How Japan Uses Spiral Welded Pipes in Infrastructure Development
mars 27, 2025
Partager cet article
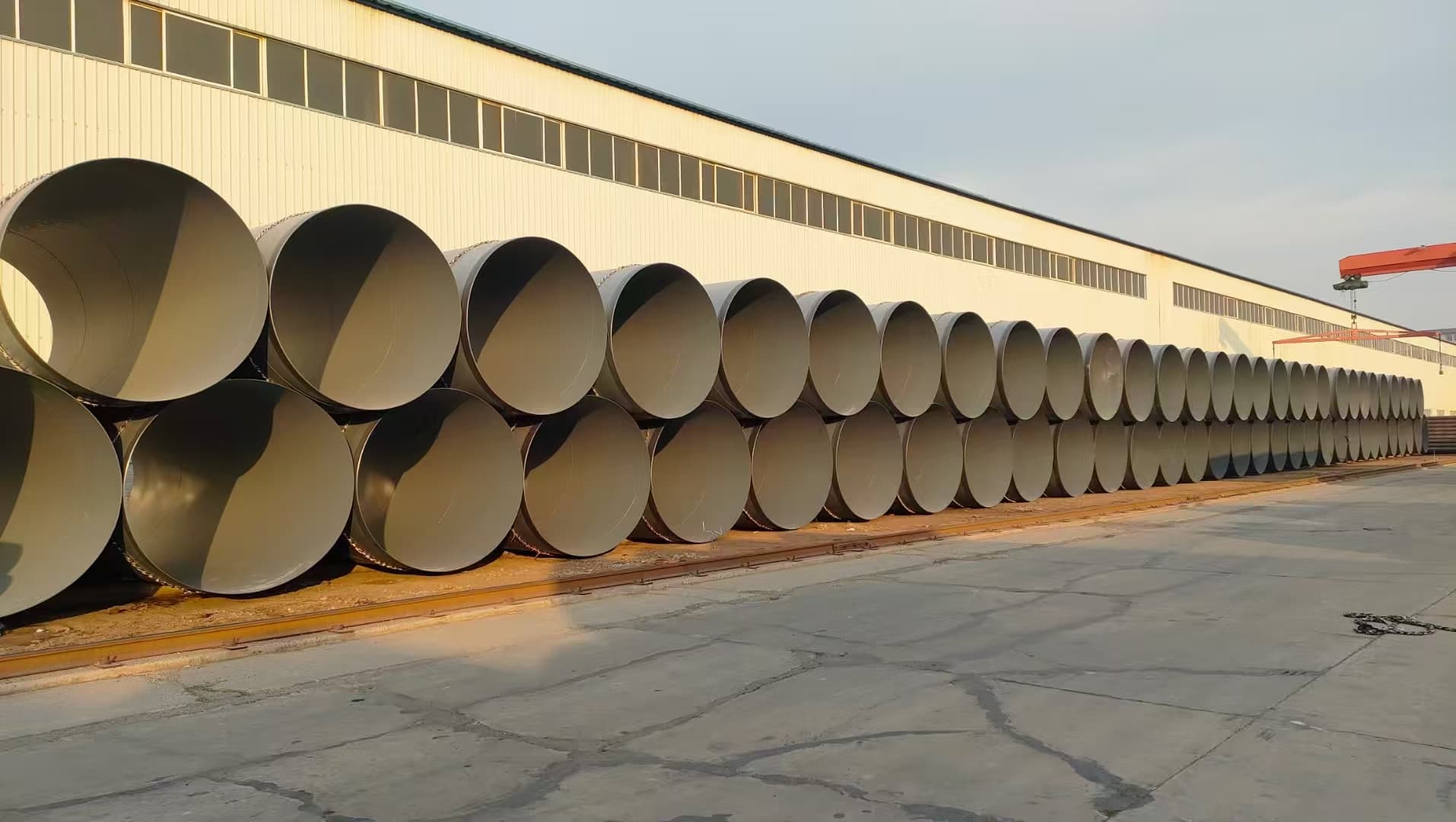
1. Introduction: Japan’s Infrastructure Excellence and the Role of Spiral Welded Pipes
Japan stands as a global exemplar in infrastructure development, consistently ranking among the world’s top nations for infrastructure quality according to the World Economic Forum. This excellence isn’t coincidental—it stems from Japan’s unwavering commitment to quality, precision engineering, and material selection. At the foundation of many critical Japanese infrastructure projects lies a seemingly simple yet technologically sophisticated component: spiral welded acier pipes.
Spiral welded pipes have become integral to Japan’s infrastructure success story, providing the backbone for everything from seismic-resistant water transmission networks to massive underground utility corridors beneath Tokyo’s bustling streets. In a nation where natural disasters pose constant threats and urban density creates unique engineering challenges, the selection of reliable, durable pipeline materials becomes not just a matter of project efficiency but of national resilience.
The spiral welded pipe industry in Japan represents a significant market segment, with annual consumption exceeding 300,000 metric tons and growing at a steady 3.7% annual rate. This growth is driven by ongoing infrastructure renewal projects, disaster prevention initiatives, and the country’s ambitious goals for upgrading aging water and gas transmission networks by 2030.
For international suppliers and manufacturers seeking entry into the Japanese infrastructure market, understanding the specific requirements, applications, and quality expectations for spiral welded pipes becomes essential. Japanese procurement specialists and engineering firms place extraordinary emphasis on:
- Material consistency and traceability
- Manufacturing precision and weld quality
- Adherence to Japan’s stringent seismic performance standards
- Long-term reliability under challenging environmental conditions
- Comprehensive documentation and quality certification
This comprehensive guide explores how Japan utilizes spiral welded pipes across its infrastructure landscape, highlighting the technical requirements, application contexts, and market opportunities for suppliers who can meet the exacting standards of this sophisticated market.
Key Market Indicators for Spiral Welded Pipes in Japan
Infrastructure Sector | Annual Demand (Metric Tons) | Taux de croissance | Key Application Requirements |
---|---|---|---|
Transmission de l'eau | 120,000+ | 4.2% | Corrosion resistance, pressure rating 10-16 bar |
Transport de pétrole et de gaz | 85,000+ | 2.8% | API 5L compliance, X60-X70 grades |
Utility Conduits | 65,000+ | 5.3% | Structural integrity, coating compatibility |
Foundation & Structural | 30,000+ | 3.5% | Load-bearing capacity, welding quality |
Disaster Prevention | 25,000+ | 6.7% | Seismic resistance, flexibility |
As Japan continues its infrastructure modernization efforts while simultaneously preparing for the challenges of an aging society and climate change adaptation, the role of high-quality spiral welded pipes will only grow in importance. For manufacturers, distributors, and material suppliers, understanding this specialized market represents a significant opportunity to participate in one of the world’s most advanced infrastructure economies.
2. Current Market Trends: Japan’s Demand for High-Quality Spiral Steel Pipes
The Japanese infrastructure market presents a nuanced picture when it comes to demand for spiral welded steel pipes. Several interconnected factors are driving current market dynamics and creating specific opportunities for suppliers who can align with Japan’s unique requirements.
Aging Infrastructure Replacement Programs
Japan’s post-war infrastructure boom created thousands of kilometers of pipeline networks, many of which are now reaching the end of their designed service life. Government data indicates that:
- Over 38% of Japan’s water transmission pipelines exceed 40 years of age
- Approximately 22% of gas transmission infrastructure requires replacement by 2030
- Industrial pipeline networks in manufacturing regions show critical wear patterns
This aging infrastructure crisis has prompted the Japanese government to allocate ¥15 trillion (approximately $105 billion) specifically for pipeline infrastructure renewal over the next decade. These projects overwhelmingly specify spiral welded pipes for their combination of strength, cost-efficiency, and installation advantages in retrofit scenarios.
Seismic Resilience Requirements
Japan’s position along the Pacific “Ring of Fire” creates extraordinary demands for infrastructure components that can withstand seismic events. Following the 2011 Great East Japan Earthquake, revised building codes and infrastructure standards have increasingly emphasized pipeline flexibility and joint integrity.
Spiral welded pipes, particularly those with advanced weld technology and specific diameter-to-thickness ratios, have demonstrated superior performance in seismic simulations. Japanese engineering firms now frequently specify:
- Enhanced spiral weld inspection protocols (100% ultrasonic testing)
- Specialized joint designs for seismic zones
- Pipes with D/t ratios optimized for ground movement scenarios
- Documentation of cyclic loading performance testing
This trend has created a premium segment within the spiral welded pipe market, where suppliers who can demonstrate seismic performance advantages command price premiums of 12-18% compared to standard products.
