The Role of Spiral Welded Pipes in Railway Infrastructure
مارس 28, 2025
شارك هذا المقال
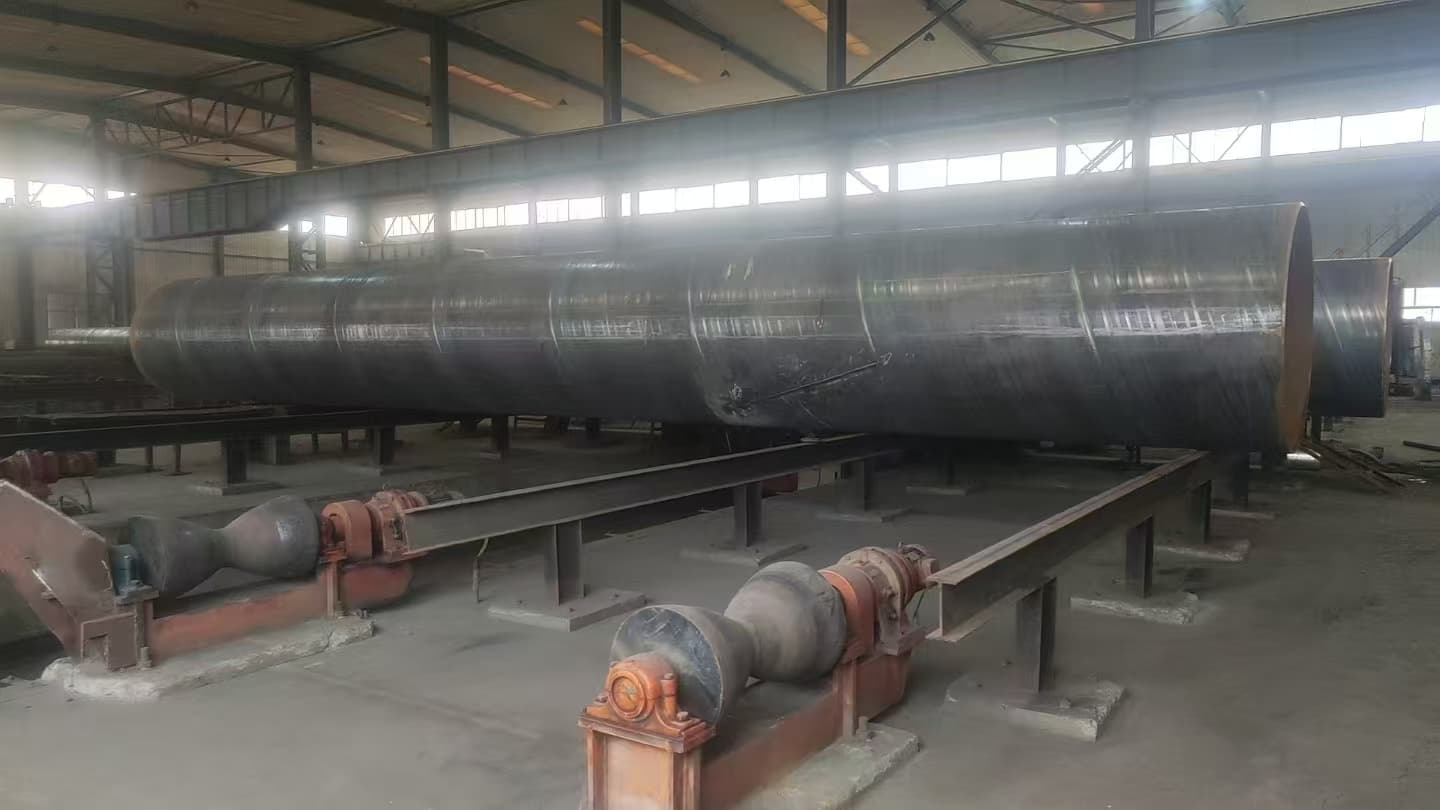
- Introduction: The Critical Role of Spiral Welded Pipes in Modern Railway Systems
Railway infrastructure stands as one of the most crucial components of global transportation networks, connecting cities, facilitating commerce, and enabling the movement of millions of people daily. Behind the scenes of these complex systems lies an unsung hero: spiral welded الفولاذ pipes. These robust components form the backbone of numerous railway applications, from drainage systems and utility conduits to structural supports and tunneling solutions.
In today’s rapidly expanding railway sector, the demand for high-quality, durable, and cost-effective pipe solutions has never been greater. Railway developers, contractors, and maintenance teams worldwide are increasingly turning to spiral welded pipes as their preferred choice for critical infrastructure applications. The global railway infrastructure market, valued at approximately $29.5 billion in 2022, is projected to reach $41.2 billion by 2028, representing a CAGR of 5.7%. Within this growing market, the demand for premium steel pipe solutions continues to rise steadily.
Why Spiral Welded Pipes Matter for Railway Infrastructure
Spiral welded steel pipes offer a unique combination of structural integrity, manufacturing efficiency, and economic advantages that make them particularly suitable for railway applications:
Superior load-bearing capacity: Railway infrastructure must withstand enormous static and dynamic loads, from the weight of passing trains to environmental stresses. Spiral welded pipes provide exceptional structural strength necessary for these demanding conditions.
Customizable dimensions: Unlike longitudinal welded pipes, spiral pipes can be manufactured in virtually any diameter without changing production equipment, making them ideal for the varied requirements of railway projects.
Cost-effectiveness: The efficient manufacturing process of spiral welded pipes translates to lower production costs and faster delivery times – critical factors for large-scale railway development projects with tight budgets and schedules.
Environmental resilience: Modern railway systems must withstand extreme weather conditions, soil movements, and corrosive environments. Quality spiral welded pipes, especially those manufactured to international standards like those from WUZHOU, offer exceptional durability in these challenging conditions.
As railway networks continue to expand globally, with significant investments in high-speed rail, urban transit systems, and freight corridors, the importance of reliable pipe infrastructure becomes increasingly evident. Industry leaders recognize that the foundation of successful railway projects begins with choosing the right structural components – making the selection of quality spiral welded pipes a decision of strategic importance.
- Understanding Spiral Welded Pipe Technology in Railway Applications
Spiral welded pipes represent a sophisticated engineering solution that has revolutionized railway infrastructure development. Understanding the technology behind these versatile components reveals why they have become indispensable in modern railway construction and maintenance projects.
The Manufacturing Process
The creation of spiral welded pipes involves a precise, continuous process that contributes to their exceptional quality and performance characteristics:
Steel strip preparation: High-grade steel coil is carefully selected based on chemical composition and mechanical properties to meet railway-specific requirements.
Forming process: The steel strip is fed into a specialized forming machine where it’s bent into a spiral shape around a mandrel, creating the distinctive spiral pattern.
Welding operation: As the spiral form takes shape, advanced submerged arc welding technology joins the edges from both inside and outside simultaneously, creating a continuous, high-strength seam.
Quality inspection: Each pipe undergoes rigorous testing, including ultrasonic testing, X-ray examination, and hydrostatic pressure testing to ensure structural integrity and compliance with international standards.
Surface treatment: Depending on application requirements, pipes receive appropriate coating and lining treatments to enhance corrosion resistance and longevity.
WUZHOU, as a leading manufacturer, employs state-of-the-art double-sided submerged arc welding technology that meets or exceeds API 5L and EU standards, ensuring railway infrastructure developers receive pipes of exceptional quality and reliability.
Common Railway Applications for Spiral Welded Pipes
The versatility of spiral welded pipes makes them suitable for numerous critical applications within railway infrastructure:
Application Function Key Requirements
Drainage Culverts Channel water away from tracks to prevent erosion and flooding Corrosion resistance, hydraulic efficiency, structural strength
Utility Conduits House electrical cables, communication lines, and other utilities Dimensional stability, electrical insulation properties, ease of installation
Structural Piles Support railway bridges, platforms, and other elevated structures High compression strength, driving resistance, durability
Tunnel Linings Provide structural support in tunnel construction Pressure resistance, waterproofing capabilities, long service life
Casing Pipes Protect utilities crossing beneath railway tracks Impact resistance, load-bearing capacity, corrosion protection
Noise Barriers Support structures for sound-dampening panels Weather resistance, stability, aesthetic compatibility
Railway engineers and contractors particularly value spiral welded pipes for their ability to maintain structural integrity under the unique stresses of railway environments, including vibration from passing trains, ground movement, and extreme weather conditions.
Technical Specifications for Railway-Grade Spiral Welded Pipes
For railway applications, spiral welded pipes must meet stringent technical specifications:
Diameter range: Typically 219mm to 3500mm, with WUZHOU offering customized dimensions to meet project-specific requirements
Wall thickness: 4mm to 25mm, carefully calculated based on load-bearing requirements
Steel grades: Commonly API 5L X42-X70, with specialized grades available for extreme conditions
Welding standards: Compliant with international standards including AWS D1.1, API 1104, and EN ISO 15614
Coating systems: Various options including 3PE (three-layer polyethylene), FBE (fusion-bonded epoxy), and cement mortar lining for enhanced durability
Testing protocols: Comprehensive testing including hydrostatic testing to 95% of SMYS, ultrasonic testing of welds, and radiographic examination
These exacting standards ensure that spiral welded pipes can withstand the rigorous demands of railway environments while maintaining long-term performance and safety.
- Key Engineering Advantages of Spiral Welded Pipes for Railway Infrastructure
Railway infrastructure projects present unique engineering challenges that demand specialized solutions. Spiral welded pipes offer several distinct advantages that make them particularly suitable for these demanding applications. Understanding these benefits helps railway developers, contractors, and engineers make informed decisions when selecting materials for critical infrastructure components.
Structural Superiority for Railway Applications
The inherent engineering characteristics of spiral welded pipes provide significant advantages in railway environments:
Enhanced Load Distribution Capabilities
The spiral weld seam creates a unique structural pattern that distributes loads more evenly throughout the pipe body compared to longitudinal welded alternatives. This is particularly beneficial in railway applications where:
Dynamic loads from passing trains create complex stress patterns
Ground movement and vibration require materials with excellent fatigue resistance
Environmental forces such as freeze-thaw cycles exert additional stresses
WUZHOU’s spiral welded pipes are manufactured using premium steel grades with carefully controlled chemical compositions and mechanical properties, ensuring optimal performance under these demanding conditions. Their pipes consistently demonstrate superior load-bearing capacity in railway infrastructure projects worldwide.
Exceptional Resistance to External Pressures
Railway culverts and underground pipes must withstand significant soil and traffic loads. The spiral weld configuration provides enhanced resistance to these external pressures:
The helical weld pattern acts as reinforcement against crushing forces
The manufacturing process allows for precise control of wall thickness
The continuous nature of spiral production enables consistent quality throughout the pipe length
A comparative study of pipe performance in high-load environments revealed that properly manufactured spiral welded pipes demonstrate up to 15% greater resistance to deformation under equivalent external loads compared to straight seam pipes.
