
The spiral seam configuration distributes stress more evenly around the pipe circumference compared to longitudinal seams, resulting in:
- Higher burst pressure resistance
- Better performance under fluctuating pressure conditions
- Improved resistance to bending and external loads
Optimized Weld Quality
WUZHOU’s implementation of double-sided submerged arc welding creates welds with:
- Complete penetration across the wall thickness
- Minimal heat-affected zone impact on base material properties
- Uniform weld profile that minimizes stress concentration
- Comprehensive non-destructive testing ensures weld integrity
Field Performance Advantages:
- Seismic Resilience: The spiral structure offers inherent flexibility that performs well in areas prone to seismic activity
- Fatigue Resistance: Better performance under cyclic loading conditions common in pumping operations
- Installation Adaptability: Greater tolerance for field bending within allowable limits
3.3 Technical Advantages for Large-Diameter Pipeline Projects
Large-diameter pipelines present unique challenges that spiral welded pipes are particularly well-suited to address:
Diameter Range Flexibility
WUZHOU’s production capabilities allow for the manufacture of pipes with diameters ranging from standard sizes to custom specifications, accommodating:
- Trunk lines requiring diameters of 24″ to 60″ for maximum flow efficiency
- Gathering systems with varying diameter requirements
- Special applications requiring non-standard dimensions
Hydraulic Efficiency
The internal surface characteristics of properly manufactured spiral welded pipes contribute to hydraulic performance:
- Lower Friction Coefficient: The spiral weld pattern can create a slight helical flow pattern that reduces turbulence in some applications
- Consistent Internal Diameter: Precise manufacturing ensures uniform flow characteristics throughout the pipeline length
- Smooth Weld Transitions: WUZHOU’s quality control processes ensure minimal internal weld reinforcement that could impede flow
Field Joint Considerations
For pipeline construction, field welding of pipe joints is a critical consideration:
- Precision end preparation with customized beveling profiles facilitates high-quality field joints
- Uniform wall thickness around the circumference simplifies alignment during field welding
- Comprehensive documentation of pipe material properties supports development of appropriate welding procedures
Industry Application Matrix:
Oil & Gas Application | Critical Requirements | How Spiral Welded Pipes Deliver |
---|---|---|
Crude Oil Transmission | Pressure integrity, maintenance access | Robust weld quality, longer individual pipe lengths |
Natural Gas Pipelines | Crack propagation resistance, tight tolerances | Spiral seam limits longitudinal crack propagation |
Offshore Gathering Lines | Corrosion resistance, installation efficiency | Compatible with advanced coating systems, optimized weight-to-strength ratio |
Storage Terminal Connections | Dimensional stability, field adaptability | Precise end preparation, consistent ovality control |
Compressor Station Piping | Vibration resistance, pressure cycling | Enhanced fatigue performance of spiral welds |
WUZHOU’s commitment to quality and innovation has positioned their spiral welded pipes as the preferred choice for oil and gas transmission projects worldwide. With an annual output capacity of 400,000 tons distributed across multiple production bases, WUZHOU ensures both production capacity and quality consistency for projects of any scale.
4. Comparative Analysis: Spiral Welded Pipes vs. Alternative Pipeline Solutions
When planning oil and gas pipeline infrastructure, decision-makers must carefully evaluate different pipe manufacturing technologies to determine the most suitable solution for their specific project requirements. This comparative analysis examines how spiral welded pipes compare with the primary alternatives in the market.
4.1 Spiral Welded vs. Longitudinal Seam Welded Pipes
Longitudinal seam welded (LSAW) pipes have traditionally been the standard for critical oil and gas applications, but spiral welded pipes offer compelling advantages in many scenarios:
Manufacturing Process Comparison:
Feature | Spiral Welded (SSAW) | Longitudinal Seam (LSAW) |
---|---|---|
Raw Material | Coiled steel strip | Steel plate |
Welding Configuration | Helical seam at 30-45° angle | Straight longitudinal seam |
Diameter Flexibility | One coil width produces multiple diameters | Each diameter requires specific plate width |
Production Efficiency | Higher for large diameters | Lower for large diameters |
Typical Application Range | 16″ to 100″+ diameter | 16″ to 60″ diameter |
Performance Characteristics:
Strength Distribution:
- SSAW: More uniform stress distribution due to helical weld pattern
- LSAW: Concentrated stress along the longitudinal axis
Material Efficiency:
- SSAW: Typically 5-8% more efficient material utilization
- LSAW: More material waste, especially for large diameters
Pressure Resistance:
- SSAW: Excellent for most pressure ratings up to API 5L X80
- LSAW: Traditional choice for ultra-high pressure applications
Field Join Requirements:
- SSAW: Standard field welding procedures
- LSAW: Similar field welding requirements
Cost Implications:
For large-diameter pipelines (36″ and above), WUZHOU’s spiral welded pipes typically offer cost savings of 10-15% compared to equivalent LSAW pipes without compromising performance or reliability. These savings are particularly significant for large-scale projects where material costs represent a substantial portion of the overall budget.