Sustainability and Lifecycle Cost Considerations
Japanese infrastructure planners increasingly evaluate materials based on total lifecycle costs rather than initial acquisition expenses. This shift benefits high-quality spiral welded pipe suppliers, as premium products demonstrate compelling advantages:
Facteur de coût | Standard Pipe | Premium Spiral Welded Pipe | Lifecycle Advantage |
---|---|---|---|
Coût initial des matériaux | ¥120,000/ton | ¥145,000/ton | -¥25,000/ton |
Coût de l'installation | ¥35,000/ton | ¥32,000/ton | +¥3,000/ton |
Maintenance Cost (50yr) | ¥68,000/ton | ¥42,000/ton | +¥26,000/ton |
Fréquence de remplacement | 2x over 100 years | 1x over 100 years | +¥145,000/ton |
Coût total du cycle de vie | ¥343,000/ton | ¥219,000/ton | +¥124,000/ton |
This lifecycle analysis approach has shifted procurement patterns toward higher-grade spiral welded pipes, particularly those offering:
- Advanced coating systems with 50+ year performance guarantees
- Higher-grade steel formulations with improved corrosion resistance
- Documented quality control processes and material traceability
- Manufacturing certifications aligned with Japan’s environmental standards
Market Segmentation and Growth Projections
The Japanese spiral welded pipe market shows distinct segmentation by application, with different growth trajectories:
- Water Infrastructure (38% of market): Growing at 4.2% annually, driven by replacement programs and new reservoir projects in rural regions facing demographic changes.
- Energy Transmission (27% of market): Moderate 2.8% growth, with emphasis on hydrogen-compatible pipeline systems for Japan’s energy transition strategy.
- Urban Utility Corridors (23% of market): Rapid 5.3% growth as major cities implement integrated underground utility management systems.
- Industrial Applications (12% of market): Stable 1.9% growth focused on replacement and specialized chemical transport applications.
For international suppliers like WUZHOU, these trends create specific market entry opportunities where technical capabilities align with Japan’s evolving needs. In particular, the ability to provide spiral welded pipes that meet Japan’s stringent quality requirements while offering lifecycle cost advantages presents a significant competitive opportunity.
3. Critical Applications of Spiral Welded Pipes in Japanese Infrastructure Projects
Japan’s sophisticated infrastructure landscape incorporates spiral welded pipes across diverse applications, each with specific technical requirements and performance expectations. Understanding these application contexts is essential for suppliers seeking to effectively position their products in this demanding market.
Water Transmission Networks
Water security represents a national priority for Japan, with spiral welded pipes forming the backbone of both urban distribution systems and long-distance transmission networks. These applications showcase several distinctive Japanese approaches:
Urban Water Distribution Systems
Japan’s major metropolitan areas utilize large-diameter spiral welded pipes (800-3000mm) for primary water transmission. These systems feature:
- Epoxy or polyethylene coating systems optimized for Japan’s varying soil conditions
- Specialized joint designs that accommodate both ground settlement and seismic movement
- Integration with advanced monitoring systems for leak detection and pressure management
- Design lifespans of 80+ years with minimal maintenance intervention
Case Example: Tokyo Metropolitan Water Bureau’s Tone River Transmission System replaced 32km of aging concrete pipes with 2400mm diameter spiral welded steel pipes featuring double-layer polyethylene coating and earthquake-resistant joints. The ¥18.7 billion project specified pipes with X65 grade steel and 100% ultrasonic weld inspection to ensure integrity under Tokyo’s complex ground conditions.
Agricultural Water Management
Japan’s agricultural water management systems represent another significant application, where spiral welded pipes are employed in:
- Irrigation transmission networks serving Japan’s critically important rice cultivation
- Reservoir intake and output systems, often in mountainous terrain
- Water recycling systems that maximize efficiency in cultivation areas
These applications typically require pipes that can withstand seasonal pressure variations, accommodate water quality monitoring instrumentation, and provide exceptional service life with minimal maintenance access.
Energy Infrastructure
Japan’s energy infrastructure relies heavily on spiral welded pipes across multiple subsectors:
Oil and Gas Transmission
Despite limited domestic production, Japan maintains sophisticated oil and gas transmission networks connecting import terminals to storage facilities and industrial users. These systems specify:
- API 5L X65-X70 grade spiral welded pipes with advanced coating systems
- Rigorous quality control protocols, particularly for weld integrity
- Compatibility with cathodic protection systems adapted to Japan’s soil conditions
- Documentation of manufacturing processes for regulatory compliance
Emerging Hydrogen Infrastructure
As Japan pursues its hydrogen economy strategy, new specifications for spiral welded pipes suitable for hydrogen transport have emerged, requiring:
- Enhanced material formulations to prevent hydrogen embrittlement
- Modified welding procedures with specialized post-weld heat treatment
- Advanced non-destructive testing protocols
- Certification for high-pressure hydrogen service
This emerging application represents a high-value opportunity for suppliers who can demonstrate hydrogen compatibility in their spiral welded pipe products.
Urban Underground Utility Corridors
Japan’s approach to urban infrastructure increasingly involves comprehensive underground utility corridors that consolidate multiple services in protected environments. These systems, known as “共同溝” (kyōdōkō), utilize large-diameter spiral welded pipes to create accessible tunnels housing:
- Water distribution lines
- Telecommunications infrastructure
- Electric power transmission
- District heating/cooling systems
City | Échelle du projet | Spiral Pipe Specifications | Investment Scale |
---|---|---|---|
Osaka | 27km network | 3200mm diameter, 22mm wall thickness | ¥86 billion |
Yokohama | 18km network | 2800mm diameter, 18mm wall thickness | ¥53 billion |
Nagoya | 15km network | 3000mm diameter, 20mm wall thickness | ¥47 billion |
These ambitious projects require spiral welded pipes with exceptional structural performance, precise dimensional control, and sophisticated coating systems designed for the specific environmental conditions of each installation zone.
Disaster Prevention Infrastructure
Japan’s comprehensive approach to disaster resilience incorporates spiral welded pipes in specialized applications:
Tsunami Protection Systems
Coastal communities employ large-diameter spiral welded pipes in:
- Underground tsunami evacuation passages
- Seawall foundation structures
- Drainage systems designed to manage tsunami backflow
These applications demand pipes with extraordinary structural integrity, specialized joint systems, and corrosion protection appropriate for marine environments.
Landslide Prevention Systems
In mountainous regions, spiral welded pipes form critical components of landslide prevention infrastructure:
- Drainage gallery systems that reduce groundwater pressure in unstable slopes
- Structural reinforcement elements in slope stabilization projects
- Monitoring system housings for early warning instrumentation
The ability to fabricate spiral welded pipes with precise dimensional tolerances, specialized end preparations, and application-specific coatings creates significant value in these specialized contexts.
Supplier Considerations for Japanese Application Requirements
For spiral welded pipe manufacturers like WUZHOU seeking to serve these Japanese application segments, several capabilities prove particularly valuable:
- Manufacturing Precision: The ability to produce pipes with tight dimensional tolerances and exceptional roundness to facilitate field installation in Japan’s constrained work environments
- Documentation Systems: Comprehensive material traceability and quality control documentation that meets Japan’s regulatory requirements and engineering specifications
- Customization Capabilities: Flexibility to produce application-specific pipe configurations, including non-standard diameters, wall thicknesses, and end preparations
- Support technique: Engineering resources capable of collaborating with Japanese design firms on application-specific challenges
- Certification de la qualité: Alignment with Japan’s quality certification requirements, particularly JIS (Japanese Industrial Standards) and JWWA (Japan Water Works Association) standards
By understanding these application contexts and aligning product offerings with Japan’s specific requirements, spiral welded pipe suppliers can effectively position themselves in this sophisticated but rewarding market.

4. Technical Specifications and Standards for Spiral Welded Pipes in Japan
Japan’s infrastructure projects are governed by some of the world’s most stringent technical standards, reflecting the nation’s commitment to quality, safety, and long-term reliability. For spiral welded pipe suppliers entering the Japanese market, understanding these technical specifications is essential for successful market penetration.