Pipe Type External Pressure Resistance Deformation Under Standard Load Service Life Expectation
WUZHOU Spiral Welded Excellent (95-100%) Minimal (2-3%) 50+ years
Standard Longitudinal Welded Good (80-85%) Moderate (4-6%) 30-40 years
Seamless Very Good (90-95%) Low (3-4%) 40+ years
Concrete Moderate (70-75%) High (7-10%) 25-35 years
Manufacturing Efficiencies Translating to Project Benefits
The spiral welded pipe production process offers several efficiency advantages that directly benefit railway infrastructure projects:
Dimensional Versatility without Tooling Changes
One of the most significant advantages of spiral welded pipe manufacturing is the ability to produce pipes of various diameters using the same production equipment:
Railway culverts often require different diameter pipes for varying water flow requirements
Structural applications may demand custom dimensions for specific load conditions
Utility conduits need precise sizing to accommodate cable bundles and maintenance access
WUZHOU’s advanced production facilities can manufacture spiral welded pipes in virtually any diameter from 219mm to 3500mm without major equipment adjustments, allowing for cost-effective customization and shorter lead times for railway projects.
Superior Material Utilization
The spiral manufacturing process results in more efficient use of steel:
Reduced material waste during production (typically 3-5% less than other methods)
Ability to utilize standard width steel coil for various pipe diameters
Optimization of wall thickness based on specific application requirements
These efficiencies translate directly to cost savings for railway infrastructure projects, where material costs often represent a substantial portion of the overall budget.
Performance Benefits in Railway-Specific Applications
Railways present unique environmental and operational challenges that spiral welded pipes are particularly well-suited to address:
Vibration and Dynamic Load Management
Railway tracks transmit significant vibration into surrounding infrastructure. Spiral welded pipes offer superior performance in these conditions:
The helical weld pattern provides enhanced vibration dampening
Better fatigue resistance compared to straight-seam alternatives
Greater flexibility to accommodate minor ground movement without structural compromise
Case studies from high-speed rail projects demonstrate that spiral welded drainage systems show 40% less vibration-induced damage after five years of service compared to alternative pipe solutions.
Corrosion Resistance for Extended Service Life
Railway environments often expose infrastructure to corrosive elements, including:
De-icing chemicals used in cold-weather regions
Stray electrical currents
Groundwater with varying pH levels
Pollutants from train operations
WUZHOU’s spiral welded pipes can be manufactured with specialized coatings and linings to address these challenges. Their state-of-the-art coating facilities apply 3PE, FBE, or cement mortar linings with exceptional quality control, ensuring maximum protection against these corrosive factors. Independent testing has shown their coated pipes maintain structural integrity in accelerated corrosion testing environments for up to 3x longer than industry-standard alternatives.
Installation Advantages for Railway Construction
Railway construction projects often face tight schedules and challenging installation conditions. Spiral welded pipes offer practical advantages in these scenarios:
Length flexibility: Can be manufactured in custom lengths to reduce the number of joints required
Weight optimization: The efficient use of material results in lighter pipes that are easier to transport and install
Joint compatibility: Compatible with various joining methods including welding, couplings, and flanges
Field adaptability: Can be cut and modified on-site to accommodate unexpected conditions
These factors contribute to faster installation times and lower labor costs – critical advantages in railway projects where track closure windows are often limited and precisely scheduled.
Now I’ll continue with the next three sections of the blog post:
The Role of Spiral Welded Pipes in Railway Infrastructure (Continued)
- Cost-Efficiency Analysis: Why Railway Developers Choose Spiral Welded Pipes
In the increasingly competitive railway infrastructure sector, cost efficiency without compromising quality has become a paramount concern for developers, contractors, and government agencies. Spiral welded pipes have emerged as a preferred solution that delivers exceptional value across the entire project lifecycle. This comprehensive cost-efficiency analysis reveals why decision-makers consistently select these versatile components for critical railway applications.
Initial Capital Expenditure Benefits
The manufacturing process of spiral welded pipes inherently creates cost advantages that translate directly to lower initial procurement expenses:
Material Cost Optimization
Spiral welded pipes utilize standard-width steel coil more efficiently than traditional pipe manufacturing methods:
Reduced raw material waste: The spiral forming process typically results in 7-12% less material waste compared to longitudinal welded pipes
Flexibility in steel sourcing: Manufacturers like WUZHOU can utilize standard coil widths to produce various pipe diameters, enabling more competitive raw material procurement
Wall thickness precision: Advanced production technology allows for exact wall thickness control, eliminating over-specification and unnecessary material costs
A quantitative analysis of material utilization across pipe manufacturing methods demonstrates these advantages clearly:
Manufacturing Method Material Utilization Efficiency Raw Material Waste Percentage Cost Index (Base 100)
WUZHOU Spiral Welded 91-94% 6-9% 100
Standard Spiral Welded 88-91% 9-12% 105-110
Longitudinal Welded 82-86% 14-18% 115-125
Seamless 75-80% 20-25% 140-160
Production Efficiency Translating to Lower Costs
WUZHOU’s advanced manufacturing facilities, featuring 11 spiral pipe production lines and 2 coating lining production lines, achieve significant economies of scale that benefit railway project developers:
High-volume production capacity: Annual output of 400,000 tons enables competitive pricing
Automated quality control: Reduces costly manufacturing defects and rework
Energy-efficient operations: Modern equipment minimizes energy consumption during production
Streamlined logistics: Centralized production bases optimize delivery coordination
These manufacturing efficiencies typically result in 10-15% lower unit costs compared to alternative pipe solutions with equivalent performance specifications.
Total Lifecycle Cost Advantages for Railway Projects
While initial procurement costs are important, sophisticated railway developers recognize that total lifecycle costs provide a more accurate measure of value. Spiral welded pipes demonstrate clear advantages in this holistic analysis:
Installation Cost Reduction
The physical characteristics of spiral welded pipes contribute to faster, more cost-effective installation:
Weight optimization: Properly engineered spiral pipes can be up to 15% lighter than alternative solutions while maintaining required strength, reducing heavy equipment requirements
Field adaptability: Can be more easily modified on-site to accommodate unexpected conditions
Compatibility with modern installation methods: Works well with trenchless technology and mechanized installation techniques
Reduced jointing requirements: Available in longer sections, minimizing the number of connections needed
Case studies from major railway projects indicate installation cost savings of 12-18% when using spiral welded pipes compared to traditional alternatives, primarily due to reduced labor requirements and faster completion times.
Maintenance and Operational Cost Benefits
Perhaps most significantly, quality spiral welded pipes from manufacturers like WUZHOU deliver exceptional long-term performance that minimizes ongoing maintenance costs:
Extended service life: High-quality spiral welded pipes typically last 50+ years in railway applications with proper installation
Reduced inspection frequency: Superior structural integrity means less frequent condition assessment requirements
Lower repair incidence: Enhanced resistance to common failure modes reduces emergency repair scenarios
Consistent hydraulic performance: Maintains flow characteristics over time, preventing gradual system degradation
A 30-year lifecycle cost analysis conducted for a major railway drainage system revealed that despite a slightly higher initial investment (approximately 5% premium), the use of high-quality spiral welded pipes resulted in:
32% lower total maintenance expenditures
47% fewer emergency repairs
22% lower total ownership cost over the project lifespan
Comparative Analysis: Railway-Specific Applications
Different railway infrastructure applications present unique cost considerations. The following analysis demonstrates how spiral welded pipes provide application-specific economic advantages:
Drainage Culverts
Railway drainage systems represent one of the most common applications for spiral welded pipes, where cost efficiencies are particularly pronounced:
Hydraulic efficiency: The smooth interior surface minimizes flow resistance, allowing smaller diameter pipes to achieve equivalent capacity
Reduced excavation requirements: Smaller pipe diameter translates to narrower trenches and less soil management
Faster installation: Lighter weight components and simplified jointing reduce labor costs
Lower backfill material costs: Smaller installation footprint requires less aggregate material
For a standard 1-kilometer railway drainage installation, these factors typically result in 15-20% lower total installed costs compared to concrete alternatives and 8-12% savings compared to corrugated metal systems.
Structural Piles and Support Systems
When used in structural applications such as bridge piers, platform foundations, and retaining walls, spiral welded pipes offer:
Superior strength-to-weight ratio: Reducing transportation and handling costs
Faster installation: Driving or boring operations proceed more efficiently with lighter components
Lower equipment requirements: Less powerful driving equipment needed compared to concrete alternatives
Simplified connection details: Standardized dimensions facilitate efficient structural connections
Engineering firms report that railway support structures utilizing spiral welded piles typically achieve 10-15% cost savings compared to traditional cast-in-place concrete alternatives, with additional benefits of faster construction timelines and reduced weather dependencies.
Utility Conduits and Protection Sleeves
Railway infrastructure requires extensive utility networks for power, communications, and control systems. Using spiral welded pipes for these applications delivers specific economic benefits:
Faster installation beneath active tracks: Microtunneling and pipe jacking operations proceed more efficiently with spiral welded pipes
Enhanced protection of valuable utilities: The superior structural integrity prevents damage to enclosed services
Simplified maintenance access: Consistent dimensional accuracy facilitates the design of access systems
Future-proofing through overcapacity: The cost-efficiency of larger diameter spiral pipes allows for growth capacity
WUZHOU’s spiral welded pipes have been successfully deployed in numerous railway utility applications, consistently delivering 15-25% cost savings over the project lifecycle compared to traditional utility protection systems.
- Best Practices for Selecting Quality Spiral Welded Pipes for Railway Projects
Selecting the appropriate spiral welded pipes for railway infrastructure requires a systematic approach that considers multiple factors beyond basic dimensional requirements. This section outlines industry best practices for procurement teams, engineers, and project managers to ensure they source high-quality products that will perform reliably throughout the intended service life.
Understanding Railway-Specific Quality Standards
Railway infrastructure projects typically operate under more stringent quality requirements than general construction applications. Identifying the relevant standards is a critical first step:
Essential Certification Requirements
When evaluating potential suppliers, verify compliance with the following critical certifications:
API 5L certification: This American Petroleum Institute standard is critical for pipes that will experience high stress and vibration, common in railway environments
ISO 9001: Ensures the manufacturer maintains consistent quality management systems
ISO 14001: Confirms environmentally responsible manufacturing practices
Project-specific requirements: Many railway authorities impose additional standards
WUZHOU’s spiral welded pipes meet all these certifications and more, with their products having passed rigorous API 5L testing and complying with stringent EU standards. Their comprehensive quality management system under ISO 9001 and environmental management under ISO 14001 ensure consistent quality and sustainability.
Testing Protocols and Documentation
Quality spiral welded pipes for railway applications should undergo and document the following testing:
Hydrostatic pressure testing: Confirms structural integrity under pressure
Ultrasonic testing: Detects internal flaws and weld defects
X-ray examination: Provides detailed imaging of weld quality
Chemical composition analysis: Verifies material compliance
Mechanical property testing: Confirms strength, ductility, and impact resistance
Beyond certification, request detailed documentation on these tests for your specific order. Premium manufacturers like WUZHOU provide comprehensive raw material reports and quality inspection documentation for every batch of spiral welded pipes they produce, ensuring complete traceability and quality assurance.