4.2 Spiral Welded Pipes vs. Seamless Pipes
Seamless pipes are manufactured without welding seams and are often considered for high-pressure, critical applications. However, they come with significant limitations for large-diameter applications:
Capability Comparison:
Aspect | Spiral Welded Pipes | Seamless Pipes |
---|---|---|
Diameter Range | 16″ to 100″+ | Generally limited to 24″ |
Wall Thickness Consistency | Very good, controlled by coil thickness | Excellent, but may vary in very thick walls |
Manufacturing Complexity | Moderate | High |
Production Speed | High | Low for large diameters |
Cost Factor (relative) | 1.0x | 2.5-4.0x for comparable sizes |
Application Suitability:
High-Pressure Transmission:
- Spiral Welded: Suitable for most standard operating pressures with proper design
- Seamless: Traditionally preferred for ultra-high pressure or critical services
Sour Service Applications:
- Spiral Welded: Suitable with appropriate material selection and quality control
- Seamless: Often specified for H₂S service, though modern welded pipes meet requirements
Deep Offshore Applications:
- Spiral Welded: Used successfully in many offshore gathering systems
- Seamless: Often specified for risers and critical subsea applications
WUZHOU’s spiral welded pipes manufactured to API 5L specifications have been successfully deployed in numerous projects where seamless pipes were traditionally specified, providing significant cost savings while meeting all performance requirements.
4.3 Spiral Welded Pipes vs. Reinforced Thermoplastic Pipes (RTP)
For certain low-pressure applications, reinforced thermoplastic pipes have emerged as an alternative to steel pipes:
Comparative Strengths and Limitations:
Consideration | Spiral Welded Steel Pipes | Reinforced Thermoplastic Pipes |
---|---|---|
Pressure Rating | Up to 2500+ psi depending on specifications | Typically limited to 450 psi |
Temperature Tolerance | -45°C to 120°C+ | Usually limited to 65-80°C |
Chemical Resistance | Requires appropriate coating for corrosive environments | Inherently resistant to many chemicals |
Installation Requirements | Welding equipment, heavy lifting capability | Lighter weight, specialized joining methods |
Service Life | 50+ years with proper protection | 20-30 years in optimal conditions |
Initial Cost | Higher material cost | Often lower initial cost |
Lifecycle Cost | Lower maintenance with proper corrosion protection | May require earlier replacement |
Decision Matrix for Pipeline Material Selection:
For oil and gas applications, the following decision matrix helps determine when WUZHOU spiral welded pipes offer the optimal solution:
✓ OPTIMAL CHOICE for spiral welded pipes:
- Large diameter transmission pipelines (24" and above)
- Moderate to high-pressure applications (150-1500 psi)
- Projects where material cost optimization is critical
- Applications requiring standard API 5L grades up to X80
- Situations requiring rapid deployment of large pipe volumes
△ EVALUATE OPTIONS (spiral vs. alternatives):
- Ultra-high pressure applications (1500+ psi)
- Highly sour service with H₂S concentrations above threshold
- Specialized offshore applications
- Very small diameter requirements (below 16")
× TYPICALLY NOT RECOMMENDED for spiral welded pipes:
- Ultra-small diameter applications (below 8")
- Non-standard dimensions outside manufacturing capabilities
- Applications requiring seamless pipe by regulatory mandate
WUZHOU’s engineering team works closely with clients to evaluate specific project requirements and recommend the most appropriate pipe solution, whether spiral welded or an alternative approach, ensuring optimal performance and cost-effectiveness.