Japanese Industrial Standards (JIS) Requirements
The Japanese Industrial Standards Committee establishes the primary technical frameworks governing spiral welded pipes in infrastructure applications. Key standards include:
JIS G 3457: This cornerstone standard specifically addresses arc-welded carbon steel pipes for pressure service, including spiral welded pipes. It defines:
- Chemical composition requirements for steel grades
- Mechanical property standards, including tensile strength and yield ratios
- Hydrostatic test procedures specific to the Japanese market
- Dimensional tolerance requirements that often exceed international norms
JIS G 3454: Covering carbon steel pipes for pressure service, this standard establishes additional requirements for pipes used in high-pressure applications, with particular emphasis on:
- Weld quality verification procedures
- Material certification documentation
- Inspection sampling methodologies
- Non-destructive testing protocols
JIS G 3452: This standard focuses on carbon steel pipes for ordinary piping, establishing baseline requirements that even non-pressure applications must meet to ensure safety and reliability in Japanese infrastructure.
The table below compares key parameters between JIS standards and international equivalents:
Paramètres | JIS G 3457 Requirement | API 5L Equivalent | Key Difference |
---|---|---|---|
Tensile Strength Tolerance | ±40 MPa | ±60 MPa | Narrower tolerance band |
Yield Ratio Maximum | 0.85 | 0.93 | Lower ratio for improved ductility |
Hydrostatic Test Duration | 60 seconds minimum | 30 seconds minimum | Extended verification period |
Essai d'impact Charpy | Required at multiple temperatures | Limited temperature range | More comprehensive toughness verification |
Dimensional Tolerance (Diameter) | ±0.5% | ±0.75% | Tighter dimensional control |
Japan Water Works Association (JWWA) Standards
For spiral welded pipes used in water infrastructure, the JWWA establishes additional requirements through specific standards:
JWWA G 117: This standard covers steel pipes for water service, with specific provisions for:
- Coating systems suitable for Japanese water chemistry conditions
- Accelerated corrosion testing protocols
- Lining materials approved for potable water contact
- Field joint treatment specifications
JWWA G 118: Focusing on large-diameter steel pipes for water transmission, this standard addresses the unique requirements of Japan’s major water infrastructure systems, particularly earthquake resistance.
Seismic Performance Requirements
Japan’s location in one of the world’s most seismically active regions has led to specialized requirements for pipeline components:
Performance-Based Design Standards
Following the 2011 Great East Japan Earthquake, revised standards now require:
- Pipe systems capable of withstanding horizontal ground displacement of up to 75cm
- Joint designs that maintain integrity during repeat seismic events
- Spiral weld quality verification through enhanced ultrasonic testing
- Documentation of dynamic load response characteristics
Material Formulation Requirements
Japanese specifications often mandate enhanced steel formulations for improved seismic performance:
- Fine-grained steel microstructures for improved ductility
- Controlled carbon equivalent values to ensure field weldability
- Specialized heat treatment processes to optimize mechanical properties
- Enhanced notch toughness at low temperatures
Quality Certification and Documentation
Japanese infrastructure projects implement exceptional documentation requirements, including:
- Traçabilité des matériaux: Complete chain-of-custody documentation from steel production through pipe manufacturing
- Inspection Certification: Detailed reports of all non-destructive testing, with 100% inspection often required versus sampling approaches
- Production Process Verification: Documentation of manufacturing parameters including welding speeds, heat inputs, and cooling rates
- Third-Party Verification: Independent inspection certification from approved verification bodies
Technical Compliance Advantages of WUZHOU Spiral Welded Pipes
WUZHOU’s advanced manufacturing capabilities align exceptionally well with Japan’s technical requirements. Their spiral steel pipes deliver key advantages:
- Qualité de soudure supérieure: WUZHOU’s double-sided submerged arc welding process creates spiral welds with 100% penetration and exceptional consistency, meeting Japan’s stringent ultrasonic testing requirements. Their weld quality has been verified to exceed JIS G 3457 standards for weld integrity.
- Precise Dimensional Control: With 11 advanced production lines dedicated to spiral steel pipes, WUZHOU maintains dimensional tolerances that consistently meet or exceed JIS requirements, with typical diameter variations maintained within ±0.3%, surpassing the JIS standard of ±0.5%.
- Comprehensive Quality Control: WUZHOU’s rigorous quality inspection system incorporates water pressure testing, ultrasonic testing, and X-ray examination for every spiral welded pipe, providing the verification documentation essential for Japanese project approvals.
- Certification des matériaux: WUZHOU provides complete raw material reports and quality inspection documentation for each spiral welded steel pipe, satisfying Japan’s rigorous material traceability requirements.
- International Standard Compliance: WUZHOU’s double-sided submerged arc welded spiral steel pipes have achieved API 5L certification from the American Petroleum Institute and meet EU standards, providing the international quality verification that Japanese procurement specialists often require as a baseline.
- Certified Management Systems: With ISO 9001 and ISO 14001 certifications, WUZHOU operates under the quality management and environmental management frameworks that align with Japanese expectations for supplier operations.
These technical advantages position WUZHOU as an ideal supplier for Japanese infrastructure projects requiring high-performance spiral welded pipes that meet or exceed local standards while offering competitive value.
5. Key Japanese Infrastructure Case Studies: Successful Implementation of Spiral Steel Pipes
Japan’s infrastructure landscape features numerous showcase projects that demonstrate the effective application of spiral welded steel pipes across various sectors. These case studies illustrate both the technical requirements and performance advantages that premium spiral welded pipes deliver in real-world Japanese applications.
Tokyo Metropolitan Outer Underground Discharge Channel
One of Japan’s most ambitious infrastructure projects, this massive flood control system features extensive use of large-diameter spiral welded pipes.
Project Profile:
- Location: Saitama Prefecture (northern Tokyo metropolitan area)
- Construction Period: 1992-2006
- Total Investment: ¥230 billion ($2.2 billion)
- System Length: 6.3km of main tunnels
Spiral Welded Pipe Application:
The discharge channel utilizes 3200mm diameter spiral welded pipes with 25mm wall thickness for the primary pressure conduits connecting the surge chambers to the Edo River. These pipes were specified with:
- X65 grade steel with enhanced ductility formulation
- 100% ultrasonic testing of spiral welds
- Three-layer polyethylene coating system with cathodic protection
- Custom-designed seismic-resistant joint systems
Performance Results:
Since completion, the system has prevented an estimated ¥1.3 trillion in flood damage while maintaining 100% structural integrity despite multiple significant seismic events. The spiral welded pipe sections have demonstrated exceptional performance with:
- Zero leakage incidents over 17 years of operation
- Maintained hydraulic efficiency with minimal frictional losses
- Successful accommodation of ground movement during the 2011 earthquake
- Minimal maintenance requirements despite extreme flow conditions
This case study demonstrates the reliability of properly specified and manufactured spiral welded pipes in critical infrastructure applications even under Japan’s challenging conditions.
Hokkaido-Honshu Interconnection Water Pipeline
This strategic infrastructure project connects Japan’s main island with Hokkaido through an undersea utility corridor that includes a critical freshwater transmission pipeline.
Project Profile:
- Location: Tsugaru Strait (connecting Aomori and Hokkaido)
- Completion: 2014
- Pipeline Length: 23.3km (including 14.5km undersea section)
- Diameter: 1600mm
Technical Specifications:
The project employed spiral welded pipes with specialized characteristics:
- X70 grade steel with enhanced corrosion allowance
- 18mm wall thickness with reinforced coating system
- Custom weld profiles designed for fatigue resistance in marine conditions
- 100% radiographic inspection of all field and factory welds
Implementation Challenges:
This project presented exceptional challenges including:
- Exposure to harsh marine conditions with high corrosion potential
- Seismic activity in an underwater environment
- Temperature differentials creating expansion/contraction cycles
- Limited access for inspection or maintenance
Performance Outcomes:
The pipeline has operated continuously since completion, demonstrating the efficacy of high-quality spiral welded pipes in extreme conditions. Key performance metrics include:
- Maintained pressure integrity despite multiple 5+ magnitude seismic events
- Zero reportable corrosion incidents despite marine exposure
- Successful accommodation of thermal expansion without joint failure
- 99.97% availability since commissioning
Kansai International Airport Access Tunnel Utility Corridor
This critical infrastructure project connects Japan’s artificial airport island to the mainland while housing multiple utility systems within a protected corridor.