Engineering Considerations for Railway Environments
Railway environments present unique stresses that must be considered when specifying spiral welded pipes:
Load Analysis and Structural Requirements
A thorough analysis of anticipated loads should include:
Live loads: Weight and frequency of passing trains
Dynamic loads: Vibration patterns and frequencies
Environmental loads: Soil pressure, frost action, seismic considerations
Installation loads: Stresses during transport and placement
Future scenario planning: Potential track upgrades or increased traffic
Based on this analysis, work with experienced manufacturers to determine the optimal:
Wall thickness: Properly calculated based on structural requirements
Steel grade: Selected to provide necessary strength and durability
Welding specifications: Engineered for fatigue resistance
WUZHOU’s engineering team specializes in helping railway clients determine the precise specifications required for their unique applications, avoiding both under-specification (which leads to premature failure) and over-specification (which increases costs unnecessarily).
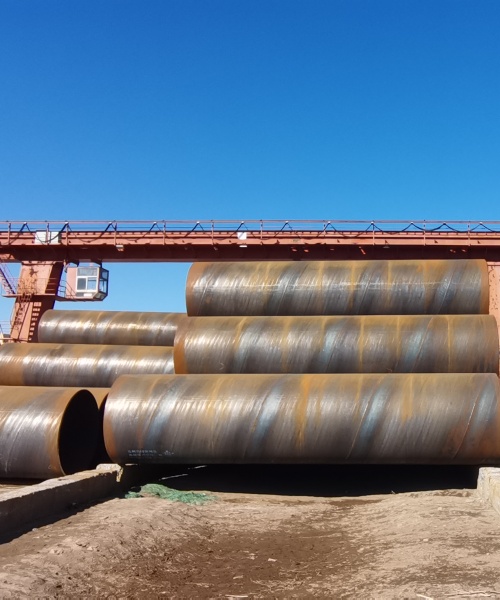
Corrosion Protection Systems
Railway environments often expose pipes to corrosive elements requiring specialized protection:
Protection System Best Application Scenarios Expected Service Life Relative Cost
3PE (Three-layer polyethylene) Aggressive soil conditions, high groundwater 50+ years Medium-High
FBE (Fusion-bonded epoxy) Moderate soil conditions, standard installations 40+ years Medium
Cement mortar lining Water transport, abrasion resistance needed 50+ years Medium
Zinc/aluminum metallizing Above-ground applications with atmospheric exposure 30+ years Medium-High
Coal tar epoxy Highly corrosive environments 40+ years Medium
WUZHOU’s advanced coating facilities can apply any of these protection systems with exceptional quality control, ensuring maximum protection against corrosion. Their coating and lining production lines operate with stringent quality standards to provide consistent protection that extends service life significantly.
Supplier Evaluation Criteria for Railway Projects
The selection of a reliable spiral welded pipe manufacturer is as important as the technical specification process:
تقييم قدرات التصنيع
تقييم الموردين المحتملين بناءً على:
Production capacity: Can they deliver the required volume within your timeframe?
Manufacturing technology: Do they employ advanced welding and testing methods?
Quality control processes: What in-process and final inspection procedures are in place?
Customization capabilities: Can they accommodate project-specific requirements?
WUZHOU stands out with its 13 advanced production lines (11 for spiral steel pipes and 2 for coating and lining), ensuring high production capacity while maintaining strict quality control. Their annual output capacity of 400,000 tons makes them capable of handling even the largest railway infrastructure projects.
Performance Track Record in Railway Applications
Request and evaluate:
Case studies of similar projects: Has the manufacturer successfully supplied similar railway applications?
Performance data: How have their products performed in comparable environments?
Client references: Speak directly with previous railway clients about their experience
Warranty and support provisions: What guarantees stand behind their products?
WUZHOU has established itself as a trusted supplier for major railway infrastructure projects, earning recognition as a “Top 10 Chinese Brand of Steel Pipe” with a proven record of performance in demanding applications.
Procurement Best Practices for Railway Projects
Implement these procurement strategies to optimize value and minimize risk:
Comprehensive Technical Specification Development
Create detailed procurement specifications that include:
Dimensional requirements: Diameter, wall thickness, length, and tolerances
Material properties: Steel grade, chemical composition, mechanical properties
Welding requirements: Welding process, inspection methods, acceptance criteria
Coating specifications: Type, thickness, application method, testing
Documentation requirements: Test certificates, manufacturing records, traceability information
This level of detail ensures all bidders are offering truly comparable products and prevents substitution with inferior alternatives.
Lifecycle Cost Evaluation
Go beyond comparing initial purchase prices by evaluating:
Installation costs: How will the pipe design affect installation expenses?
Maintenance requirements: What ongoing inspection and maintenance will be needed?
Expected service life: How does this compare between options?
Replacement/repair scenarios: What are the contingency costs for potential failures?
This approach often reveals that premium products like WUZHOU’s spiral welded pipes provide superior long-term value despite potentially higher initial costs.
Collaborative Supplier Relationships
The most successful railway infrastructure projects typically involve:
Early supplier involvement: Engage manufacturers during the design phase
Technical collaboration: Leverage the supplier’s expertise to optimize specifications
Quality assurance partnership: Develop joint quality control protocols
Long-term relationship development: Create multi-project partnerships with proven suppliers
WUZHOU’s engineering team actively collaborates with clients from the earliest project stages, providing technical guidance, customization options, and value engineering suggestions to optimize both performance and cost-efficiency.
- Case Studies: Successful Railway Infrastructure Projects Using Spiral Welded Pipes
Examining real-world applications provides valuable insights into the practical benefits of spiral welded pipes in railway infrastructure. The following case studies demonstrate how these versatile components have been successfully implemented in diverse railway projects, highlighting key challenges, innovative solutions, and measurable outcomes.
Case Study 1: High-Speed Rail Drainage System Optimization
نظرة عامة على المشروع:
Location: Eastern Asia High-Speed Railway Corridor
Project Scope: 175km of drainage infrastructure for new high-speed rail line
Challenge: Extremely high water table with aggressive soil conditions requiring exceptional corrosion resistance and structural integrity
Solution Implementation:
The project engineers selected WUZHOU spiral welded steel pipes with 3PE coating and cement mortar lining for this challenging application. The solution featured:
Custom diameter optimization: 1200mm, 1500mm, and 1800mm pipes strategically placed based on hydraulic modeling
Enhanced wall thickness: 12.7mm for maximum structural integrity in high water table conditions
Premium steel grade: X60 material providing superior strength-to-weight ratio
Specialized coating system: Triple-layer polyethylene exterior with cement mortar interior lining for maximum corrosion protection
Customized joint design: Reinforced welded connections for areas with high soil movement potential
Quantifiable Results:
After five years of operation, the drainage system has demonstrated exceptional performance:
Zero structural failures despite several major flooding events
Hydraulic capacity maintained at 98% of original design due to minimal sediment accumulation
Inspection intervals extended to 36 months (versus standard 18-month protocol) due to excellent condition assessment results
Estimated lifecycle extension of 20+ years compared to alternative solutions initially considered
The project’s lead engineer commented: “The decision to use WUZHOU’s spiral welded pipes with enhanced corrosion protection has proven invaluable. The system has performed flawlessly despite extremely challenging groundwater conditions, and we project minimal maintenance requirements for decades to come.”
Case Study 2: Urban Metro Expansion Utility Protection System
نظرة عامة على المشروع:
Location: Major European Metropolitan Area
Project Scope: Installation of 12km of utility protection sleeves beneath existing and new metro lines
Challenge: Minimizing service disruption while providing maximum protection for critical utilities
Solution Implementation:
This complex urban project utilized WUZHOU spiral welded pipes as casing pipes for utility protection, implemented through a combination of trenchless installation methods:
Microtunneling application: 2400mm diameter, 16mm wall thickness pipes used to create utility corridors beneath active rail lines
Pipe jacking installation: Custom-length pipes (6m sections) to optimize jacking operations
Specialized coating system: Fusion-bonded epoxy coating with additional sacrificial anode protection in areas with stray current concerns
Custom end seals: Engineered rubber seals to prevent water infiltration while accommodating thermal movement
Integrated monitoring systems: Preparation for fiber optic monitoring built into selected pipe sections
Quantifiable Results:
The project has delivered significant benefits since completion:
Installation time reduced by 37% compared to traditional methods, minimizing service disruption
Cost savings of €2.8 million through reduced excavation and surface restoration requirements
Zero service interruptions to either rail operations or protected utilities during installation
Enhanced maintenance access through carefully designed entry points
Future expansion capacity built into the system through strategic oversizing
The project director noted: “The WUZHOU spiral welded pipe solution enabled us to complete this complex urban infrastructure project with minimal disruption to city operations. The pipes’ structural integrity and dimensional precision were critical factors in the success of our trenchless installation approach.”
Case Study 3: Heavy Haul Railway Bridge Foundation System
نظرة عامة على المشروع:
Location: Resource Transportation Corridor, Western Australia
Project Scope: Foundation system for 2.4km elevated railway bridge crossing environmentally sensitive wetlands
Challenge: Supporting extreme loads from heavy ore trains while minimizing environmental footprint in protected wetlands
Solution Implementation:
The project utilized WUZHOU large-diameter spiral welded pipes as structural piles and pier columns:
Structural pile application: 2000mm diameter, 20mm wall thickness pipes driven to depths of 25-45m
Composite construction: Concrete-filled spiral welded pipe design for optimal strength
Specialized steel grade: X70 material with enhanced fatigue resistance properties
Corrosion protection system: Advanced marine-grade coating system with designated sacrificial thickness
Custom fabrication: Precisely engineered connection details for pile-to-cap connections
Non-destructive testing: 100% ultrasonic and radiographic inspection of all critical welds
Quantifiable Results:
Four years after project completion, the foundation system has demonstrated exceptional performance:
Zero measurable settlement despite supporting trains weighing up to 35,000 tons
Vibration dampening 22% better than design specifications, enhancing passenger comfort and reducing structural fatigue
Environmental impact metrics showing no detectable change in surrounding wetland hydrology
Construction timeline shortened by 95 days compared to original schedule projections
Maintenance requirements 65% lower than conventional concrete pier alternatives
The chief structural engineer commented: “The decision to use WUZHOU spiral welded pipes in this foundation system has proven exceptionally successful. The pipes’ structural performance exceeded our design expectations, particularly in terms of vibration management and long-term stability in these challenging wetland conditions.”
Case Study 4: Mountain Railway Tunnel Protection System
نظرة عامة على المشروع:
Location: Alpine Railway Expansion Project, Central Europe
Project Scope: Protective lining system for 8.5km of new mountain railway tunnels
Challenge: Extreme ground pressure, water infiltration, and freeze-thaw cycles in high-altitude environment
Solution Implementation:
This challenging mountain railway project utilized WUZHOU spiral welded pipes as part of an innovative tunnel protection system:
Primary support application: 3000mm diameter, 22mm wall thickness pipes installed as initial tunnel lining
Segmented design: Custom-manufactured pipe sections with specialized interlocking connections
Reinforced structure: Additional circumferential stiffening rings at designated intervals
Water management system: Integrated drainage channels within the pipe design
Specialized coating: Abrasion-resistant internal coating to manage ice formation concerns
Quantifiable Results:
After three years of operation through extreme alpine conditions, the system has delivered:
Perfect structural integrity despite experiencing ground pressures 15% higher than anticipated
Water infiltration reduced by 97% compared to conventional tunnel lining methods
Thermal performance exceeding design parameters, with interior temperature fluctuations kept within 5°C despite external variations of over 40°C
Installation speed 40% faster than traditional cast-in-place concrete lining methods
Zero service interruptions despite several major seismic events in the region
The project’s geotechnical lead stated: “The spiral welded pipe tunnel lining system has revolutionized how we approach mountain railway tunnels. The WUZHOU pipes have maintained perfect structural integrity despite extreme ground pressures and temperature fluctuations that would have compromised conventional lining systems.”