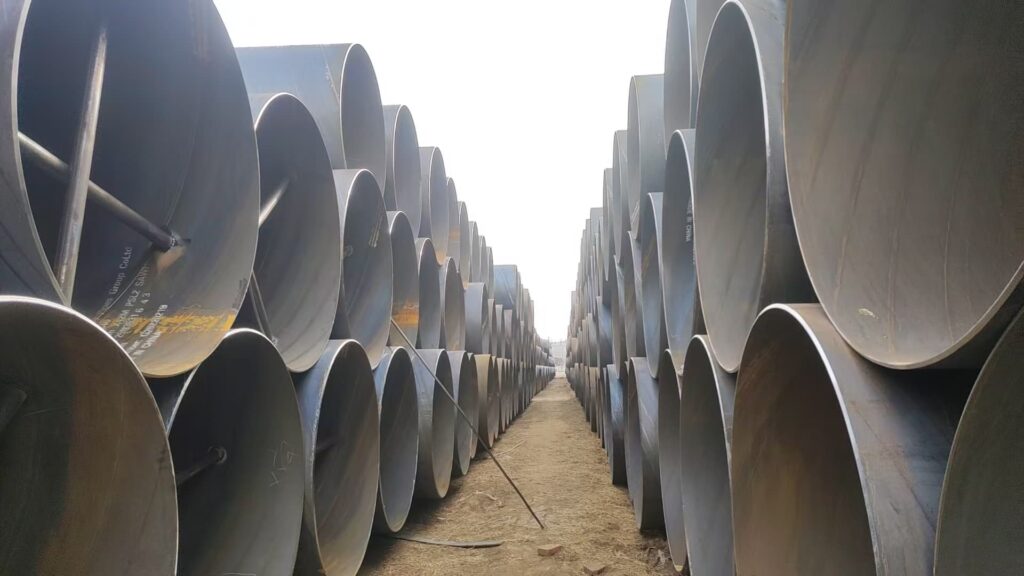
5. Quality Standards and Certifications Essential for Oil & Gas Applications
For oil and gas pipeline applications, adherence to stringent quality standards is non-negotiable. The industry relies on established international standards to ensure pipeline reliability, safety, and longevity. WUZHOU’s commitment to quality is demonstrated through comprehensive certifications and testing protocols.
5.1 International Standards and Specifications
API 5L – Specification for Line Pipe
The American Petroleum Institute’s API 5L specification is the primary standard governing pipes for oil and gas transmission. WUZHOU’s spiral welded pipes are certified to API 5L, covering:
- Material requirements and chemical composition
- Mechanical properties (yield strength, tensile strength, elongation)
- Manufacturing process controls
- Dimensions and tolerances
- Testing requirements
- Marking and documentation
Other Critical Standards Applied by WUZHOU:
Standard | Scope | Significance for Oil & Gas Applications |
---|---|---|
ISO 3183 | Petroleum and natural gas industries – Steel pipe for pipeline transportation systems | Harmonized with API 5L, recognized internationally |
EN 10208 | Steel pipes for pipelines for combustible fluids | European standard for gas transmission |
ASTM A1018 | Steel, Sheet and Strip, Heavy-Thickness Coils | Raw material specification |
NACE MR0175 | Petroleum and natural gas industries – Materials for use in H2S-containing environments | Critical for sour service applications |
DNV-OS-F101 | Submarine Pipeline Systems | Offshore pipeline requirements |
ISO 9001 | Quality management systems | Ensures consistent quality processes |
ISO 14001 | Environmental management systems | Demonstrates environmental responsibility |
WUZHOU’s maintenance of these certifications ensures that their spiral welded pipes meet or exceed all requirements for global oil and gas projects, providing procurement specialists with confidence in product quality and compliance.
5.2 Comprehensive Testing Protocols
Quality assurance in spiral welded pipe manufacturing requires rigorous testing at multiple stages. WUZHOU implements a comprehensive testing regime that exceeds minimum requirements:
Non-Destructive Testing (NDT):
- Ultrasonic Testing (UT): 100% of spiral seam welds are inspected using automated ultrasonic testing to detect internal defects
- Radiographic Testing (RT): Sampling or full inspection of welds using X-ray technology to verify weld integrity
- Magnetic Particle Inspection (MPI): For detection of surface and near-surface defects in ferromagnetic materials
- Hydrostatic Testing: Each pipe undergoes pressure testing at minimum 1.5 times the design pressure to verify integrity
Mechanical and Chemical Testing:
Raw Material Verification:
- Chemical composition analysis of each heat
- Mechanical property testing of base material
Production Testing:
- Tensile testing of base material and weld seams
- Charpy V-Notch impact testing at specified temperatures
- Hardness testing across weld and heat-affected zones
- Flattening tests to verify weld integrity
- Nick-break tests to examine weld fusion
Special Requirements Testing:
- Hydrogen-induced cracking (HIC) tests for sour service
- Sulfide stress cracking (SSC) resistance for H₂S environments
- Fracture toughness testing for crack arrest properties
WUZHOU provides comprehensive raw material reports and quality inspection documentation for every batch of spiral welded pipes, ensuring complete traceability and verification of compliance with project specifications.
5.3 Quality Management Systems and Process Controls
Beyond specific product tests, WUZHOU implements robust quality management systems certified to ISO 9001 standards. These systems encompass:
Material Traceability:
- Complete documentation from raw material to finished product
- Heat number tracking throughout manufacturing process
- Bar coding systems for automatic identification and verification
Manufacturing Process Controls:
- Continuous monitoring of welding parameters
- Automated dimensional measurement and recording
- Statistical process control methods to identify trends and potential issues
- Regular calibration of all measuring and testing equipment
Documentation and Certification:
- Comprehensive manufacturing data records
- Material Test Reports (MTRs) for all products
- Inspection certificates in accordance with EN 10204
- Digital quality management system with secure client access
WUZHOU’s implementation of these comprehensive quality systems has resulted in consistently high acceptance rates and minimal field issues, earning the trust of major oil and gas operators and EPC contractors worldwide.