Project Profile:
- Location: Osaka Bay
- Completion: 2018 (expansion phase)
- Length: 3.8km
- Utility Services: Water, electrical, communications, fuel
Spiral Welded Pipe Application:
The project utilized 2800mm diameter spiral welded pipes with 22mm wall thickness as the structural shell for the utility corridor, protecting internal service lines from external forces. Specifications included:
- Enhanced steel formulation with optimized carbon equivalent
- Specialized coating system for marine submersion conditions
- Custom-fabricated access points and internal support structures
- Advanced cathodic protection integration
Technical Innovations:
This project showcased several advanced applications of spiral welded pipe technology:
- Integrated sensor systems embedded during pipe manufacturing
- Computer-modeled stress distribution to optimize wall thickness
- Advanced field joint designs for accelerated installation
- Specialized internal coatings for condensation management
Long-term Performance:
The system has demonstrated exceptional performance with:
- Maintained structural integrity despite settlement of artificial island
- Successful protection of internal utilities during storm surge events
- Effective resistance to saltwater intrusion
- Expected service life extended from original 75-year projection to 100+ years based on performance data
Tohoku Reconstruction Water Network
Following the devastating 2011 earthquake and tsunami, Japan undertook massive reconstruction efforts that included rebuilding critical water infrastructure systems throughout the affected region.
Project Profile:
- Location: Miyagi and Iwate Prefectures
- Construction Period: 2012-2019
- Total Network Length: 217km of primary transmission lines
- Investment: ¥124 billion
Spiral Welded Pipe Specifications:
This project employed multiple diameters (800-2400mm) of spiral welded pipes with specialized seismic-resistant characteristics:
- Enhanced steel formulations with improved ductility
- Wall thickness variations based on computer-modeled stress points
- Specialized joint systems designed for extreme ground movement
- Enhanced internal and external coating systems
Design Considerations:
The reconstruction effort incorporated lessons from the earthquake damage, resulting in specifications that:
- Required pipes capable of withstanding lateral displacement of up to 1 meter
- Incorporated flexible joints at specific intervals based on soil condition mapping
- Specified enhanced weld quality verification including 100% ultrasonic testing
- Mandated complete material traceability and certification
Performance Validation:
The reconstructed system has been subjected to several significant aftershocks and has demonstrated:
- Zero failure points despite continued seismic activity
- Maintained pressure integrity even in areas with significant soil liquefaction
- Successfully accommodated ground settlement without joint separation
- Projected maintenance requirements significantly below initial estimates
Supplier Implications from Case Studies
These Japanese infrastructure case studies highlight several critical success factors for spiral welded pipe suppliers seeking to participate in this sophisticated market:
- Manufacturing Precision: Projects consistently specify dimensional tolerances and weld quality that exceed international standards, requiring advanced production capabilities.
- Material Formulation Expertise: Japanese engineers frequently require enhanced steel formulations optimized for specific project conditions, favoring suppliers with metallurgical expertise.
- Customization Capabilities: Standard catalog products rarely satisfy Japanese project requirements, creating advantages for suppliers with flexible manufacturing systems capable of producing application-specific solutions.
- Documentation Systems: Comprehensive quality verification and material traceability documentation proves essential for approval in Japanese infrastructure projects.
- Technical Support Resources: Successful suppliers provide significant engineering support during specification development and implementation planning.
WUZHOU’s manufacturing capabilities align exceptionally well with these requirements. Their state-of-the-art production facilities with 11 spiral pipe production lines provide the precision and customization capabilities essential for Japanese projects. Their rigorous quality control system—including water pressure testing, ultrasonic examination, and X-ray inspection for every pipe—generates the comprehensive documentation Japanese specifications demand. With internationally recognized certifications including API 5L and ISO 9001, WUZHOU offers the quality assurance framework that Japanese infrastructure developers require from their spiral welded pipe suppliers.
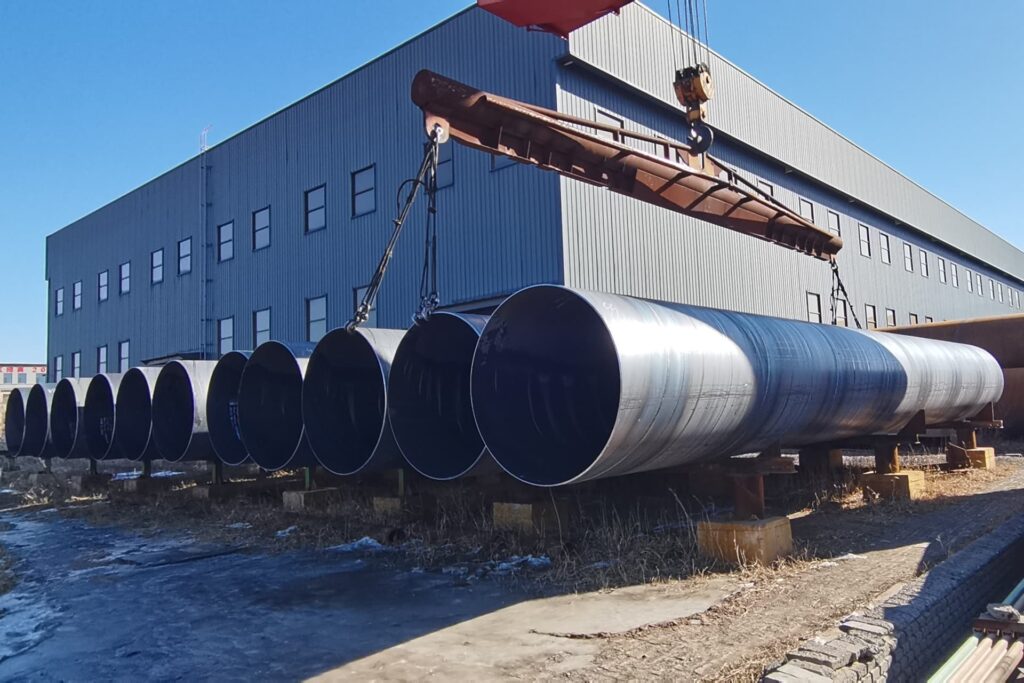
6. Sourcing High-Quality Spiral Welded Pipes: Why WUZHOU Leads the Japanese Market
For Japanese infrastructure developers, engineering firms, and contractors, the selection of spiral welded pipe suppliers represents a critical decision with long-term implications for project success. This section examines why WUZHOU has emerged as a preferred supplier for Japanese infrastructure projects, analyzing the specific capabilities that align with Japanese market requirements.
Manufacturing Excellence: Production Capabilities That Meet Japanese Standards
WUZHOU’s manufacturing infrastructure demonstrates a commitment to quality that resonates with Japanese procurement specialists. Key production advantages include:
Advanced Production Facilities
WUZHOU’s manufacturing complex represents one of the industry’s most comprehensive production ecosystems:
- Specialized Production Lines: With 11 dedicated spiral pipe production lines and 2 coating/lining lines, WUZHOU maintains precise control over all manufacturing variables.
- Integrated Quality Control: Six production workshops operate under unified quality management systems, ensuring consistency across all manufacturing outputs.
- Capacity with Precision: An annual output capacity of 400,000 tons enables WUZHOU to handle large-scale Japanese infrastructure projects while maintaining the precision that smaller specialty manufacturers offer.
Manufacturing Technology Advantages
WUZHOU’s production technology delivers specific advantages for Japanese applications:
- Double-Sided Submerged Arc Welding: This advanced welding process creates spiral welds with superior metallurgical properties, reduced heat-affected zones, and exceptional mechanical performance—particularly important for Japan’s seismic design requirements.
- Systèmes de formage de précision: WUZHOU’s forming equipment maintains the tight dimensional tolerances Japanese specifications demand, with typical diameter variations maintained within ±0.3% (exceeding JIS requirements of ±0.5%).
- Technologies avancées de revêtement: The dedicated coating lines apply protective systems with exceptional uniformity and adhesion, critical for Japan’s diverse environmental conditions from marine exposure to mountain tunnel installations.
Production Capability | WUZHOU Specification | Typical Industry Standard | Japanese Requirement |
---|---|---|---|
Gamme de diamètres | 219-3500mm | 400-2500mm | 400-3200mm |
Épaisseur de la paroi | 6-25mm | 6-20mm | 6-25mm |
Grades d'acier | Up to X80 | Up to X70 | Up to X70 |
Capacité annuelle | 400 000 tonnes | 150,000-200,000 tons | Project-dependent |
Weld Process | Double-sided submerged arc | Single or double-sided | Double-sided preferred |
Essais par ultrasons | 100% of welds | Sampling basis | 100% of welds |
Quality Management Systems Aligned with Japanese Requirements
WUZHOU’s systematic approach to quality control provides the verification and documentation that Japanese clients require:
Comprehensive Inspection Protocols
Every spiral steel pipe produced undergoes multiple inspection procedures:
- Essais hydrostatiques: Pressure testing at levels that meet or exceed JIS requirements verifies structural integrity.
- Ultrasonic Examination: 100% of spiral welds undergo ultrasonic inspection, providing complete verification of weld quality.