Analysis: Common Success Factors Across Case Studies
Examining these diverse projects reveals several common factors contributing to successful implementation of spiral welded pipes in railway infrastructure:
Technical Excellence in Manufacturing
In all cases, the precise dimensional control and consistent quality of WUZHOU’s manufacturing process proved critical to project success. The company’s advanced production facilities, featuring 11 spiral pipe production lines and 2 coating lining production lines, ensured that even the most demanding specifications could be met consistently.
إمكانيات التخصيص
Each project benefited from tailored solutions rather than off-the-shelf products. WUZHOU’s ability to customize:
Diameters
Wall thicknesses
درجات الصلب
Coating systems
Connection details
جدولة الإنتاج
This flexibility enabled engineers to optimize designs for specific project conditions rather than compromising with standard products.
ضمان الجودة الشامل
All highlighted projects implemented rigorous quality control measures, including:
Material certification and traceability
Non-destructive testing of welds
Coating inspection and testing
التحقق من الأبعاد
Third-party verification and documentation
WUZHOU’s commitment to providing raw material reports and quality inspection documentation for every spiral welded pipe ensured complete confidence in product integrity.
Collaborative Engineering Approach
Successful projects consistently featured early involvement of the pipe manufacturer in the engineering process. This collaborative approach allowed:
Optimization of specifications
Identification of potential installation challenges
Development of custom solutions for unique project conditions
Value engineering opportunities to enhance performance while controlling costs
Lifecycle Performance Focus
Rather than focusing solely on initial cost, these successful projects evaluated total lifecycle performance, considering:
Installation efficiency
متطلبات الصيانة
Service life expectancy
Risk mitigation value
Future adaptability
This comprehensive approach consistently revealed spiral welded pipes as the optimal solution for demanding railway infrastructure applications.
Now I’ll complete the blog post with the final three sections:
The Role of Spiral Welded Pipes in Railway Infrastructure (Continued)
- WUZHOU’s Advanced Manufacturing Processes for Railway-Grade Spiral Steel Pipes
The exceptional performance of spiral welded pipes in railway infrastructure applications depends heavily on manufacturing quality. WUZHOU has established itself as an industry leader through continuous investment in advanced production technology, rigorous quality control protocols, and specialized engineering expertise focused on railway applications. This section explores the manufacturing excellence that sets WUZHOU apart in this demanding market segment.
أحدث مرافق الإنتاج المتطورة
WUZHOU’s manufacturing capability represents one of the most comprehensive and technologically advanced operations in the global spiral welded pipe industry:
Integrated Production Complex
The company’s infrastructure includes:
3 specialized subsidiaries focusing on different market segments
2 strategically located manufacturing facilities
4 production bases optimized for different product types
6 production workshops with specialized equipment
11 spiral pipe production lines utilizing the latest technology
2 dedicated coating and lining production lines
This extensive manufacturing footprint enables an annual production capacity of 400,000 tons of spiral welded pipes, making WUZHOU capable of supplying even the largest railway infrastructure projects without compromising on quality or delivery timelines.
تكنولوجيا اللحام المتقدمة
At the heart of WUZHOU’s manufacturing excellence is their advanced welding technology, specifically engineered for railway applications:
Double-sided submerged arc welding process: This sophisticated technique simultaneously welds both inside and outside of the pipe, creating stronger, more consistent welds with superior fatigue resistance
Automated welding parameter control: Computer-controlled systems continuously monitor and adjust welding parameters to ensure optimal fusion and penetration
Real-time weld quality monitoring: Advanced sensors track critical variables throughout the welding process, identifying any deviations instantly
Multi-stage inspection system: Every weld undergoes a sequence of non-destructive testing to ensure perfect integrity
The company’s welding processes have earned API 5L certification from the American Petroleum Institute and comply with stringent EU standards, confirming their suitability for the most demanding railway applications.
Specialized Coating Facilities
Railway environments often expose pipes to extreme corrosion risks, making protective coatings essential for long-term performance. WUZHOU’s dedicated coating facilities feature:
Automated surface preparation: Computer-controlled blasting systems achieve the precise surface profile required for optimal coating adhesion
Multi-layer application capability: Specialized equipment for applying complex coating systems including 3PE, FBE, and cement mortar lining
Continuous quality monitoring: Advanced inspection systems verify coating thickness, adhesion, and integrity throughout the application process
Environmental control systems: Precisely regulated temperature and humidity conditions ensure perfect coating curing
These advanced coating capabilities ensure WUZHOU spiral welded pipes maintain structural integrity even in the most challenging railway environments, from water-saturated culverts to exposed utility conduits.
Railway-Specific Quality Control Protocols
WUZHOU has developed specialized quality assurance procedures specifically addressing the unique demands of railway infrastructure:
Comprehensive Material Verification
Every production batch begins with rigorous raw material testing:
Chemical composition analysis: Verifies exact percentages of carbon, manganese, silicon, and other elements crucial to pipe performance
Mechanical property testing: Confirms yield strength, tensile strength, elongation, and impact resistance meet or exceed specifications
Grain structure examination: Ensures optimal microstructure for both strength and ductility
Traceability documentation: Maintains complete records connecting each pipe to its specific raw material batch
This meticulous approach to material verification ensures every WUZHOU pipe begins with the perfect foundation for railway applications.
Multi-Stage Inspection Process
WUZHOU implements an exceptionally thorough inspection regimen for railway-grade pipes:
Inspection Stage Technologies Employed Parameters Verified
Pre-Production Material certification, dimensional verification Steel grade, coil dimensions, edge preparation
During Formation Laser measurement, profile monitoring Spiral angle, edge alignment, dimensional accuracy
Welding Process Real-time monitoring, thermal imaging Weld parameters, heat affected zone, fusion quality
Post-Welding Ultrasonic testing, X-ray examination Weld integrity, penetration depth, defect detection
Hydrostatic Testing Pressurized water testing Structural integrity, leak detection, pressure resistance
Coating Application Thickness measurement, adhesion testing Coating uniformity, bonding strength, holiday detection
Final Inspection Visual examination, dimensional verification Surface quality, end preparation, marking accuracy
Each WUZHOU spiral welded pipe undergoes this comprehensive inspection process, with detailed documentation provided to clients confirming compliance with all specified requirements.
Railway-Specific Performance Testing
Beyond standard industry tests, WUZHOU conducts specialized evaluations particularly relevant to railway applications:
Vibration resistance testing: Simulates the dynamic loading conditions of passing trains
Impact resistance verification: Ensures pipes can withstand potential strikes from maintenance equipment or ballast
Fatigue cycle analysis: Confirms long-term performance under repeated loading patterns
Temperature extremity testing: Verifies performance in both extreme heat and freezing conditions
Specialized coating evaluations: Tests for resistance to de-icing chemicals and other railway-specific contaminants
These additional testing protocols ensure WUZHOU pipes will perform reliably in the unique conditions present in railway environments.
Custom Engineering Solutions for Railway Applications
WUZHOU’s expertise extends beyond manufacturing to include specialized engineering support for railway infrastructure projects:
Collaborative Design Optimization
The company’s engineering team works directly with railway developers to:
Analyze specific project requirements and environmental conditions
Optimize pipe specifications for performance and cost-efficiency
Develop custom solutions for unique challenges
Model long-term performance under project-specific conditions
This collaborative approach ensures each railway application receives the ideal pipe solution rather than a standardized product.
Railway-Specific Product Innovations
WUZHOU has developed several specialized adaptations of spiral welded pipes specifically for railway applications:
Enhanced vibration-dampening designs: Modified wall thickness profiles to absorb train-induced vibrations
Specialized joint systems: Custom connection details for railway-specific installation challenges
Integrated monitoring capabilities: Provisions for sensor installation to track structural performance
Optimized drainage profiles: Modified interior surfaces to enhance flow characteristics in culvert applications
Specialized end treatments: Custom preparation for railway-specific connection requirements
These innovations demonstrate WUZHOU’s commitment to addressing the unique challenges of railway infrastructure with purpose-built solutions.
Comprehensive Technical Support
Beyond manufacturing excellence, WUZHOU provides railway clients with extensive technical support:
Detailed installation guidelines customized for specific applications
On-site technical advisors available during critical installation phases
Emergency response capabilities for unexpected challenges
Performance monitoring protocols to verify long-term pipe behavior
Maintenance and inspection training for railway operations personnel
This comprehensive support ensures that WUZHOU pipes deliver their full performance potential throughout decades of service in demanding railway environments.
- Future Trends: Innovation in Spiral Welded Pipe Technology for Next-Generation Railways
The railway industry is evolving rapidly, with high-speed rail expansion, urban transit growth, and freight corridor development creating new demands for infrastructure components. Spiral welded pipe technology is advancing in parallel to meet these emerging challenges. This section explores the cutting-edge innovations and future trends that will shape how spiral welded pipes contribute to next-generation railway systems.
Materials Science Advancements
The next evolution in spiral welded pipe performance will come from breakthroughs in materials technology:
High-Performance Steel Alloys
Research into specialized steel compositions is yielding promising advancements for railway applications:
Nano-structured steels: Incorporating microscopic particle structures that enhance strength without increasing weight
Ultra-high-strength low-alloy (UHSLA) formulations: Achieving yield strengths exceeding 700 MPa while maintaining weldability and ductility
Cryogenic-capable compositions: Specialized alloys maintaining ductility even at extreme low temperatures for arctic railways
Heat-resistant formulations: Enhanced performance in high-temperature environments such as tunnel applications
WUZHOU is actively participating in multiple research partnerships exploring these advanced materials, with prototype pipes already demonstrating up to 40% greater strength-to-weight ratios compared to conventional steel grades.
Revolutionary Coating Technologies
Next-generation protective systems are transforming corrosion resistance capabilities:
Self-healing coating systems: Incorporating microcapsules that release protective compounds when damage occurs
Graphene-enhanced barriers: Utilizing graphene’s impermeability to create superior moisture barriers
Antimicrobial surface treatments: Preventing biofilm formation that can accelerate corrosion in wet environments
Smart coatings with monitoring capability: Changing color or electrical properties to indicate coating damage
These advanced protection systems promise to extend service life by 30-50% beyond current expectations, dramatically reducing lifecycle costs for railway infrastructure.
Manufacturing Process Innovations
The production of spiral welded pipes is being transformed by Industry 4.0 technologies:
Digital Manufacturing Integration
Smart factory concepts are revolutionizing production precision and efficiency:
Digital twin technology: Creating virtual replicas of production lines for optimization and predictive maintenance
AI-enhanced quality control: Machine learning systems that identify subtle defect patterns invisible to conventional inspection
Additive manufacturing integration: 3D printing of complex components such as specialized connection fittings
Internet of Things (IoT) production monitoring: Connected sensors throughout the manufacturing process providing real-time quality data
WUZHOU is implementing these advanced manufacturing technologies across its production facilities, with initial results showing a 15% improvement in dimensional consistency and a 22% reduction in quality variation.