6. How to Select the Right Spiral Welded Pipe Supplier for Your Project
Choosing the right supplier for spiral welded pipes is critical to project success. This section provides procurement specialists and project engineers with a systematic approach to evaluate and select suppliers that can reliably deliver quality products.
6.1 Key Supplier Evaluation Criteria
When evaluating spiral welded pipe manufacturers for oil and gas applications, consider the following critical factors:
Production Capabilities Assessment:
Capability Factor | Questions to Ask | WUZHOU’s Advantages |
---|---|---|
Manufacturing Scale | What is the annual production capacity? How many production lines are available? | 400,000 tons annual capacity across 11 dedicated spiral pipe production lines |
Size Range Capability | What diameter and wall thickness combinations can be produced? | Wide range of diameters with precise thickness control |
Grade Availability | What API 5L grades can be supplied? Are special grades available? | Full range from Grade B through X80 with special grades upon request |
Coating Facilities | Are coating services available in-house or outsourced? | 2 dedicated coating lines for various coating systems |
Production Flexibility | How quickly can the supplier respond to custom specifications? | Multi-line capability allows for rapid adaptation to customer requirements |
Quality Assurance Credentials:
Certification Requirements:
- Valid API 5L certification with regular audits
- ISO 9001 quality management system certification
- ISO 14001 environmental management system
- Product-specific certifications for special requirements
Testing Capabilities:
- In-house vs. outsourced testing facilities
- Scope of available non-destructive testing equipment
- Laboratory certifications and accreditations
- Testing personnel qualifications and certification
Quality Track Record:
- References from previous oil and gas projects
- Statistical data on acceptance rates
- Field performance history
- Response procedures for non-conformities
WUZHOU’s comprehensive quality management system, certified testing facilities, and proven track record in oil and gas projects worldwide make them a reliable choice for critical pipeline applications.
6.2 Supply Chain Considerations for Pipeline Projects
Pipeline projects often involve complex logistics and strict scheduling requirements. Evaluating a supplier’s ability to manage these challenges is essential:
Logistics and Delivery Capability:
- Production Planning: How does the supplier handle project scheduling and production planning?
- Inventory Management: Does the supplier maintain stocks of common materials to expedite production?
- Transportation Arrangements: What capabilities exist for coordinating shipping and handling of large-diameter pipes?
- Documentation Management: How efficiently can shipping documents and quality certifications be provided?
Project Management Integration:
- Communication Systems: What systems are in place for real-time production updates and reporting?
- Technical Support: Is engineering support available for specification development and technical questions?
- Field Support: Can representatives be deployed to assist with receiving inspection or installation issues?
- Problem Resolution Process: What procedures exist for addressing non-conformities or field issues?
WUZHOU’s integrated project management approach encompasses all these elements, providing clients with comprehensive support from inquiry to installation, ensuring smooth project execution even under challenging timelines.
6.3 Total Cost of Ownership Analysis
While initial price is important, procurement specialists should conduct a total cost of ownership (TCO) analysis when selecting spiral welded pipe suppliers:
Cost Components Beyond Purchase Price:
Cost Element | Considerations | WUZHOU Value Proposition |
---|---|---|
Quality-Related Costs | Inspection requirements, rejection rates, field repair costs | Consistently high first-time acceptance rates reduce inspection and remediation costs |
Delivery Reliability | Schedule impacts, expedition costs, storage costs | Reliable production scheduling reduces need for expediting and interim storage |
Technical Support | Engineering consultation, specification development, field support | Included technical support reduces need for third-party consultants |
Warranty Terms | Coverage scope, response time, remedy options | Comprehensive warranty with clear resolution process |
Life-Cycle Costs | Maintenance requirements, service life expectancy | Superior corrosion protection systems extend service life and reduce maintenance |
Supplier Risk Assessment:
Financial Stability:
- Company history and longevity
- Financial performance indicators
- Capital investment in facilities
Manufacturing Risk:
- Production capacity utilization
- Raw material sourcing strategy
- Equipment maintenance practices
Compliance Risk:
- Regulatory history
- Environmental performance
- Labor practices and standards
Geographic Risk:
- Political stability in manufacturing location
- Natural disaster exposure
- Logistics route reliability
As a leading manufacturer with 3 subsidiaries, 2 factories, 4 production bases, and 6 production workshops, WUZHOU offers a balanced risk profile with redundant production capabilities that ensure supply chain reliability for critical projects.
By systematically evaluating these aspects of potential suppliers, procurement specialists can make informed decisions that balance cost considerations with quality and reliability requirements. WUZHOU’s transparent approach to customer engagement facilitates this evaluation process, providing comprehensive information and demonstrating their capabilities as a premier spiral welded pipe manufacturer for the oil and gas industry.