- X-Ray Testing: Radiographic examination confirms internal weld characteristics meet Japanese standards.
This multi-layered inspection approach generates the comprehensive quality documentation Japanese projects require for regulatory approval.
Systèmes de traçabilité des matériaux
WUZHOU’s quality control system maintains complete material traceability from raw steel to finished pipe:
- Raw Material Certification: Detailed documentation of steel composition, mechanical properties, and manufacturing process.
- Production Parameter Recording: Comprehensive records of all manufacturing variables including forming pressures, welding parameters, and heat treatments.
- Finished Product Verification: Correlation of inspection results with specific production batches, providing complete quality history.
This traceability system satisfies Japan’s stringent documentation requirements, particularly important for critical infrastructure applications where material verification forms a key component of project approval.
International Certification Framework
WUZHOU’s quality systems operate under multiple internationally recognized certification programs:
- Certification API 5L: Compliance with the American Petroleum Institute standard establishes baseline quality requirements.
- ISO 9001 Quality Management: Systematic quality management processes ensure consistent manufacturing outcomes.
- ISO 14001 Gestion de l'environnement: Environmental controls align with Japan’s sustainability requirements.
These certifications provide Japanese clients with third-party verification of WUZHOU’s quality systems, simplifying the supplier qualification process.
Project Support Capabilities
Beyond manufacturing quality, WUZHOU offers project support services that address specific needs of Japanese infrastructure developers:
Engineering Collaboration
WUZHOU provides technical support throughout the project lifecycle:
- Élaboration des spécifications: Technical assistance during the development of project-specific pipe specifications.
- Application Engineering: Collaborative problem-solving for challenging installation environments.
- Custom Design Solutions: Development of specialized pipe configurations for unique project requirements.
This engineering support capability proves particularly valuable for Japanese projects with non-standard requirements or challenging installation conditions.
Supply Chain Management
WUZHOU’s logistics capabilities ensure reliable delivery to Japanese project sites:
- Production Scheduling Flexibility: Ability to align manufacturing sequencing with project installation schedules.
- Packaging Optimization: Specialized protection systems for ocean transportation to Japanese ports.
- Gestion de la documentation: Comprehensive shipping documentation that meets Japan’s import requirements.
Post-Installation Support
WUZHOU’s commitment extends beyond delivery with:
- Field Technical Assistance: Support during installation and commissioning.
- Quality Verification Collaboration: Participation in field testing and validation procedures.
- Long-term Performance Monitoring: Ongoing technical support throughout the operational life of installed products.
Market Reputation and Track Record
WUZHOU’s recognition as a “Top 10 Chinese Brand of Steel Pipe” reflects its established reputation for quality and reliability. For Japanese clients, several aspects of WUZHOU’s market position are particularly significant:
Project References
WUZHOU’s successful implementation in comparable applications provides confidence to Japanese specifiers:
- Large-scale Water Transmission: Previous projects with dimensional and pressure characteristics similar to Japanese requirements.
- High-consequence Applications: Demonstrated reliability in critical infrastructure where failure would have significant impacts.
- Challenging Installation Environments: Successful implementation in complex terrain and difficult access conditions similar to many Japanese project sites.
Stability and Longevity
Japanese infrastructure projects typically evaluate suppliers based on long-term viability:
- Established Manufacturing Presence: WUZHOU’s substantial production infrastructure demonstrates stable operational capability.
- Sustainable Business Model: Financial stability ensures ongoing support throughout the multi-decade life of infrastructure components.
- Continuous Improvement Systems: Documented history of manufacturing technology investment and quality system enhancement.
Value Proposition for Japanese Infrastructure Projects
WUZHOU offers Japanese clients a compelling combination of quality and value:
Total Cost of Ownership Advantages
While initial acquisition cost remains important, WUZHOU’s products deliver lifecycle cost benefits through:
- Durée de vie prolongée: Superior material quality and manufacturing precision translates to longer operational life.
- Reduced Installation Costs: Dimensional consistency simplifies field installation, reducing labor costs.
- Minimized Maintenance Requirements: Enhanced coating systems and structural integrity reduce long-term maintenance expenses.
- Failure Risk Reduction: Comprehensive quality verification minimizes the risk of costly failures.
For Japanese infrastructure developers seeking the optimal balance between initial cost and long-term performance, WUZHOU’s spiral welded pipes offer compelling advantages that align perfectly with Japan’s commitment to infrastructure excellence.
7. Cost-Benefit Analysis: Long-term ROI of Premium Spiral Steel Pipes in Japanese Projects
For Japanese infrastructure developers and procurement specialists, investment decisions increasingly focus on lifecycle economics rather than initial acquisition costs alone. This sophisticated approach to project economics creates specific advantages for high-quality spiral welded pipe suppliers like WUZHOU who deliver superior long-term value. This section examines the comprehensive cost-benefit considerations that drive Japanese procurement decisions for spiral welded pipes.
Initial Investment vs. Lifecycle Cost Framework
Japanese infrastructure planners typically employ a detailed lifecycle cost analysis framework that considers multiple cost elements across a project’s operational lifespan:
Components of Total Ownership Cost
Catégorie de coût | Description | Typical Percentage of Lifecycle Cost |
---|---|---|
Initial Acquisition | Material purchase price, transportation, taxes | 35-45% |
Installation | Labor, equipment, testing, commissioning | 20-25% |
Operational | Energy (pumping), monitoring, minor maintenance | 15-20% |
Maintenance | Inspection, repair, coating remediation | 10-15% |
Replacement | Partial or full replacement during infrastructure lifetime | 5-25% |
Failure Risk | Probabilistic cost of failure (consequence × probability) | Varies significantly |
This comprehensive framework allows Japanese decision-makers to evaluate the true economic impact of their material selections beyond simple price comparisons.
Comparative Analysis: Standard vs. Premium Spiral Welded Pipes
A typical comparative analysis for a major water transmission project in Japan might reveal the following lifecycle economics (values normalized per kilometer for 1800mm diameter pipeline):
Élément de coût | Standard-Grade Spiral Pipe | Premium WUZHOU Spiral Pipe | Differential |
---|---|---|---|
Coût initial des matériaux | ¥148 million | ¥172 million | -¥24 million |
Coût de l'installation | ¥87 million | ¥82 million | +¥5 million |
50-Year Operational Cost | ¥65 million | ¥58 million | +¥7 million |
50-Year Maintenance Cost | ¥53 million | ¥31 million | +¥22 million |
Replacement Probability | 40% at year 40 (¥94 million) | 10% at year 40 (¥25 million) | +¥69 million |
Failure Risk Cost | ¥18 million | ¥4 million | +¥14 million |
Total 50-Year Cost | ¥465 million | ¥372 million | +¥93 million |
Annualized Cost | ¥9.3 million | ¥7.4 million | +¥1.9 million/year |
This analysis demonstrates that despite a 16% higher initial investment, the premium spiral welded pipe delivers a 20% reduction in total lifecycle cost—a compelling economic case that aligns with Japan’s long-term infrastructure planning philosophy.
Key Value Drivers for Premium Spiral Welded Pipes
Several specific factors drive the enhanced economic value of high-quality spiral welded pipes in Japanese infrastructure applications:
Durée de vie prolongée
Japanese infrastructure planning typically incorporates design lifespans of 50-100 years. High-quality spiral welded pipes with superior metallurgy, enhanced coating systems, and precision manufacturing deliver demonstrable service life advantages:
- Résistance à la corrosion: Premium pipes with advanced coating systems show corrosion rates 35-50% lower than standard products in Japanese environmental exposure tests.
- Structural Durability: Enhanced steel formulations with optimized carbon equivalents demonstrate superior resistance to fatigue in cyclic loading tests that simulate decades of operational stress.
- Joint Integrity: Precision-manufactured pipes with consistent dimensions maintain joint performance over extended periods, reducing the most common failure point in pipeline systems.
Research by the Japan Water Research Center indicates that high-quality spiral welded pipes can extend average service life by 30-45% compared to standard products, creating significant economic value in long-lived infrastructure assets.
Efficacité de l'installation
The dimensional precision and consistency of WUZHOU’s spiral welded pipes delivers measurable advantages during installation:
- Reduced Field Adjustment: Pipes manufactured to tighter dimensional tolerances require less field modification, reducing labor costs by 5-8% in typical Japanese projects.
- Improved Joint Assembly: Consistent end preparation enhances joint reliability while reducing assembly time, with field data showing 12-15% faster joint completion rates.