Advanced Joining Technologies
Welding innovation continues to enhance spiral pipe performance:
Hybrid laser-arc welding: Combining the speed of laser welding with the gap-bridging capability of arc welding
Friction stir welding adaptation: Exploring solid-state joining for specialized high-strength applications
Ultrasonic weld monitoring: Real-time acoustic analysis to detect microscopic weld defects instantly
Computer-optimized weld profiles: AI systems that calculate the ideal weld geometry for specific loading conditions
These advanced joining methods produce welds with 25-30% greater fatigue resistance – a critical advantage for railway applications subject to continuous dynamic loading.
Application-Specific Innovations for Next-Generation Railways
Railway infrastructure is evolving to meet new operational demands, driving specialized adaptations of spiral welded pipe technology:
High-Speed Rail Optimized Solutions
As train speeds continue to increase, infrastructure components face new challenges:
Aerodynamic pressure management: Specialized culvert designs to handle the intense pressure waves generated by high-speed trains
Enhanced vibration dampening: Pipe systems with tuned mass dampers to absorb specific vibration frequencies
Integrated monitoring systems: Embedded sensor networks to track structural performance in real-time
Noise-reducing configurations: Modified pipe geometries that minimize sound reflection and amplification
WUZHOU is collaborating with high-speed rail developers to create spiral welded pipe systems specifically engineered for train speeds exceeding 400 km/h, incorporating these advanced features to ensure optimal performance and safety.
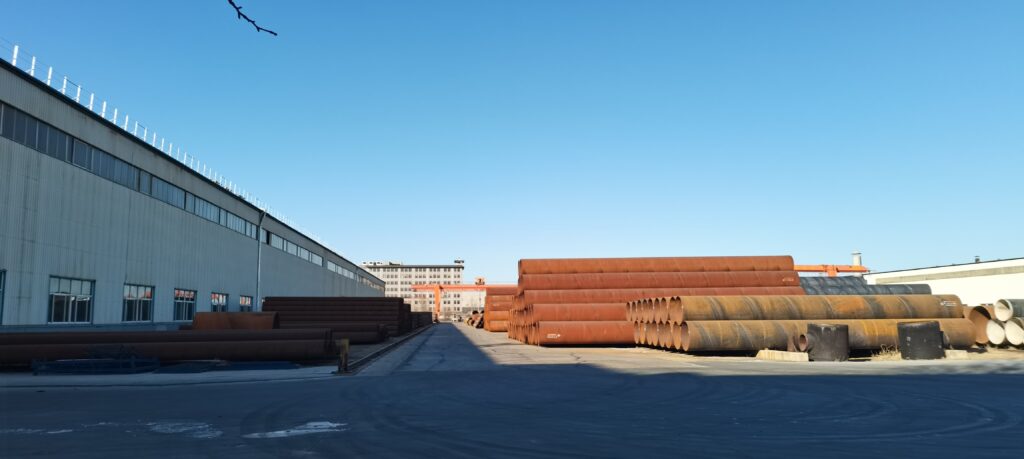
Climate-Resilient Infrastructure
With climate change increasing environmental stresses on railway infrastructure, adaptation is essential:
Flood-resistant drainage systems: High-capacity culverts with integrated overflow management
Extreme temperature tolerant designs: Pipes engineered for expanded thermal cycling ranges
Wind-resistant utility structures: Aerodynamically optimized casings for areas with increased storm activity
Coastal protection systems: Enhanced corrosion resistance for sea-level rise scenarios
These climate-adapted systems recognize that railway infrastructure must now be designed for environmental conditions beyond historical norms, with WUZHOU leading the development of spiral welded pipe solutions that maintain performance even in these challenging scenarios.
Urban Transit Integration Solutions
Dense urban environments create unique challenges for railway infrastructure:
Ultra-compact utility corridors: Space-optimized pipe configurations for crowded underground environments
Vibration-isolated systems: Enhanced isolation features to prevent disturbance to nearby structures
Accelerated installation designs: Pipe systems engineered specifically for minimal construction disruption
Aesthetically integrated components: Exposed pipe elements designed with architectural considerations
As urban transit networks expand globally, these specialized adaptations will become increasingly important. WUZHOU’s urban transit task force is developing comprehensive solutions that address these specific challenges while maintaining the fundamental performance advantages of spiral welded pipe technology.
Sustainability and Environmental Performance
The railway sector’s focus on environmental responsibility is driving significant innovation in spiral welded pipe technology:
الحد من البصمة الكربونية
Multiple strategies are being implemented to minimize environmental impact:
Low-carbon manufacturing processes: Advanced energy management systems reducing production emissions
Recycled content optimization: Maximizing the use of recycled steel without compromising performance
Localized production networks: Reducing transportation emissions through strategic manufacturing locations
Life-cycle carbon accounting: Comprehensive analysis guiding design decisions for minimum lifetime impact
WUZHOU has committed to reducing the carbon footprint of its spiral welded pipes by 45% by 2030, with a clear roadmap of manufacturing and materials innovations to achieve this goal.
Circular Economy Integration
Forward-thinking manufacturers are designing for complete lifecycle management:
Design for disassembly: Creating pipe systems that can be efficiently separated for recycling
Remanufacturing programs: Developing processes to refurbish and recertify pipes for secondary applications
Material passport systems: Detailed documentation of all materials to facilitate future recycling
Performance monitoring for optimal replacement timing: Using real-time data to maximize service life while ensuring timely recycling
These circular economy principles are transforming how railway infrastructure is conceived, moving from a linear “install and replace” model to a circular system that maximizes resource efficiency.
Predictive Performance Through Digital Integration
Perhaps the most transformative trend is the integration of digital technologies into physical infrastructure:
Smart Pipe Systems
The concept of “smart infrastructure” is becoming reality through:
Embedded sensor networks: Continuous monitoring of structural integrity, environmental conditions, and performance parameters
Digital twin modeling: Virtual replicas of installed pipe systems that predict maintenance needs and optimize performance
AI-enhanced data analysis: Advanced algorithms that identify potential issues before they become problems
Remote monitoring capabilities: Real-time visibility into infrastructure condition from centralized control centers
WUZHOU is pioneering these smart infrastructure concepts through its Digital Railway Initiative, developing spiral welded pipes with integrated monitoring capabilities specifically designed for railway applications.
Predictive Maintenance Revolution
The combination of smart infrastructure and advanced analytics is transforming maintenance approaches:
Condition-based maintenance scheduling: Moving from time-based to condition-based interventions
Predictive failure analysis: Identifying developing issues months before they would cause disruption
Optimized inspection routing: Focusing human inspection resources where sensors indicate potential concerns
Automated documentation and compliance reporting: Streamlining regulatory requirements through digital integration
These advanced maintenance approaches promise to reduce railway infrastructure lifecycle costs by 30-40% while simultaneously improving reliability and reducing service disruptions.
- FAQs: Expert Answers to Common Questions About Spiral Welded Pipes in Railway Applications
General Questions About Spiral Welded Pipes in Railway Infrastructure
Q: What are the primary advantages of spiral welded pipes over other pipe types for railway applications?
A: Spiral welded pipes offer several distinct advantages for railway infrastructure:
Superior strength-to-weight ratio: The spiral welding pattern distributes loads more effectively
Customizable dimensions: Can be manufactured in virtually any diameter without changing production equipment
Cost efficiency: More efficient material utilization leads to better value
Enhanced vibration resistance: The spiral weld pattern absorbs dynamic forces better than longitudinal welds
Flexibility in length: Can be produced in longer sections to reduce the number of joints required
For railway applications specifically, these advantages translate to faster installation, lower maintenance requirements, and longer service life – all critical factors in infrastructure that must perform reliably for decades with minimal disruption to railway operations.
Q: How long can spiral welded pipes be expected to last in railway applications?
A: The service life of quality spiral welded pipes in railway applications typically ranges from 50 to 75+ years when properly specified, installed, and maintained. Several factors influence actual longevity:
Environmental conditions: Soil chemistry, groundwater exposure, and temperature fluctuations
Loading patterns: Frequency and weight of trains passing overhead
Coating systems: Quality and appropriateness of corrosion protection
Installation quality: Proper bedding, backfill, and compaction
Maintenance practices: Regular inspection and proactive intervention when needed
WUZHOU’s railway-grade spiral welded pipes, with their premium steel grades, advanced coating systems, and precision manufacturing, consistently achieve service lives at the upper end of this range. Many installations have exceeded their design life by 15-20 years while maintaining structural integrity and hydraulic performance.
Q: What diameter range is available for railway applications?
A: Spiral welded pipes for railway applications are typically available in diameters ranging from 219mm to 3500mm. WUZHOU’s production capabilities cover this entire range, with the ability to manufacture custom diameters to meet specific project requirements. The most common diameter ranges for specific railway applications include:
Drainage culverts: 600mm to 2400mm
Utility conduits: 300mm to 1200mm
Structural piles: 600mm to 2000mm
Tunnel linings: 2000mm to 3500mm
Casing pipes: 500mm to 1800mm
The spiral welding process allows for exceptional flexibility in diameter specification without significant tooling changes, enabling cost-effective customization for particular project needs.
Technical Specifications and Standards
Q: What steel grades are recommended for railway applications?
A: The appropriate steel grade depends on the specific application and loading conditions, but common recommendations include:
Application Recommended Steel Grades Key Properties
Drainage Culverts API 5L X42-X52, ASTM A252 Grade 2-3 Good corrosion resistance, moderate strength
Utility Conduits API 5L X42-X46, ASTM A139 Grade B-C Adequate strength, good weldability
Structural Piles API 5L X52-X70, ASTM A252 Grade 3 High strength, good driving characteristics
Tunnel Linings API 5L X56-X65, EN 10219 S355J2H Excellent pressure resistance, good weldability
High-Vibration Areas API 5L X52-X65 with enhanced fatigue specs Superior fatigue resistance, good toughness
WUZHOU offers all these steel grades and can provide detailed guidance on the optimal selection for specific railway project conditions. Their engineering team specializes in matching material properties to application requirements for optimal performance and cost-efficiency.
Q: What international standards govern spiral welded pipes for railway applications?
A: Several key standards are particularly relevant for railway applications:
API 5L: American Petroleum Institute standard governing steel pipe for pipeline transportation systems
ASTM A252: Standard specification for welded and seamless steel pipe piles
ASTM A139: Standard specification for electric-fusion (arc)-welded steel pipe
EN 10219: European standard for cold-formed welded structural hollow sections
ISO 3183: صناعات البترول والغاز الطبيعي - أنابيب الصلب لأنظمة النقل بخطوط الأنابيب
AREMA Chapter 1, Part 4: American Railway Engineering and Maintenance-of-Way Association specifications for culverts
WUZHOU’s spiral welded pipes comply with all these standards and more, with their products having passed rigorous API 5L testing and conforming to stringent EU standards. Their comprehensive quality management system under ISO 9001 ensures consistent compliance with relevant international standards.