7. WUZHOU’s Advanced Production Capabilities and Quality Control Measures
WUZHOU has established itself as a leader in the spiral welded pipe industry through continuous investment in advanced production technology and rigorous quality control systems. This section explores the specific capabilities that differentiate WUZHOU in the competitive spiral pipe manufacturing market.
7.1 State-of-the-Art Manufacturing Facilities
WUZHOU’s production infrastructure represents the cutting edge of spiral welded pipe manufacturing technology:
Production Capacity and Infrastructure:
- Scale of Operations: With 11 spiral pipe production lines across 4 production bases, WUZHOU achieves an annual output of 400,000 tons
- Manufacturing Flexibility: Multiple production lines with varying capabilities allow for simultaneous production of different specifications
- Coating Capabilities: 2 dedicated coating and lining production lines deliver complete pipe solutions with protective systems
- Production Efficiency: Advanced automation and process control systems maximize throughput while maintaining quality standards
Technological Advantages:
Forming Systems:
- Computer-controlled forming equipment for precise dimensional control
- Adaptive forming technology that adjusts in real-time to maintain tight tolerances
- Advanced spiral forming machines capable of handling high-strength steel grades
Welding Technology:
- Multi-wire submerged arc welding systems for optimal penetration and fusion
- Automated welding parameter control based on material thickness and grade
- Specialized welding techniques for high-strength materials and sour service applications
Heat Treatment:
- In-line heat treatment capabilities for stress relief
- Specialized equipment for localized heat treatment of weld seams
- Temperature monitoring and control systems for precise thermal management
This advanced manufacturing infrastructure enables WUZHOU to produce spiral welded pipes that consistently exceed industry standards for dimensional accuracy, weld quality, and mechanical properties.
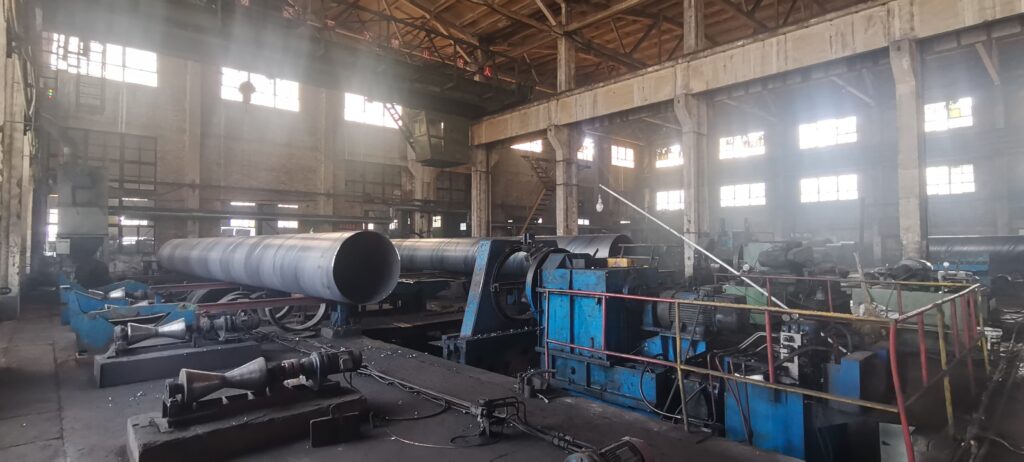
7.2 Comprehensive Quality Control System
WUZHOU’s reputation for exceptional quality is built upon a multi-layered quality control system that encompasses every aspect of the manufacturing process:
Raw Material Quality Assurance:
WUZHOU implements stringent control measures beginning with raw material selection:
- Supplier Qualification Program: Only steel mills meeting WUZHOU’s rigorous standards are approved as suppliers
- Material Verification: 100% inspection of incoming steel coils for dimensional accuracy, surface condition, and mechanical properties
- Chemical Analysis: Verification testing of each heat to confirm compliance with specified grade requirements
- Mechanical Testing: Comprehensive testing of base material properties before production begins
In-Process Quality Controls:
Production Stage | Quality Control Measures | Documentation |
---|---|---|
Edge Preparation | Automated edge milling inspection | Dimensional records |
Forming Process | Continuous monitoring of forming parameters | Process control charts |
Tack Welding | Visual and NDT inspection | Inspection reports |
Internal Welding | Real-time monitoring of welding parameters | Welding parameter logs |
External Welding | Automated visual inspection systems | Weld quality reports |
Heat Treatment | Temperature profile monitoring | Heat treatment records |
Dimensional Inspection | Laser measurement systems | Dimensional reports |
NDT Testing | Automated UT, RT as required | NDT certification |
Hydrostatic Testing | Pressure and hold time verification | Test certificates |
Coating Application | Thickness, adhesion, and holiday testing | Coating inspection reports |
Advanced Testing Capabilities:
WUZHOU’s in-house testing facilities feature state-of-the-art equipment operated by certified personnel:
- Mechanical Testing Laboratory: Equipped for tensile, impact, hardness, and specialized mechanical tests
- Chemical Analysis Laboratory: Capabilities for precise determination of material composition
- Non-Destructive Testing Center: Comprehensive NDT capabilities including automated UT, RT, MT, and PT
- Metallurgical Laboratory: Facilities for microstructure analysis and failure investigation if required
- Corrosion Testing Facilities: Equipment for testing corrosion resistance and suitability for sour service
All testing is performed in accordance with international standards and documented with complete traceability, providing customers with comprehensive quality verification for every pipe produced.