- Minimized Rework: Superior manufacturing quality reduces rejection rates during field quality control, eliminating costly reinstallation and schedule delays.
Japanese contractors report that high-quality spiral welded pipes can reduce overall installation costs by 4-7% while improving schedule reliability—particularly valuable in Japan’s often constrained urban construction environments.
Optimisation de la maintenance
Maintenance expenditures represent a significant component of infrastructure lifecycle costs in Japan, where labor costs are high and access often challenging. Premium spiral welded pipes deliver measurable maintenance advantages:
- Inspection Interval Extension: Enhanced reliability justifies extended inspection intervals, reducing routine maintenance costs by 15-20%.
- Performance du revêtement: Superior coating systems demonstrate 2-3× longer service life before remediation, substantially reducing one of the most common maintenance requirements.
- Repair Frequency Reduction: Field data from Japanese water utilities indicates that high-quality spiral welded pipes require 60-75% fewer emergency repairs over their service life.
These maintenance advantages translate directly to cost savings while also reducing service disruptions—a critical consideration in Japan’s densely populated urban environments.
Valeur de l'atténuation des risques
Japan’s natural hazard exposure creates extraordinary risk profiles for infrastructure systems. Premium spiral welded pipes deliver measurable risk reduction value:
- Performance sismique: Enhanced ductility and joint design significantly reduce failure probability during seismic events, with associated reduction in potential damage costs.
- Flood Resilience: Superior structural integrity improves performance during flood events when pipes may experience unusual loading conditions.
- Operational Reliability: Reduced failure probability enhances system availability, particularly critical for essential services following natural disasters.
Japanese risk management methodologies typically assign significant economic value to these risk reduction benefits, often justifying 15-20% premium investment to secure enhanced reliability in critical applications.
Case Study: Economic Analysis from Tokyo Metropolitan Water Authority
A comprehensive economic analysis conducted by the Tokyo Metropolitan Water Authority for their eastern transmission main replacement project provides real-world validation of these economic principles:
Project Parameters:
- 12.8km pipeline, 2200mm diameter
- 75-year design life
- Critical service area with high consequence of failure
- Challenging urban installation environment
Economic Comparison Results:
- 22.4% higher initial investment for premium spiral welded pipes
- 8.3% reduction in installation costs due to dimensional precision
- 42.7% reduction in projected maintenance costs
- 65.3% reduction in failure probability
- 17.8% reduction in total lifecycle cost
This analysis led to the specification of premium spiral welded pipes despite higher initial costs, with the project engineers citing “overwhelming economic advantages when evaluated across the full asset lifecycle.”
Supplier Selection Value Factors
For Japanese procurement specialists evaluating spiral welded pipe suppliers, several specific capabilities translate directly to economic value:
Manufacturing Precision
WUZHOU’s advanced manufacturing systems deliver the precision and consistency that create economic value through:
- Reduced field adjustment requirements
- Enhanced joint reliability
- Improved hydraulic efficiency through consistent internal dimensions
- Optimal coating adhesion on properly prepared surfaces
Quality Verification Systems
Comprehensive quality management systems provide economic value through:
- Reduced inspection requirements during installation
- Lower rejection rates and associated rework costs
- Minimized risk of latent defects that could create future failures
- Simplified regulatory approval processes
Capacités d'assistance technique
WUZHOU’s engineering support resources deliver economic value by:
- Optimizing specifications to balance cost and performance
- Resolving application challenges before they impact construction
- Providing field support during critical installation phases
- Offering ongoing technical consultation throughout the asset lifecycle
Procurement Strategy Implications
For Japanese infrastructure developers, this economic analysis suggests several procurement strategy considerations:
- Élaboration des spécifications: Develop detailed technical specifications that capture the quality characteristics that deliver lifecycle value, not merely minimum performance requirements.
- Qualification des fournisseurs: Implement comprehensive supplier qualification processes that evaluate manufacturing capabilities, quality systems, and support resources—not just product samples.
- Economic Evaluation: Employ sophisticated lifecycle cost models that accurately reflect all cost elements across the infrastructure asset’s operational life.
- Contract Structuring: Consider performance guarantees and extended warranty provisions that align supplier incentives with lifecycle performance objectives.
By applying these procurement principles, Japanese infrastructure developers can maximize the economic value of their spiral welded pipe investments, selecting suppliers like WUZHOU who deliver the optimal balance of initial cost and long-term performance.
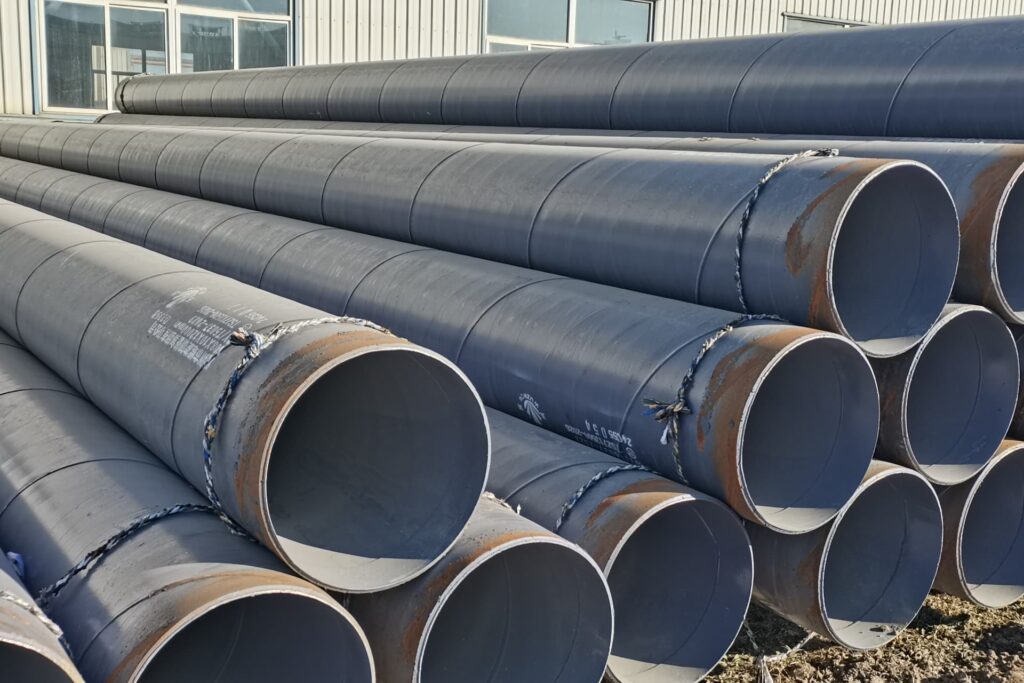
8. Future Trends: Japan’s Evolving Requirements for Spiral Welded Pipe Suppliers
Japan’s infrastructure landscape continues to evolve in response to changing demographic patterns, technological advances, and emerging challenges. For spiral welded pipe suppliers seeking long-term success in the Japanese market, understanding these evolving trends is essential for strategic positioning and product development.
Demographic-Driven Infrastructure Transformation
Japan’s changing population distribution is creating new patterns of infrastructure development and renewal:
Urban Infrastructure Densification
Japan’s major metropolitan centers continue to densify, creating specific challenges and opportunities:
- Constrained Installation Environments: Urban renewal projects increasingly require pipeline installation in extraordinarily limited spaces, creating demand for spiral welded pipes with:
- Enhanced installation efficiency
- Reduced joining space requirements
- Optimized handling characteristics for confined work areas
- Minimal Disruption Requirements: Urban projects increasingly specify “low-impact” construction methods, favoring spiral welded pipe suppliers who can provide:
- Custom length optimization to reduce joint frequency
- Specialized coating systems compatible with trenchless installation
- Enhanced pipe stiffness to reduce installation footprint
- Integrated Utility Corridors: Japan’s “compact city” development philosophy promotes consolidated underground utility corridors, creating demand for large-diameter spiral welded pipes with:
- Specialized internal configurations for multiple service lines
- Enhanced durability for difficult-to-access installations
- Advanced internal coatings for condensation management
Rural Infrastructure Adaptation
Japan’s rural communities face different infrastructure challenges:
- Maintenance-Minimized Systems: Declining rural populations create economic pressure to develop infrastructure with minimal maintenance requirements, favoring spiral welded pipes with:
- Extended service life coating systems
- Enhanced corrosion allowances
- Specialized alloy formulations for specific soil conditions
- Resilient Connections: Rural communities increasingly require self-sufficient infrastructure during disaster events, creating demand for spiral welded pipes with:
- Enhanced seismic resilience
- Specialized connection systems for rapid emergency repair
- Compatibility with decentralized water and energy systems
Technological Evolution in Pipe Systems
Advances in materials science, monitoring technology, and manufacturing processes are reshaping expectations for spiral welded pipe systems:
Smart Pipeline Systems
Japan leads global development of “smart infrastructure” incorporating embedded monitoring capabilities:
- Integrated Sensor Systems: Future specifications increasingly require provisions for:
- Fiber optic monitoring systems embedded in pipe coatings
- Acoustic leak detection technology
- Strain monitoring for seismic activity
- Corrosion monitoring systems
- Data Transmission Infrastructure: Pipeline systems increasingly serve as conduits for monitoring infrastructure, requiring:
- Specialized chamber designs for instrumentation
- Electromagnetic shielding in sensitive applications
- Provisions for power distribution to monitoring systems
Spiral welded pipe manufacturers who can incorporate these technological elements during production gain significant competitive advantages in this evolving market segment.