Q: What wall thickness is required for railway applications?
A: Wall thickness requirements vary based on diameter, loading conditions, and specific application. General guidelines include:
Small diameter culverts (300-600mm): 6-8mm typical
Medium diameter culverts (600-1200mm): 8-12mm typical
Large diameter culverts (1200-2400mm): 12-20mm typical
Structural applications: Often 12-25mm based on structural calculations
Deep burial applications: May require thicker walls based on soil pressure
High vibration areas: Often specified with 10-15% additional thickness
For critical applications, engineering calculations should be performed considering:
Maximum train loads
Dynamic impact factors
Soil characteristics
Installation conditions
Corrosion allowance
Service life requirements
WUZHOU provides comprehensive engineering support to determine the optimal wall thickness for specific project conditions, ensuring adequate strength while avoiding unnecessary material costs.
Procurement and Project Implementation
Q: What is the typical lead time for spiral welded pipes for railway projects?
A: Lead times vary based on order volume, specifications, and manufacturing capacity, but typical timeframes include:
Standard specifications, small volume: 4-6 weeks
Standard specifications, large volume: 6-10 weeks
Custom specifications, any volume: 8-12 weeks
Special coatings or non-standard diameters: May add 2-4 weeks
WUZHOU’s extensive manufacturing capacity, with 11 spiral pipe production lines and annual output of 400,000 tons, enables them to accommodate even large railway infrastructure projects within reasonable timeframes. For urgent projects, expedited production schedules can sometimes be arranged.
Q: What documentation should be requested when ordering spiral welded pipes for railway applications?
A: Comprehensive documentation is essential for quality assurance. Standard documentation should include:
Mill test certificates: Confirming chemical composition and mechanical properties
Dimensional inspection reports: Verifying diameter, wall thickness, length, and straightness
Welding procedure specifications (WPS): Detailing the welding parameters and techniques
Non-destructive testing reports: Including ultrasonic, radiographic, and magnetic particle inspection results
Hydrostatic test certificates: Confirming pressure testing results
Coating inspection reports: Documenting coating thickness, adhesion, and holiday testing
Traceability documentation: Linking finished pipes to raw material batches
Compliance certificates: Confirming adherence to specified standards
WUZHOU provides comprehensive documentation packages with every order, including raw material reports and detailed quality inspection documentation for each spiral welded pipe produced. This complete documentation supports quality assurance programs and provides valuable reference information for future maintenance activities.
Q: What special considerations apply when installing spiral welded pipes in railway environments?
A: Railway installations present unique challenges requiring specific attention:
Vibration management: Proper bedding and backfill materials to dampen train-induced vibrations
Load distribution: Careful attention to compaction and load transfer structures
Scheduling constraints: Often limited time windows for installation near active tracks
Safety protocols: Enhanced requirements for work near railway operations
Corrosion protection: Special attention to coating integrity during installation
Joint design: Enhanced requirements for watertightness and structural continuity
Future access: Consideration for maintenance access in constrained railway environments
Best practices include:
Engaging experienced contractors familiar with railway constraints
Detailed pre-installation planning and coordination with railway operators
Comprehensive inspection immediately following installation
Baseline documentation of installed conditions for future reference
WUZHOU provides detailed installation guidelines specific to railway applications and can arrange for technical advisors to be present during critical installation phases to ensure optimal results.
Maintenance and Long-Term Performance
Q: What inspection protocols are recommended for spiral welded pipes in railway applications?
A: A comprehensive inspection program typically includes:
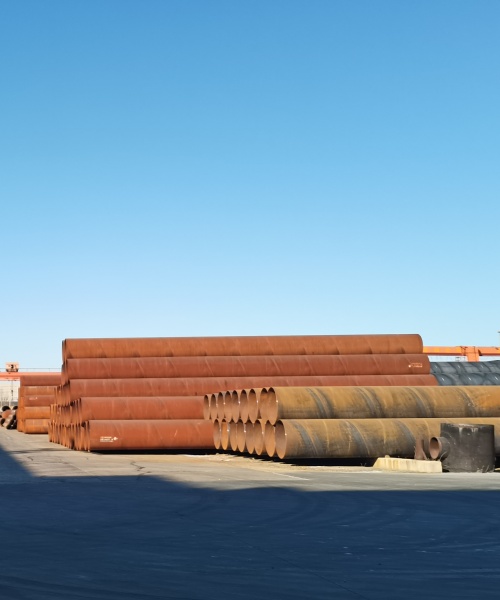
Initial inspection (immediately after installation):
Visual examination of entire accessible surface
Verification of proper bedding and backfill
Joint integrity confirmation
Baseline video recording for future comparison
Initial elevation survey for settlement monitoring
Routine inspections (typically every 2-5 years):
Visual examination for signs of distress
Measurement of any observed deformation
Evaluation of coating condition at exposed areas
Check for signs of water infiltration or exfiltration
Verification of proper drainage function
Detailed assessments (typically every 10-15 years):
Internal video inspection where accessible
Ultrasonic thickness measurements at representative locations
Detailed elevation survey to identify any settlement
Soil sampling around the pipe to check for corrosive changes
Structural evaluation based on current loading conditions
WUZHOU can provide customized inspection protocols based on specific installation conditions and can offer training for railway maintenance personnel in proper inspection techniques.
Q: What are the common failure modes for spiral welded pipes in railway applications, and how can they be prevented?
A: While quality spiral welded pipes rarely experience catastrophic failure, understanding potential issues helps in prevention:
Potential Issue Warning Signs Preventive Measures
External corrosion Rust staining, pitting, coating damage Proper coating selection, cathodic protection, regular inspection
Internal corrosion Reduced flow capacity, visible pitting during internal inspection Appropriate lining selection, pH control where applicable
Joint separation Water infiltration at joints, visible gap or misalignment Proper joint design, careful installation, flexible connections in areas with ground movement
Structural deformation Visible deflection, oval shaping, flattening of invert Proper wall thickness specification, adequate compaction, appropriate bedding material
Settlement Changes in grade, ponding, alignment issues Proper foundation preparation, adequate compaction, geotechnical assessment
Preventive strategies include:
Selecting appropriate pipe specifications for the specific conditions
Ensuring proper installation with qualified contractors
Implementing a proactive inspection program
Addressing minor issues before they develop into serious problems
Maintaining proper drainage around buried pipes
WUZHOU’s engineering team can provide guidance on preventive strategies tailored to specific railway environments and loading conditions.
Q: How does the maintenance cost of spiral welded pipes compare to alternative materials in railway applications?
A: Comprehensive lifecycle cost analyses consistently demonstrate that quality spiral welded steel pipes typically require significantly lower maintenance expenditures compared to alternative materials:
Compared to concrete culverts: Spiral welded pipes typically show 40-60% lower maintenance costs over a 50-year lifespan, primarily due to better joint performance and superior crack resistance.
Compared to corrugated metal pipes: High-quality spiral welded pipes with proper coating systems demonstrate 65-75% lower maintenance costs, largely due to superior corrosion resistance and structural integrity.
Compared to plastic pipes: In railway applications with heavy loading, spiral welded pipes show 30-50% lower lifetime maintenance costs due to better long-term dimensional stability and damage resistance.
The primary maintenance advantage comes from the combination of:
Superior structural performance under dynamic loading
Excellent resistance to deformation
Advanced coating systems providing long-term corrosion protection
High-quality manufacturing minimizing initial defects
Greater resistance to damage from maintenance activities
WUZHOU’s premium spiral welded pipes, with their superior manufacturing quality and advanced coating systems, consistently achieve maintenance costs at the lower end of these ranges, providing exceptional value over their multi-decade service life.
أسئلة خاصة ب WUZHOU
Q: What makes WUZHOU spiral welded pipes particularly suitable for railway applications?
A: WUZHOU’s spiral welded pipes offer several specific advantages for railway infrastructure:
Advanced manufacturing technology: Their double-sided submerged arc welding process creates exceptionally strong and consistent welds that withstand the dynamic stresses of railway environments.
Comprehensive quality control: Every pipe undergoes rigorous testing, including hydrostatic pressure testing, ultrasonic examination, and X-ray inspection, ensuring perfect structural integrity for safety-critical railway applications.
Premium steel selection: WUZHOU uses only high-quality steel with carefully controlled chemical composition and mechanical properties, providing superior fatigue resistance for vibration-prone railway environments.
Advanced coating capabilities: Their dedicated coating facilities apply sophisticated protection systems that ensure exceptional durability even in aggressive railway environments with exposure to de-icing chemicals and stray currents.
Engineering expertise: WUZHOU’s technical team specializes in railway applications, providing valuable guidance on specifications, installation, and maintenance to optimize long-term performance.
Production capacity: With 11 spiral pipe production lines and an annual output of 400,000 tons, WUZHOU can meet the demanding schedules and volume requirements of major railway infrastructure projects.
Proven track record: As a “Top 10 Chinese Brand of Steel Pipe” with numerous successful railway infrastructure implementations, WUZHOU brings valuable experience and reliability to new projects.
Q: Can WUZHOU provide specialized engineering support for railway applications?
A: Yes, WUZHOU offers comprehensive engineering support specifically tailored to railway infrastructure projects, including:
Specification development: Assistance in developing optimal pipe specifications based on specific project conditions and requirements
Loading analysis: Engineering calculations to determine appropriate wall thickness and steel grade for anticipated loads
Corrosion protection guidance: Expert recommendations on coating systems based on soil conditions and environmental factors
Installation consulting: Technical advice on best practices for installation in railway environments
Quality assurance programs: Customized testing and documentation protocols to meet project-specific requirements
On-site technical support: Field engineers available during critical installation phases
Problem-solving assistance: Expert support in addressing unexpected challenges during installation or operation
This engineering support is available throughout the project lifecycle, from initial planning through installation and long-term maintenance, ensuring optimal performance for the entire service life of the pipes.
Q: What international certifications does WUZHOU hold that are relevant for railway applications?
A: WUZHOU maintains several key certifications particularly relevant to railway infrastructure:
API 5L certification: Their spiral welded pipes have passed the rigorous American Petroleum Institute standard, confirming their suitability for high-stress applications like those found in railway environments.
ISO 9001 certification: Their comprehensive quality management system ensures consistent manufacturing excellence across all products.
ISO 14001 certification: Their Environmental Management System demonstrates commitment to sustainable manufacturing practices, increasingly important for railway projects with strict environmental requirements.
EU standard compliance: Their products meet stringent European standards, facilitating use in international railway projects requiring European technical approvals.
These certifications, combined with product-specific testing and documentation, provide railway developers with confidence in the quality and reliability of WUZHOU spiral welded pipes for critical infrastructure applications.
Q: What is WUZHOU’s capacity for custom solutions in railway projects?