7.3 Engineering Support and Technical Expertise
Beyond manufacturing excellence, WUZHOU provides valuable technical expertise that helps customers optimize their pipeline designs:
Application Engineering Services:
Technical Consultation:
- Specification development assistance based on operating conditions
- Material grade optimization for specific environments
- Wall thickness calculations based on pressure requirements
- Corrosion protection system recommendations
Design Optimization:
- Value engineering to optimize material utilization
- Alternative specifications to improve cost-effectiveness
- Joint design recommendations for field welding
- Transportation and installation considerations
Technical Documentation:
- Comprehensive product data sheets
- Engineering calculations and justifications
- Material compatibility analyses
- Technical presentations and training materials
Research and Development Initiatives:
WUZHOU maintains a forward-looking approach through ongoing R&D programs focused on:
- Development of pipes for increasingly demanding environments
- Improvement of manufacturing processes for enhanced quality and efficiency
- Advanced coating systems for extended service life
- Special applications requiring custom solutions
This commitment to technical leadership ensures that WUZHOU remains at the forefront of spiral welded pipe technology, providing customers with innovative solutions for their most challenging pipeline requirements.
8. Case Studies: Successful Oil & Gas Pipeline Projects Using Spiral Welded Pipes
Examining real-world applications provides valuable insights into the performance and benefits of spiral welded pipes in oil and gas infrastructure. The following case studies highlight successful projects where WUZHOU’s spiral welded pipes delivered exceptional results.
8.1 Case Study: Major Cross-Country Crude Oil Pipeline
Project Overview:
- Location: Central Asia to Eastern China
- Pipeline Length: 1,200 kilometers
- Diameter: 42-inch (1067mm)
- Wall Thickness: 14.3mm to 17.5mm (varying by section)
- Steel Grade: API 5L X70
- Design Pressure: 1,440 psi (10 MPa)
- Coating System: 3-layer polyethylene (3LPE)
Challenges Addressed:
- Diverse terrain including mountain passes and river crossings
- Temperature variations from -30°C to +40°C
- High operating pressure requirements
- Accelerated construction schedule
- Remote installation locations
WUZHOU’s Solution:
WUZHOU manufactured approximately 180,000 tons of spiral welded pipe for this project, delivering pipes with exceptional dimensional consistency and mechanical properties. The manufacturing process included:
- Custom steel formulation with enhanced low-temperature toughness
- 100% ultrasonic testing of all welds with advanced flaw detection capabilities
- Specialized 3LPE coating application optimized for temperature extremes
- Precise end preparation for field welding in challenging conditions
- Comprehensive documentation and traceability systems
Results:
- Zero pipe-related delays during the construction phase
- 99.8% first-time acceptance rate for field joints
- Successful hydrostatic testing of all pipeline sections on first attempt
- Pipeline commissioned on schedule and operating at full capacity
- Five years of operation with zero pipe-related integrity issues
8.2 Case Study: Offshore Gas Gathering System
Project Overview:
- Location: South China Sea
- Water Depth: 50-120 meters
- Pipeline Length: 85 kilometers
- Diameter: 24-inch (610mm)
- Wall Thickness: 15.9mm
- Steel Grade: API 5L X65 with supplementary requirements for offshore service
- Coating System: Fusion-bonded epoxy with concrete weight coating
Challenges Addressed:
- Corrosive marine environment
- Dynamic loading from wave and current action
- Installation by S-lay method requiring specific mechanical properties
- Strict schedule constraints to meet production timeline
- Rigorous quality requirements for subsea application
WUZHOU’s Solution:
WUZHOU supplied approximately 25,000 tons of spiral welded pipe manufactured with specialized properties for offshore installation:
- Enhanced weld quality with 100% UT and 10% RT verification
- Increased wall thickness uniformity for consistent field welding results
- Specialized coating application system for superior adhesion in marine environment
- Concrete weight coating applied with precise thickness control
- Comprehensive quality documentation package for regulatory approval
Results:
- Successful installation with no pipe rejections during laying operations
- Pipeline achieved full pressure test certification on first attempt
- Commissioning completed ahead of schedule
- Three years of continuous operation with excellent flow efficiency
- Integrity monitoring confirms consistent performance meeting design specifications
8.3 Case Study: Sour Gas Transmission Pipeline
Project Overview:
- Location: Middle East
- Pipeline Length: 320 kilometers
- Diameter: 36-inch (914mm)
- Wall Thickness: 12.7mm
- Steel Grade: API 5L X65 with sour service requirements
- H₂S Content: 2.5% in gas stream
- CO₂ Content: 3.8% in gas stream
- Coating System: Dual-layer fusion-bonded epoxy
Challenges Addressed:
- Highly corrosive sour gas environment