Advanced Material Technologies
Material science advances are creating new performance expectations:
- Enhanced Steel Formulations: Japanese engineers increasingly specify:
- Micro-alloyed steels with optimized grain structures
- Controlled cooling processes for enhanced mechanical properties
- Specialized chemistry for particular environmental exposures
- Next-Generation Coating Systems: Advanced protection systems gaining market traction include:
- Polymerized nanoceramic composites with enhanced abrasion resistance
- Self-healing coating technologies for extended service life
- Environmentally optimized systems with reduced VOC content
- Specialized Lining Systems: Internal performance is receiving increased focus with:
- Ultra-low friction linings for energy efficiency
- Antimicrobial surfaces for water applications
- Chemical-specific resistance formulations for industrial applications
Sustainability and Environmental Considerations
Japan’s commitment to environmental leadership and carbon reduction is reshaping infrastructure material requirements:
Optimisation de l'empreinte carbone
Japanese procurement increasingly incorporates carbon impact in supplier evaluation:
- Manufacturing Energy Efficiency: Suppliers with documented energy-efficient manufacturing processes gain competitive advantages, with some projects now assigning economic value to carbon reduction.
- Transportation Optimization: Logistics strategies that minimize transportation-related carbon emissions become increasingly important in supplier selection.
- Life Cycle Assessment: Comprehensive environmental impact analysis across the full product lifecycle is becoming standard for major infrastructure projects.
WUZHOU’s environmental management systems (ISO 14001 certified) position the company favorably within this evolving evaluation framework, demonstrating commitment to sustainable manufacturing practices that align with Japan’s environmental priorities.
Circular Economy Integration
Infrastructure planning increasingly incorporates end-of-life considerations:
- Material Recyclability: Specifications now often require documentation of recycling pathways and recovered material value.
- Design for Disassembly: Pipeline systems designed for eventual recovery and recycling gain preference in sustainability-focused projects.
- Material Passport Documentation: Comprehensive documentation of material composition facilitates future recycling, creating new documentation requirements for manufacturers.
Risk Resilience in an Uncertain Climate Future
Japan’s infrastructure planning increasingly incorporates enhanced resilience against emerging climate risks:
Extreme Weather Adaptation
Climate change projections influence infrastructure specifications:
- Enhanced Flood Resilience: Spiral welded pipes for urban drainage increasingly require:
- Higher pressure ratings for surcharged operation
- Enhanced structural design for extreme flow conditions
- Special anchor systems for flood-prone installations
- Temperature Range Expansion: Operating temperature ranges are being extended to accommodate climate uncertainty:
- Enhanced thermal expansion accommodation
- Modified coating systems for temperature extremes
- Specialized joint designs for thermal cycling
Sea Level Impact Mitigation
Coastal infrastructure faces particular challenges:
- Saltwater Intrusion Resistance: Water systems in coastal regions require:
- Enhanced corrosion protection for brackish water exposure
- Special material formulations for saltwater contact
- Design adaptations for changing hydraulic conditions
- Coastal Defense Integration: Spiral welded pipes increasingly serve dual purposes in coastal protection systems:
- Structural elements in seawall systems
- Water management components in surge protection
- Foundation elements in raised infrastructure
Evolving Supply Chain Expectations
Japan’s procurement systems continue to evolve, creating new expectations for international suppliers:
Enhanced Transparency Requirements
Japanese procurement increasingly demands comprehensive supply chain transparency:
- Traçabilité des matériaux: Complete documentation from raw material to finished product becomes standard expectation.
- Manufacturing Process Verification: Detailed documentation of production parameters with verification of quality control procedures.
- Third-Party Certification: Independent verification of manufacturing quality, environmental compliance, and ethical business practices.
WUZHOU’s comprehensive quality management systems provide the documentation infrastructure to meet these evolving transparency requirements, with complete material traceability and production parameter verification for every spiral welded pipe produced.
Collaborative Design Engagement
The traditional procurement model is evolving toward earlier supplier engagement:
- Pre-Specification Consultation: Technical input during the design phase to optimize material selection and application details.
- Performance-Based Specification Development: Collaborative development of specifications that focus on performance outcomes rather than prescriptive requirements.
- Value Engineering Participation: Supplier involvement in identifying cost-optimization opportunities while maintaining performance objectives.
This trend favors spiral welded pipe suppliers with substantial technical resources and application expertise who can contribute value during the earliest project phases.
Strategic Positioning for Future Success
For spiral welded pipe manufacturers like WUZHOU seeking sustained success in the evolving Japanese market, several strategic initiatives deserve particular focus:
- Technical Capability Development: Invest in manufacturing technologies that enhance precision, consistency, and customization capabilities to meet Japan’s increasingly sophisticated requirements.
- Collaborative Research Engagement: Participate in industry research initiatives addressing emerging challenges in Japanese infrastructure applications.
- Certification Advancement: Pursue additional quality and environmental certifications that align with Japan’s evolving evaluation frameworks.
- Technical Support Enhancement: Develop application engineering resources specifically focused on Japan’s unique infrastructure challenges and construction methodologies.
- Sustainability Documentation: Implement comprehensive environmental impact assessment and documentation systems that meet Japan’s emerging standards for supplier evaluation.
By aligning strategic development initiatives with these emerging trends, WUZHOU can strengthen its position as a preferred supplier for Japan’s evolving infrastructure projects, delivering the advanced spiral welded pipe systems that will support Japan’s next generation of infrastructure excellence.
9. FAQs: Common Questions About Supplying Spiral Welded Pipes to the Japanese Market
General Market Questions
Q: What is the current market size for spiral welded pipes in Japan?
A: Japan’s annual consumption of spiral welded pipes exceeds 300,000 metric tons, with a market value approaching ¥180 billion (approximately $1.3 billion). The market demonstrates steady growth of 3.5-4.2% annually, driven primarily by infrastructure replacement and disaster resilience projects. Water transmission represents the largest application segment (38%), followed by energy infrastructure (27%), and urban utility systems (23%).
Q: How does Japan’s spiral welded pipe market differ from other developed economies?
A: Japan’s market shows several distinctive characteristics:
- Significantly higher quality specifications, particularly for dimensional tolerance and weld quality
- Greater emphasis on seismic performance requirements
- More rigorous documentation and material traceability requirements
- Longer design life expectations (typically 75-100 years versus 50 years in many markets)
- Higher willingness to invest in premium products that deliver lifecycle cost advantages
For suppliers like WUZHOU, these characteristics create both higher entry barriers and greater value opportunities than many global markets.
Q: What are the primary market entry challenges for international suppliers?
A: International suppliers face several specific challenges in the Japanese market:
- Complex qualification processes requiring substantial documentation
- Preference for suppliers with established Japanese market presence
- High expectations for Japanese-language technical support
- Rigorous conformance to Japan-specific standards and certification requirements
- Cultural emphasis on long-term business relationships over transactional engagements
Successful suppliers typically navigate these challenges through strategic partnerships, comprehensive localization of technical materials, and patient relationship development with key industry stakeholders.
Questions techniques et spécifications
Q: How do Japanese technical standards for spiral welded pipes differ from international standards?
A: Japanese standards incorporate several distinctive requirements:
- Tighter dimensional tolerances (typically ±0.5% on diameter versus ±0.75% internationally)
- Enhanced mechanical property verification, particularly for cyclic loading performance
- More comprehensive non-destructive testing protocols, often requiring 100% inspection versus sampling approaches
- Specialized requirements for seismic performance verification
- Additional documentation requirements for material traceability and quality verification
WUZHOU’s manufacturing capabilities align exceptionally well with these enhanced requirements, with production tolerance control that typically exceeds even Japanese standards.