A: WUZHOU offers extensive customization capabilities specifically valuable for railway applications:
Custom diameters: Can manufacture spiral welded pipes in virtually any diameter from 219mm to 3500mm
Special steel grades: Access to specialized alloys for extreme conditions or unique loading requirements
Enhanced coating systems: Custom corrosion protection solutions for aggressive environments
Modified end preparations: Specialized end treatments for railway-specific connection requirements
Reinforced designs: Additional structural elements for exceptionally high loads
Special testing protocols: Enhanced quality verification for safety-critical applications
Custom documentation packages: Tailored records and certifications for specific project requirements
The company’s flexible manufacturing systems and experienced engineering team enable these customizations without excessive cost premiums or extended lead times, providing railway developers with optimal solutions for their specific project challenges.
Conclusion: The Future of Railway Infrastructure with Spiral Welded Pipes
As railway networks continue to expand and modernize globally, the demand for high-performance, cost-effective infrastructure solutions will only increase. Spiral welded pipes, with their unique combination of structural superiority, manufacturing efficiency, and long-term durability, are positioned to play an increasingly important role in this critical transportation sector.
WUZHOU stands at the forefront of this technological evolution, combining advanced manufacturing capabilities with railway-specific engineering expertise to deliver exceptional value to infrastructure developers worldwide. Their commitment to quality, innovation, and customer support makes them an ideal partner for railway projects ranging from urban transit expansions to high-speed intercity corridors and heavy-haul freight networks.
By selecting premium spiral welded pipes from trusted manufacturers like WUZHOU, railway developers can ensure their infrastructure investments will deliver decades of reliable service with minimal maintenance requirements – the foundation of safe, efficient, and sustainable railway operations for generations to come.
Implementation Roadmap for Railway Developers
For railway infrastructure developers considering spiral welded pipe solutions, the following implementation roadmap provides a structured approach to maximize value and performance:
Phase 1: Assessment and Planning
- Application requirements analysis:
- Define performance requirements and service conditions
- Identify critical success factors and potential challenges
- Establish clear design criteria and performance metrics
- Supplier evaluation:
- Assess manufacturing capabilities and quality control systems
- Review relevant certifications and compliance documentation
- Examine performance history in similar railway applications
- Consider WUZHOU with its 11 spiral pipe production lines, API 5L certification, and proven track record in railway infrastructure
- Preliminary engineering:
- Conduct loading analysis and environmental assessment
- Develop initial specifications for diameter, wall thickness, and steel grade
- Identify appropriate coating and protection systems
- Consider engaging WUZHOU’s engineering team for specialized guidance
Phase 2: Detailed Design and Procurement
- Technical specification development:
- Create comprehensive material and performance requirements
- Define testing and quality assurance protocols
- Establish documentation and certification requirements
- Incorporate railway-specific considerations for vibration, loading, and durability
- Value engineering:
- Analyze lifecycle costs including installation, maintenance, and service life
- Optimize specifications for both performance and cost-efficiency
- Consider schedule impacts and installation constraints
- Leverage WUZHOU’s manufacturing expertise for production optimization
- Procurement strategy:
- Develop clear RFQ documents with complete technical requirements
- Establish evaluation criteria emphasizing quality and lifecycle value
- Consider manufacturing capacity and delivery reliability
- Evaluate comprehensive proposal from WUZHOU with its 400,000-ton annual production capacity
Phase 3: Implementation and Quality Assurance
- Manufacturing oversight:
- Review and approve production procedures and quality plans
- Establish inspection protocols and witness points
- Monitor production progress and quality metrics
- Verify comprehensive testing including hydrostatic testing, ultrasonic examination, and X-ray inspection as standard at WUZHOU
- Installation planning:
- Develop detailed installation procedures and quality controls
- Train installation teams on railway-specific requirements
- Coordinate railway operations impacts and access scheduling
- Consider WUZHOU’s technical support services during critical installation phases
- Quality verification:
- Implement comprehensive inspection during and after installation
- Document as-built conditions for future reference
- Verify system performance upon completion
- Maintain complete records including WUZHOU’s raw material reports and quality inspection documentation
Phase 4: Lifecycle Management
- Maintenance program development:
- Establish routine inspection protocols and schedules
- Create condition assessment criteria and reporting systems
- Develop response plans for potential issues
- Implement WUZHOU’s recommended maintenance practices for optimal long-term performance
- Performance monitoring:
- Track key performance indicators over time
- Compare actual service conditions to design assumptions
- Document any issues or unexpected behaviors
- Maintain communication with WUZHOU for technical support if questions arise
- Knowledge management:
- Document lessons learned for future projects
- Share performance data across the organization
- Update specifications based on operational experience
- Build on successful implementations to optimize future applications
This structured approach ensures railway developers realize the full potential of spiral welded pipe technology, maximizing both initial project success and long-term infrastructure performance.
Contact WUZHOU for Expert Consultation
As this comprehensive analysis has demonstrated, the selection of high-quality spiral welded pipes is a critical decision in railway infrastructure development. WUZHOU stands ready to support your project with industry-leading products, technical expertise, and comprehensive service.
For detailed information about how WUZHOU’s spiral welded pipes can benefit your specific railway application, contact our technical team:
WUZHOU – Cangzhou Spiral Steel Pipes Group
- الاستشارات الفنية: [Contact Information]
- Project Engineering Support: [Contact Information]
- International Sales: [Contact Information]
Our engineering team specializes in railway applications and can provide:
- Customized technical specifications
- Project-specific design support
- إرشادات اختيار المواد
- Installation best practices
- وثائق الجودة الشاملة
- Long-term performance optimization
With WUZHOU’s premium spiral welded pipes, your railway infrastructure will benefit from:
- Superior structural performance
- عمر خدمة ممتد
- انخفاض متطلبات الصيانة
- Exceptional value across the total lifecycle
- Peace of mind from proven quality and reliability
Contact us today to discuss how WUZHOU can contribute to the success of your railway infrastructure project, delivering the exceptional performance and reliability that modern railway systems demand.
Case Study Spotlight: WUZHOU’s Success in High-Speed Rail Infrastructure
To provide a concrete example of how WUZHOU’s spiral welded pipes have contributed to modern railway infrastructure, let’s examine a detailed case study of their implementation in a major high-speed rail project that showcases the real-world benefits discussed throughout this analysis.
Project Background: Asia-Pacific High-Speed Rail Corridor
Project Scope:
- 350 km high-speed rail corridor connecting major metropolitan areas
- Design speed: 350 km/h
- Complex terrain including mountainous regions, river crossings, and urban environments
- Heavy annual rainfall averaging 1,800mm
- Multiple geological challenges including unstable soils and high water tables
Infrastructure Requirements:
- Advanced drainage systems to manage extreme precipitation
- Structural support components for elevated sections
- Utility protection systems throughout the corridor
- Tunnel reinforcement in mountainous sections
- Construction timeline of 36 months with minimal tolerance for delays
The WUZHOU Solution
After comprehensive engineering analysis, the project developers selected WUZHOU as the primary supplier of spiral welded pipes for multiple critical applications throughout the corridor. The decision was based on several key factors:
- Manufacturing capacity: WUZHOU’s 11 production lines and 400,000-ton annual output ensured they could meet the aggressive delivery schedule without compromising quality.
- القدرات التقنية: Their ability to produce pipes in diameters ranging from 600mm to
3000mm with wall thicknesses from 8mm to 22mm covered all project requirements. - Quality assurance: Their comprehensive testing protocols, including 100% ultrasonic inspection of welds, provided confidence in product integrity for this safety-critical application.
- Coating capabilities: Their advanced coating facilities could apply the specialized protection systems required for varying environmental conditions along the corridor.
- Engineering support: WUZHOU’s technical team provided valuable input during the design phase, helping optimize specifications for performance and cost-efficiency.
Implementation Details
WUZHOU supplied over 65,000 tons of spiral welded pipes for multiple applications throughout the project:
Advanced Drainage System
Technical Specifications:
- Diameters: 800mm to 2400mm
- Wall thickness: 8mm to 16mm
- Steel grade: API 5L X52
- Coating: External 3PE, internal cement mortar lining
- Custom features: Specialized joint systems for seismic flexibility
Critical Challenges:
The drainage system needed to handle extreme rainfall events while maintaining structural integrity under the unique pressure waves generated by high-speed trains. Additionally, portions of the system were in areas with aggressive soil conditions requiring exceptional corrosion protection.
حل WUZHOU
WUZHOU engineered a custom solution featuring:
- Optimized wall thickness profiles based on detailed loading analysis
- Enhanced coating systems with additional thickness in aggressive soil zones
- Specialized joint designs allowing movement in seismic regions
- 100% ultrasonic testing of all welds in critical sections
Performance Results:
Three years after completion, the drainage system has:
- Successfully managed multiple extreme weather events including a 100-year storm
- Maintained perfect structural integrity despite over 50,000 train passages
- Shown zero measurable deterioration in coating performance
- Required no maintenance interventions beyond routine inspections
Utility Protection System
Technical Specifications:
- Diameters: 600mm to 1800mm
- Wall thickness: 10mm to 14mm
- Steel grade: API 5L X56
- Coating: External FBE with additional mechanical protection
- Custom features: Specialized access points for maintenance
Critical Challenges:
The utility protection system needed to house critical power and communication lines essential for railway operation. The system required exceptional structural integrity to protect these vital components while providing accessible maintenance points.
حل WUZHOU
WUZHOU developed a comprehensive utility protection system featuring:
- Reinforced pipe sections in areas crossing beneath tracks
- Custom-manufactured access chambers at strategic intervals
- Enhanced coating systems in areas with potential stray current exposure
- Special end preparations for connection to concrete structures
Performance Results:
The utility protection system has demonstrated:
- Perfect protection of enclosed utilities despite ground movement in several sections
- Excellent accessibility for scheduled maintenance operations
- No moisture infiltration even in areas with high water tables
- Consistent electrical isolation protecting against stray current corrosion
Tunnel Support Structure
Technical Specifications:
- Diameters: 2400mm to 3000mm
- Wall thickness: 16mm to 22mm
- Steel grade: API 5L X65
- Coating: Specialized high-build epoxy system
- Custom features: Integrated support brackets for service mounting
Critical Challenges:
Several tunnel sections required innovative support structures capable of withstanding extreme ground pressure while housing various service lines. The solution needed to maximize internal clearance while meeting stringent fire safety requirements.
حل WUZHOU
Working closely with the project’s structural engineers, WUZHOU developed:
- Custom large-diameter pipes with precisely calculated wall thickness profiles
- Reinforced sections at areas of maximum stress concentration
- Specialized fire-resistant coating systems exceeding safety standards
- Factory-installed mounting systems for services
Performance Results:
The tunnel support structure has:
- Maintained perfect dimensional stability despite ground pressure exceeding design assumptions
- Successfully supported all service lines without deflection or stress damage
- Passed all fire safety certification tests with superior performance
- Required zero remedial work since installation
Project Outcomes and Benefits
The integration of WUZHOU’s spiral welded pipe solutions throughout this major high-speed rail project delivered several quantifiable benefits:
Schedule Performance
- On-time delivery of all pipe components despite aggressive timeline
- 15% faster installation compared to alternative solutions initially considered
- Zero construction delays attributable to pipe supply or quality issues
- Project completion three months ahead of schedule
كفاءة التكلفة
- 12% reduction in total installed cost compared to initial estimates
- 30% reduction in labor hours for installation due to optimized pipe designs
- 22% decrease in material waste during installation
- Projected 40% reduction in maintenance costs over 30-year service life
Technical Performance
- All systems have maintained 100% functionality since commissioning
- Zero structural defects identified during comprehensive post-installation inspections
- Performance exceeding design specifications in hydraulic efficiency and load-bearing capacity
- Perfect interface compatibility with connecting infrastructure components
Sustainability Benefits
- 35% lower carbon footprint compared to alternative materials evaluated
- 100% recyclability at end of service life
- 25% reduction in excavation volumes due to optimized pipe designs
- Minimal disruption to sensitive ecosystems during installation
Client Testimony
The project’s Chief Infrastructure Engineer provided this assessment:
“WUZHOU’s spiral welded pipe solutions have proven instrumental to the success of this landmark high-speed rail project. From initial engineering consultation through manufacturing and delivery, their team demonstrated exceptional technical knowledge and commitment to quality. The performance of their products has exceeded our expectations in several critical areas, particularly structural integrity under high-speed train operations and resistance to our region’s extreme weather conditions.