- Desert installation with extreme temperature variations
- Stringent material requirements for H₂S resistance
- National energy security implications requiring highest reliability
- Challenging soil conditions with high chloride content
WUZHOU’s Solution:
For this critical application, WUZHOU manufactured pipes with specialized properties to address the corrosive environment:
- Custom steel chemistry with controlled hardness for sour service
- Enhanced manufacturing controls to prevent hardness excursions in heat-affected zones
- 100% UT inspection with additional RT and hardness verification
- Specialized welding procedures qualified for sour service
- Advanced dual-layer FBE coating for superior corrosion protection
Results:
- Pipeline commissioned on schedule with zero material-related delays
- All pipes passed rigorous third-party inspection for sour service
- Successful pressure testing with no leaks or failures
- Four years of operation with corrosion monitoring confirming integrity
- Pipeline maintaining full design capacity with minimal pressure loss
These case studies demonstrate WUZHOU’s capability to deliver high-quality spiral welded pipes for diverse and demanding oil and gas applications. By combining advanced manufacturing technology with rigorous quality control and application-specific engineering, WUZHOU has established a proven track record of success in critical infrastructure projects worldwide.
9. FAQs: Expert Answers to Common Questions About Spiral Welded Pipes
9.1 General Questions About Spiral Welded Pipes
Q: What is the maximum diameter available for spiral welded pipes?
A: WUZHOU can manufacture spiral welded pipes with diameters ranging from 16 inches (406mm) up to 100 inches (2540mm). For oil and gas transmission, the most common diameters range from 24 inches to 60 inches. The spiral welding process actually becomes more cost-effective as diameter increases, making it particularly advantageous for large-diameter applications.
Q: How do spiral welded pipes compare to longitudinal welded pipes in terms of strength?
A: When manufactured to the same quality standards, spiral welded pipes offer comparable strength to longitudinal welded pipes. The spiral weld configuration actually provides some advantages in terms of stress distribution around the circumference. WUZHOU’s spiral welded pipes meet all the same strength requirements specified in API 5L and other international standards as their longitudinal counterparts.
Q: What is the maximum pressure rating for spiral welded pipes?
A: The pressure rating of spiral welded pipes depends on the combination of diameter, wall thickness, and steel grade. WUZHOU’s spiral welded pipes can be designed for pressures exceeding 2500 psi (172 bar) when using high-grade materials and appropriate wall thickness. For most oil and gas transmission applications, WUZHOU pipes are regularly used in the 1000-1500 psi (69-103 bar) range.
Q: Are spiral welded pipes suitable for sour service applications?
A: Yes, WUZHOU manufactures spiral welded pipes specifically designed for sour service applications in accordance with NACE MR0175/ISO 15156 requirements. These pipes are produced with special steel chemistry, controlled manufacturing parameters, and extensive testing to ensure resistance to hydrogen-induced cracking (HIC) and sulfide stress cracking (SSC) in environments containing H₂S.
9.2 Technical Questions on Manufacturing and Quality
Q: How does WUZHOU ensure weld quality in spiral welded pipes?
A: WUZHOU implements a comprehensive quality control system for weld integrity:
- Precise edge preparation of the steel coil before welding
- Continuous monitoring and control of welding parameters
- Double-sided submerged arc welding (internal and external)
- 100% automated ultrasonic testing of all welds
- Additional radiographic testing based on specification requirements
- Hydrostatic testing of each pipe to verify leak-tightness
- Mechanical testing of weld properties including tensile and nick-break tests
This multi-layer approach ensures that all welds meet or exceed the requirements of international standards.
Q: What is the typical length of spiral welded pipes?
A: WUZHOU typically manufactures spiral welded pipes in lengths of 12 meters (40 feet) or 18 meters (60 feet), which optimize transportation efficiency while minimizing the number of field welds required during installation. Custom lengths can be produced to meet specific project requirements, subject to transportation limitations.
Q: How does WUZHOU address ovality concerns in large-diameter pipes?
A: Controlling pipe ovality (out-of-roundness) is crucial for proper field alignment and welding. WUZHOU addresses this through:
- Precise control of the forming process with computer-controlled equipment
- Specialized tooling designed to maintain roundness during production
- Continuous dimensional monitoring throughout manufacturing
- Final sizing operations to ensure compliance with ovality tolerances
- Comprehensive dimensional inspection before shipment
WUZHOU’s pipes consistently meet the stringent ovality requirements specified in API 5L and other international standards.