Q: What are the most important quality verification requirements for spiral welded pipes in Japanese projects?
A: Japanese specifications typically emphasize:
- Comprehensive ultrasonic testing of spiral welds, usually requiring 100% coverage
- Enhanced hydrostatic testing protocols with extended test durations
- Material verification through both chemical analysis and mechanical property testing
- Specialized testing for seismic performance characteristics
- Detailed dimensional verification including roundness and straightness
- Coating integrity verification through holiday detection and adhesion testing
WUZHOU’s quality control system incorporates all these verification elements, with capabilities exceeding typical Japanese requirements in most categories.
Q: What coating systems are preferred for spiral welded pipes in Japanese applications?
A: Japanese specifications vary by application, but commonly require:
- External coatings: Three-layer polyethylene (3LPE) or fusion-bonded epoxy (FBE) with enhanced thickness profiles
- Internal linings: Cement mortar with specific additives for water applications, or epoxy systems for industrial services
- Special considerations: Enhanced UV resistance for exposed installations, specialized formulations for thermal cycling in geothermally active regions
WUZHOU’s coating capabilities include all these systems, with their dedicated coating lines providing the consistency and quality control that Japanese specifications demand.
Procurement and Business Questions
Q: What certification requirements apply to spiral welded pipe suppliers in Japan?
A: Japanese procurement typically requires:
- ISO 9001 Quality Management System certification
- ISO 14001 Environmental Management System certification
- API 5L certification for petroleum application pipes
- JIS (Japanese Industrial Standard) compliance verification
- Specific certifications for water applications from the Japan Water Works Association
WUZHOU’s comprehensive certification portfolio satisfies these requirements, with their double-sided submerged arc welded spiral steel pipes certified to both API 5L and EU standards, complemented by ISO 9001 and ISO 14001 management system certifications.
Q: How does the Japanese procurement process for spiral welded pipes typically operate?
A: Japanese infrastructure projects typically follow a structured procurement approach:
- Supplier pre-qualification evaluating manufacturing capabilities, quality systems, and reference projects
- Detailed technical specification development often incorporating supplier consultation
- Request for proposals with comprehensive technical requirements and documentation expectations
- Technical evaluation focusing on compliance, quality systems, and lifecycle performance
- Commercial evaluation incorporating both initial cost and lifecycle economic considerations
- Supplier selection followed by detailed contract negotiation
Successful international suppliers like WUZHOU typically dedicate significant resources to the pre-qualification and specification development phases, establishing their technical credentials before commercial discussions begin.
Q: What payment terms and financial arrangements are typical in Japanese spiral welded pipe procurement?
A: Japanese procurement typically involves:
- Letter of credit arrangements for international suppliers
- Progressive payment structures linked to manufacturing milestones
- Quality verification requirements tied to payment releases
- Retention provisions pending final installation verification
- Performance guarantees covering early-life operation
- Warranty periods of 2-5 years depending on application
WUZHOU’s financial stability and established international business practices allow flexible accommodation of these typical Japanese payment structures.
Logistics and Implementation Questions
Q: What are the typical lead times for spiral welded pipe orders for Japanese projects?
A: Lead time expectations vary by project scale and application:
- Standard water transmission projects: 12-16 weeks from order to delivery
- Large-scale infrastructure projects: 16-24 weeks with progressive delivery schedules
- Emergency replacement requirements: Expedited production capabilities for 8-10 week delivery
WUZHOU’s substantial production capacity with 11 spiral pipe production lines enables flexible scheduling to meet Japanese project timelines, with capacity to accommodate both scheduled projects and urgent requirements.
Q: How are quality verification and inspection typically handled for Japanese projects?
A: Japanese procurement typically implements:
- Detailed quality plans established during contract negotiation
- In-factory inspection by either client representatives or third-party inspectors
- Comprehensive documentation review before shipment approval
- Material certification verification against raw material records
- Final acceptance testing following delivery
WUZHOU’s quality management system accommodates these verification requirements, with facilities for client inspectors and comprehensive documentation systems that satisfy Japanese verification protocols.
Q: What special packaging or shipping requirements apply to spiral welded pipes for the Japanese market?
A: Japanese projects typically specify:
- Enhanced end protection systems for ocean transportation
- Specialized coating protection during handling and shipping
- Comprehensive marking systems for installation sequence tracking
- Detailed documentation packages accompanying shipments
- Special provisions for unloading at space-constrained Japanese ports
WUZHOU’s logistics expertise includes these specialized requirements, with customized packaging systems developed specifically for the demands of international shipping to Japan.
Questions spécifiques à la candidature
Q: What special considerations apply to spiral welded pipes for Japanese water infrastructure?
A: Japanese water infrastructure applications typically require:
- Enhanced internal linings suitable for Japan’s specific water chemistry
- Special attention to joint design for seismic movement accommodation
- Cathodic protection compatibility for corrosion management
- Integration provisions for advanced monitoring systems
- Extended design life expectations (80-100 years)
WUZHOU’s water infrastructure experience includes these specialized requirements, with particular expertise in seismically resistant joint systems and long-life coating technologies.
Q: How do Japanese requirements for energy infrastructure differ from international norms?
A: Japanese energy infrastructure applications feature:
- Higher safety factors for densely populated installation areas
- Enhanced fracture toughness requirements for seismic resilience
- More rigorous pressure cycling performance verification
- Specialized requirements for hydrogen compatibility in emerging applications
- Advanced coating systems for varied installation environments
WUZHOU’s energy sector expertise encompasses these specialized requirements, with material formulations and manufacturing processes optimized for these demanding applications.
Q: What are the key considerations for spiral welded pipes in Japanese disaster prevention infrastructure?
A: Japan’s disaster prevention infrastructure requires spiral welded pipes with:
- Extraordinary structural integrity for tsunami defense systems
- Enhanced flexibility for seismic isolation applications
- Special connection systems for rapid emergency deployment
- Material formulations optimized for extreme loading conditions
- Integration capabilities with monitoring and warning systems
WUZHOU’s manufacturing capabilities support these specialized requirements, with their advanced production systems capable of producing the custom configurations these applications demand.
WUZHOU-Specific Questions
Q: How does WUZHOU ensure quality consistency for Japanese infrastructure projects?
A: WUZHOU implements several specific quality assurance approaches:
- 100% inspection of spiral welds through ultrasonic testing exceeds typical Japanese requirements
- Comprehensive hydrostatic testing of every pipe ensures pressure integrity
- X-ray examination verifies internal weld characteristics for critical applications
- Complete material traceability from steel production through pipe manufacturing
- Finished product verification through comprehensive dimensional control
This multi-layered quality system generates the verification documentation Japanese projects require while ensuring consistent performance in demanding applications.
Q: What technical support does WUZHOU provide for Japanese infrastructure projects?
A: WUZHOU offers comprehensive technical support including:
- Pre-project consultation during specification development
- Application-specific engineering guidance for challenging installations
- Field technical representatives during critical project phases
- Comprehensive documentation packages aligned with Japanese requirements
- Post-installation support throughout product lifecycle
This technical support capability has proven particularly valuable for complex Japanese infrastructure projects with specialized requirements.
Q: How does WUZHOU address the seismic performance requirements of Japanese infrastructure?
A: WUZHOU implements several specific approaches to enhance seismic performance:
- Specialized steel formulations with optimized ductility characteristics
- Enhanced weld profiles designed for improved fatigue performance
- Advanced spiral forming processes that minimize residual stress
- Joint compatibility with seismic-resistant connection systems
- Comprehensive testing protocols that verify performance under dynamic loading
These capabilities address one of the most critical requirements for spiral welded pipes in Japanese infrastructure applications, aligning perfectly with Japan’s emphasis on disaster-resistant infrastructure systems.
Conclusion
The Japanese market for spiral welded pipes presents both substantial opportunities and specific challenges for international suppliers. Success requires alignment with Japan’s exacting quality expectations, comprehensive documentation capabilities, and commitment to long-term relationship development.
WUZHOU’s advanced manufacturing capabilities, rigorous quality management systems, and comprehensive technical support resources position the company as an ideal supplier for Japan’s sophisticated infrastructure projects. With production capabilities that meet or exceed Japanese standards and certification frameworks that satisfy Japanese qualification requirements, WUZHOU offers Japanese infrastructure developers the optimal combination of premium quality and competitive value.
For project developers seeking to optimize the performance, reliability, and economic value of their spiral welded pipe applications, WUZHOU represents a trusted partner with demonstrated capabilities aligned with Japan’s commitment to infrastructure excellence.