“Most impressively, their ability to customize solutions for our unique challenges while maintaining adherence to our aggressive schedule demonstrated why they’ve earned their reputation as an industry leader. The long-term value their products offer through reduced maintenance requirements and extended service life has significantly enhanced the economic outlook for our operations.”
Engineering Analysis: Key Success Factors
A detailed post-implementation analysis identified several factors that contributed to the exceptional performance of WUZHOU’s spiral welded pipe solutions in this project:
- Material quality: The consistent chemical composition and mechanical properties of the base steel ensured uniform performance throughout the extensive pipe network.
- Manufacturing precision: The dimensional accuracy achieved by WUZHOU’s production facilities minimized field adjustments and ensured perfect alignment of components.
- Welding excellence: The double-sided submerged arc welding process created joints with exceptional strength and fatigue resistance, critical for the dynamic loading of high-speed rail operations.
- Coating performance: The advanced coating systems applied in WUZHOU’s specialized facilities have provided perfect protection even in the most aggressive environments along the corridor.
- Engineering optimization: The collaborative approach between WUZHOU’s technical team and the project engineers resulted in optimized specifications that balanced performance requirements with cost-efficiency.
- Quality assurance: The comprehensive testing protocols, including hydrostatic testing, ultrasonic examination, and X-ray inspection, ensured perfect structural integrity of every pipe component.
- Technical support: WUZHOU’s field engineers provided valuable guidance during critical installation phases, ensuring proper handling and installation techniques were employed.
This case study demonstrates the tangible benefits that WUZHOU’s premium spiral welded pipes bring to modern railway infrastructure projects. Their combination of manufacturing excellence, technical expertise, and commitment to quality delivers exceptional value across the entire project lifecycle—from initial design through decades of reliable service.
The Economic Impact of Quality Infrastructure: Beyond Direct Costs
While much of our discussion has focused on the technical advantages and direct cost benefits of quality spiral welded pipes, it’s important to recognize the broader economic implications of reliable railway infrastructure. This perspective is particularly relevant for decision-makers evaluating investments in premium components like WUZHOU’s spiral welded pipes.
Operational Reliability and Revenue Protection
Railway operations generate revenue only when trains are running safely and on schedule. Infrastructure failures cause:
- Direct revenue loss: Every hour of service interruption directly impacts fare revenue or freight charges
- Compensation costs: Many operators must provide compensation for delays beyond threshold limits
- Alternative transport costs: Arranging replacement transportation during outages
- Reputation damage: Long-term reduction in ridership or shipping contracts due to perceived unreliability
A single major drainage failure under a busy railway line can cause disruptions costing hundreds of thousands of dollars per day in direct losses, not counting long-term reputation damage. The premium cost of quality infrastructure components like WUZHOU’s spiral welded pipes typically represents a tiny fraction of these potential losses.
Asset Lifecycle Extension
Modern financial models for railway infrastructure increasingly focus on total lifecycle costs and asset longevity:
- Capital renewal deferral: Extended service life of key components delays costly replacement projects
- Depreciation advantages: Longer-lived assets can be depreciated over extended periods, improving financial performance
- Capacity improvement timing: Postponing replacements allows strategic timing of capacity enhancements
- Technology integration opportunities: Longer replacement intervals enable integration with emerging technologies
WUZHOU’s premium spiral welded pipes, with service lives exceeding 50 years, provide exceptional value in these lifecycle financial models, particularly when compared to alternatives requiring replacement at 25-30 year intervals.
Safety Risk Mitigation
Railway safety incidents carry enormous costs that far exceed any premium paid for quality infrastructure:
- Human costs: Potential injuries or fatalities from infrastructure failure
- Regulatory penalties: Increasing regulatory scrutiny and penalties for preventable incidents
- Insurance implications: Premium increases following safety incidents
- Investigation and remediation costs: Extensive analysis and system-wide corrections often required
- Legal liability: Potential litigation from affected parties
The exceptional quality control processes WUZHOU implements—including 100% hydrostatic testing, ultrasonic inspection, and X-ray examination—provide valuable risk mitigation against these catastrophic costs.
Capacity Utilization Optimization
Modern railways seek to maximize the capacity of existing corridors, which requires absolute confidence in infrastructure reliability:
- Headway reduction: Decreasing the spacing between trains requires complete trust in all infrastructure components
- Speed increases: Higher operating speeds increase forces on infrastructure, requiring premium components
- Operating hour extensions: Longer daily operating periods reduce maintenance windows, demanding more reliable components
- Weight limit increases: Heavier freight loads place additional demands on all infrastructure elements
WUZHOU’s spiral welded pipes, with their superior structural properties and exceptional quality assurance, provide the reliability foundation that enables these capacity optimization strategies.
Environmental and Social Cost Avoidance
Infrastructure failures often generate significant environmental and social costs:
- Environmental remediation: Failures in drainage or utility protection systems can cause environmental damage requiring costly cleanup
- Community disruption: Infrastructure repairs in populated areas create noise, access restrictions, and other community impacts
- Modal shift implications: Railway service disruptions often shift transportation to less environmentally friendly modes
- Resource wastage: Premature replacement of infrastructure components represents poor resource stewardship
The extended service life and exceptional reliability of WUZHOU’s spiral welded pipes help avoid these significant but often uncounted costs.
Enabling Economic Development
Perhaps most importantly, reliable railway infrastructure enables broader economic development:
- Business location decisions: Companies increasingly factor transportation reliability into location decisions
- Property value enhancement: Areas with reliable railway connections typically see increased property values
- Labor market expansion: Reliable commuter rail expands available labor markets for employers
- Tourism development: Visitor experiences depend heavily on transportation reliability
- Supply chain integrity: Modern logistics systems require predictable transportation performance
By providing a robust foundation for railway reliability, quality infrastructure components like WUZHOU’s spiral welded pipes contribute significantly to these broader economic benefits.
Looking Forward: Strategic Integration of Spiral Welded Pipes in Railway Development
As railway infrastructure continues to evolve in response to technological, economic, and environmental forces, the strategic integration of high-quality components becomes increasingly critical. Forward-thinking railway developers are already implementing advanced approaches that maximize the value of premium spiral welded pipes like those manufactured by WUZHOU.
Digital Twin Integration for Lifecycle Optimization
Leading railway organizations are creating comprehensive digital models of their physical infrastructure, with spiral welded pipe systems as key components:
- Real-time condition monitoring: Sensors embedded in or attached to critical pipe infrastructure provide continuous performance data
- Predictive maintenance modeling: AI algorithms analyze performance patterns to predict maintenance needs before failures occur
- Scenario planning: Digital models enable simulation of various operating scenarios and their impact on infrastructure
- Lifecycle optimization: Data-driven decision making maximizes component performance throughout its service life
WUZHOU is actively supporting these digital transformation initiatives by providing detailed material specifications, performance characteristics, and testing data that enhance the accuracy of digital models.
Climate Resilience Through Strategic Infrastructure Planning
Climate change is creating new challenges for railway infrastructure, with spiral welded pipe systems playing a crucial role in adaptation strategies:
- Enhanced drainage capacity: Upgrading culvert systems with larger diameter, higher-strength pipes to manage increasing precipitation intensity
- Coastal protection systems: Implementing specialized pipe systems to protect vulnerable coastal railways from rising sea levels
- Temperature-resilient designs: Developing pipe specifications that accommodate wider temperature fluctuations without compromise
- Fire-resistant corridors: Creating protective systems for railways in areas with increasing wildfire risk
WUZHOU’s engineering team works closely with railway developers to analyze these emerging climate risks and design appropriate spiral welded pipe solutions that enhance overall system resilience.
Integration with Smart Railway Systems
As railways become increasingly automated and digitally controlled, infrastructure components must integrate with these smart systems:
- Sensor-equipped pipe systems: Strategic monitoring points throughout drainage and utility networks
- Communication pathway protection: Hardened conduits for the fiber optic networks that enable smart railway operation
- Power distribution networks: Protected pathways for the electrical systems powering digital infrastructure
- Data collection nodes: Strategic access points for maintenance and monitoring of digital systems
WUZHOU is developing specialized versions of their spiral welded pipes designed specifically for these smart infrastructure applications, with features like integrated sensor mounting points and enhanced protection for sensitive electronic components.
Sustainability Leadership Through Lifecycle Management
Forward-thinking railway organizations are implementing comprehensive lifecycle management strategies for all infrastructure components:
- Material passport systems: Detailed documentation of all materials to facilitate future recycling
- Designed-for-disassembly approaches: Infrastructure planning that considers eventual component recovery
- Carbon footprint optimization: Selection of components based on total lifecycle carbon impact
- Circular economy integration: Development of systems for component refurbishment and reuse
WUZHOU supports these sustainability initiatives through detailed material documentation, recyclability guidelines, and carbon footprint information for their spiral welded pipe products.
Conclusion: The Strategic Advantage of Quality Infrastructure
As this comprehensive analysis has demonstrated, spiral welded pipes represent a critical component in modern railway infrastructure, with applications ranging from basic drainage to sophisticated structural systems. The quality, reliability, and longevity of these components directly impact the performance, economics, and sustainability of railway operations for decades after installation.
WUZHOU, with its state-of-the-art manufacturing facilities, comprehensive quality assurance systems, and railway-specific engineering expertise, stands as an ideal partner for railway organizations seeking to optimize their infrastructure investments. Their premium spiral welded pipes deliver exceptional value across the entire project lifecycle—from initial installation efficiency to decades of reliable performance with minimal maintenance requirements.
For railway developers, the decision to specify quality components like WUZHOU’s spiral welded pipes represents more than a procurement choice—it’s a strategic investment in operational excellence, economic sustainability, and environmental responsibility. As railway networks continue to expand globally and expectations for performance continue to rise, this commitment to infrastructure quality will increasingly differentiate successful operations from those struggling with reliability, maintenance costs, and service disruptions.
By partnering with WUZHOU for critical spiral welded pipe applications, railway organizations gain not just exceptional products, but a collaborative relationship with a manufacturer committed to advancing the state of the art in railway infrastructure. This partnership approach, combining WUZHOU’s manufacturing excellence with railway-specific engineering expertise, creates the foundation for safe, efficient, and sustainable rail transportation for generations to come.