Q: What coating options are available for spiral welded pipes?
A: WUZHOU offers a complete range of coating systems for corrosion protection and other requirements:
- Fusion-bonded epoxy (FBE) for excellent corrosion protection
- Three-layer polyethylene (3LPE) for superior mechanical protection
- Three-layer polypropylene (3LPP) for high-temperature applications
- Dual-layer fusion-bonded epoxy for enhanced corrosion resistance
- Concrete weight coating for offshore applications
- Internal flow coating for improved hydraulic efficiency
- Custom coating systems for special applications
WUZHOU’s two dedicated coating lines ensure high-quality application and testing of these coating systems.
9.3 Project Implementation and Commercial Questions
Q: What is the typical lead time for spiral welded pipe production?
A: Lead times vary based on quantity, specifications, and current production schedule, but typical ranges are:
- Standard grades and dimensions: 8-12 weeks from order confirmation
- Special grades or requirements: 12-16 weeks from order confirmation
- Large projects with phased delivery: Customized scheduling based on project timeline
WUZHOU’s large production capacity with 11 production lines enables flexible scheduling to accommodate urgent project requirements when necessary.
Q: Does WUZHOU provide technical support for installation contractors?
A: Yes, WUZHOU offers comprehensive technical support throughout the project lifecycle:
- Pre-bid technical consultation on specification optimization
- Submittal of detailed manufacturing and testing plans
- Provision of recommended handling and installation procedures
- Field technical support for receiving inspection and troubleshooting
- Documentation support for quality verification and regulatory compliance
This support ensures smooth project execution and proper handling of WUZHOU’s spiral welded pipes during installation.
Q: How does WUZHOU handle international shipping and logistics?
A: WUZHOU has extensive experience in international logistics for large-diameter pipes:
- Comprehensive export documentation preparation
- Optimization of loading arrangements for shipping efficiency
- Coordination with specialized heavy-lift carriers
- Port handling arrangements and supervision
- Project-specific packaging based on transportation mode and climate
- Real-time shipment tracking and status updates
WUZHOU can provide either FOB or CIF delivery terms based on customer preference and project requirements.
Q: What quality documentation is provided with WUZHOU spiral welded pipes?
A: WUZHOU provides comprehensive quality documentation packages that typically include:
- Material Test Reports (MTRs) for chemical composition and mechanical properties
- Non-destructive testing reports (UT, RT, etc.)
- Hydrostatic test certificates
- Dimensional inspection reports
- Coating inspection reports
- Certificate of compliance with applicable standards
- Mill certificates for raw materials
- Custom documentation as required by project specifications
All documentation is provided in electronic format and can be customized to meet specific project requirements.
Conclusion: Why WUZHOU Spiral Welded Pipes Are the Optimal Choice for Oil & Gas Projects
The selection of appropriate pipeline materials for oil and gas transmission infrastructure has profound implications for project economics, operational reliability, and long-term asset integrity. Through this comprehensive analysis, several key advantages of WUZHOU spiral welded pipes have been demonstrated:
Superior Manufacturing Capabilities:
WUZHOU’s advanced production facilities with 11 spiral pipe production lines and 2 coating lines represent state-of-the-art manufacturing technology. With an annual capacity of 400,000 tons, WUZHOU offers both the scale and flexibility to meet the most demanding project requirements.
Exceptional Quality Assurance:
From raw material selection through final inspection, WUZHOU implements comprehensive quality control measures that exceed industry standards. Certification to API 5L, ISO 9001, ISO 14001, and other international standards confirms WUZHOU’s commitment to quality excellence.
Economic Advantages:
The spiral welding process offers inherent economic benefits through efficient material utilization and production methods. WUZHOU leverages these advantages to provide competitive pricing without compromising quality, enabling significant cost savings for large-scale pipeline projects.
Technical Expertise:
WUZHOU’s engineering team brings extensive application experience to every project, offering valuable technical support from specification development through installation and commissioning. This expertise helps customers optimize their pipeline designs for maximum performance and value.
Proven Performance:
As demonstrated in numerous case studies, WUZHOU spiral welded pipes have a proven track record of excellence in challenging oil and gas applications around the world. From onshore transmission lines to offshore gathering systems, WUZHOU pipes consistently deliver reliable performance.
By choosing WUZHOU as your spiral welded pipe supplier, you gain a trusted partner committed to your project’s success. WUZHOU’s combination of manufacturing excellence, quality focus, and technical support ensures that your oil and gas pipeline infrastructure will deliver reliable, cost-effective performance throughout its service life.
For more information on how WUZHOU spiral welded pipes can benefit your next pipeline project, contact our technical sales team to discuss your specific requirements and discover the WUZHOU advantage in oil and gas transmission infrastructure.